Solutions for every business need
Growth comes in all shapes and sizes. Whether it’s smoother operations, sharper insights, higher revenue—or all of the above—we’ve got you covered
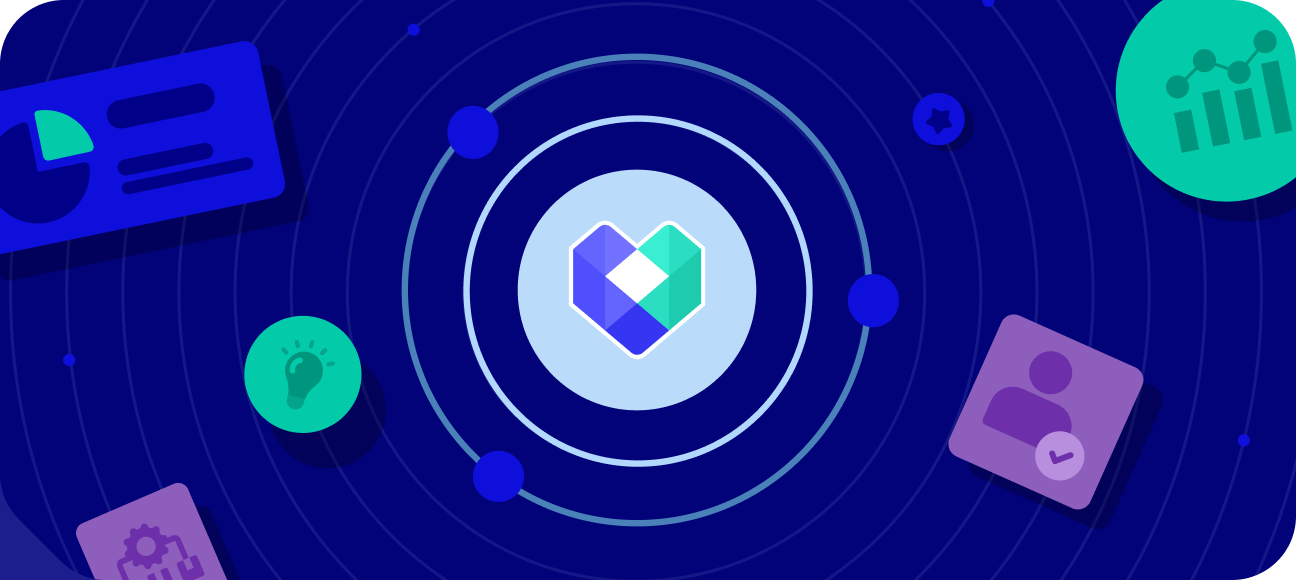
Warehouse management made simple
Gain full control over your inventory with smart automation, real-time tracking, and efficient workflows—ensuring your stock moves smoothly, every time
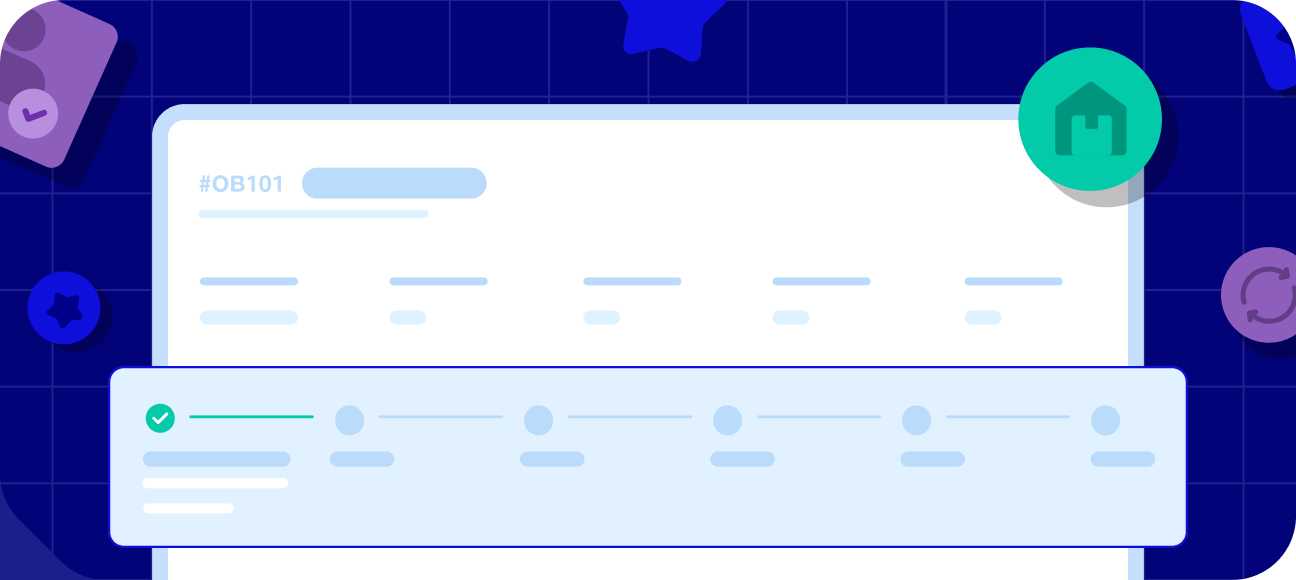
Launch hyperlocal commerce instantly
Set up and scale your hyper-local e-commerce with easy tools for web, orders, and delivery management—bringing you closer to customers, faster
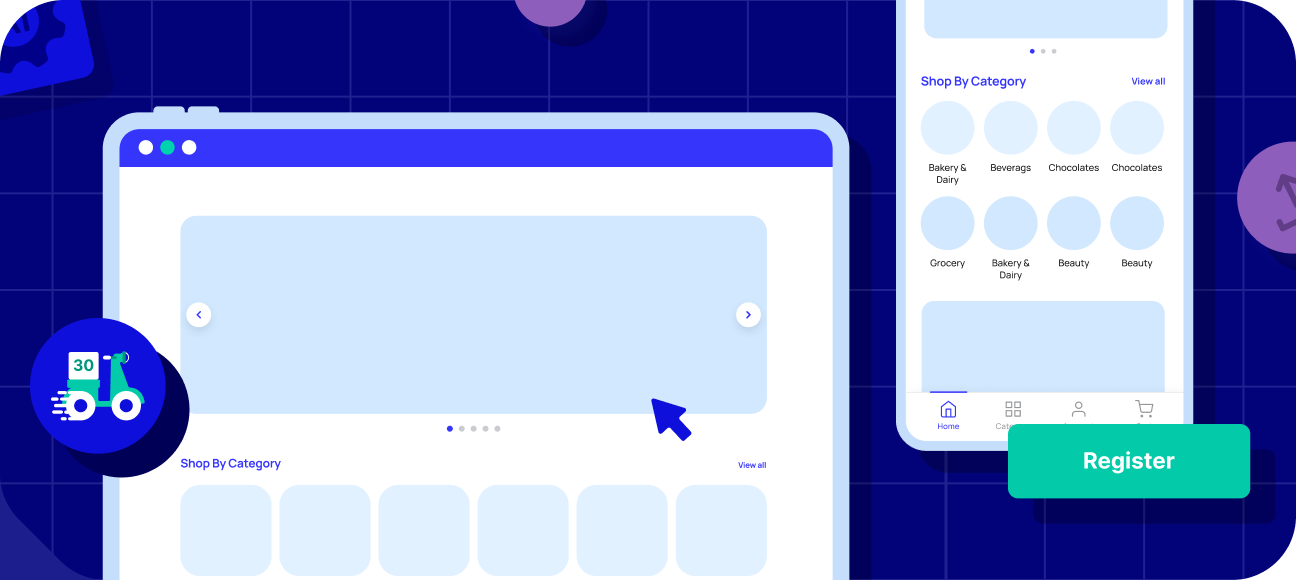
Delivery management made easy
Gain control over your deliveries with real-time visibility, smart automation, and seamless coordination—ensuring on-time arrivals, every time
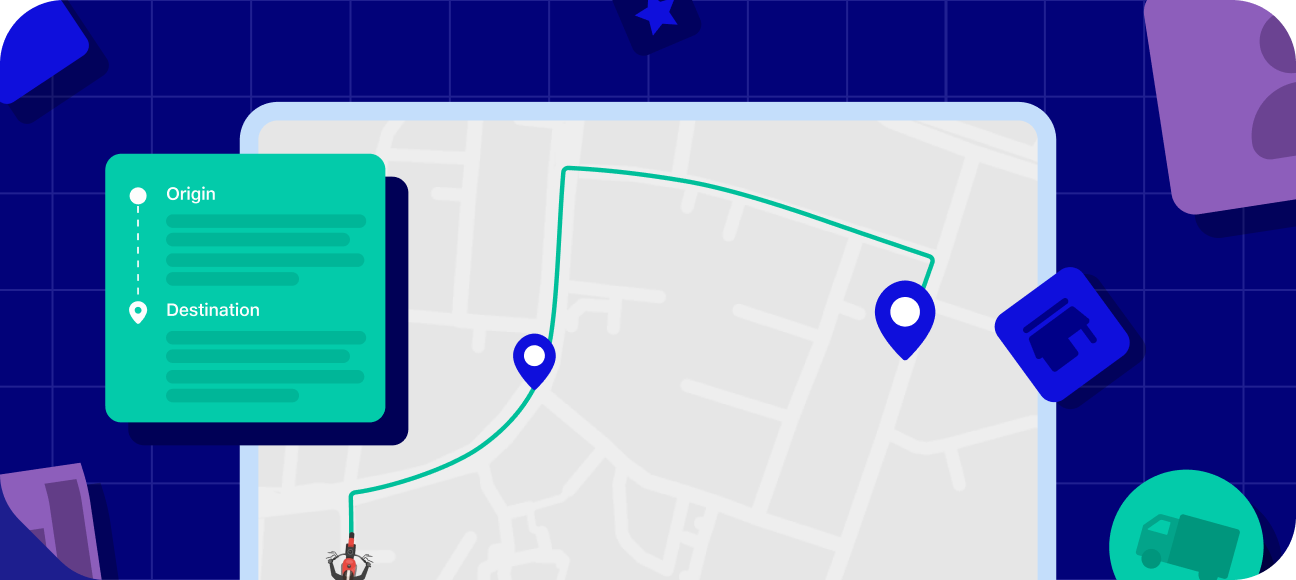
Order management made easy
Master every order with full visibility, smart automation, and effortless control—delivering the right outcomes, every time
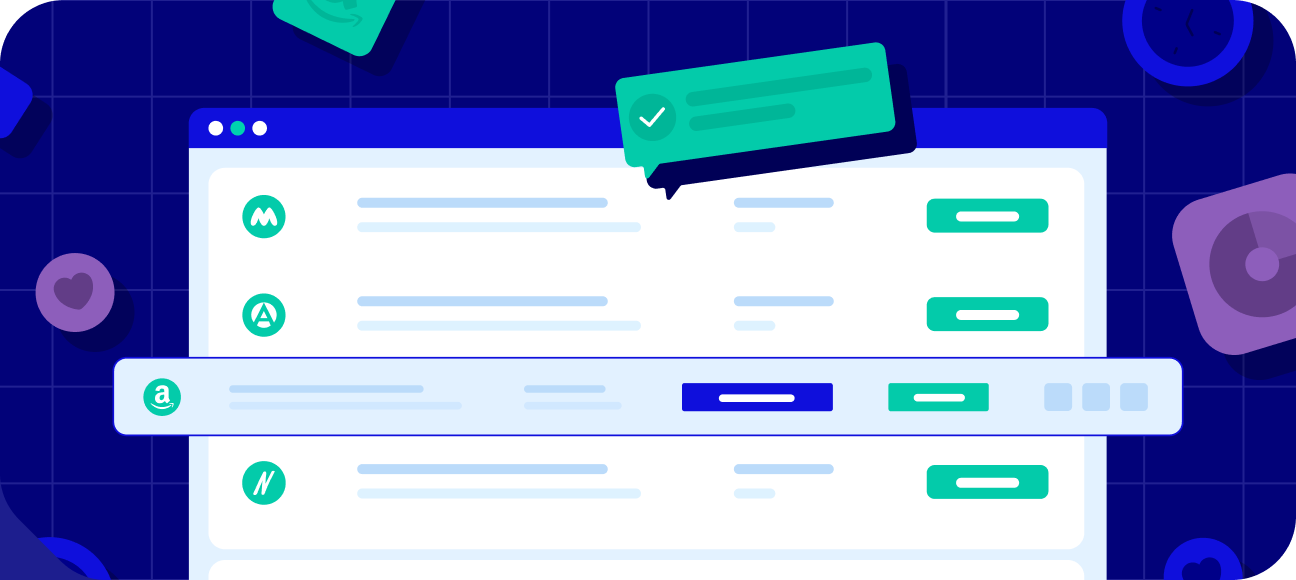
Speak to an expert
Explore how Fynd Commerce can improve every aspect of your business, from online to instore and beyond
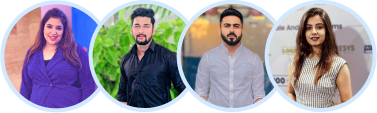
Speak to an expert
Explore how Fynd WMS powers operational excellence with our solution experts
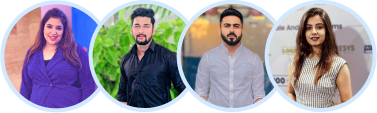
Speak to an expert
Explore how Fynd Quick powers hyperlocal businesses with our solution experts
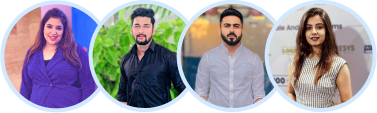
Speak to an expert
Explore how Fynd TMS powers better deliveries with our solution experts
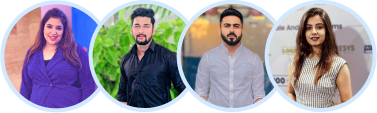
Speak to an expert
Explore how Fynd OMS powers seamless order management with our solution experts
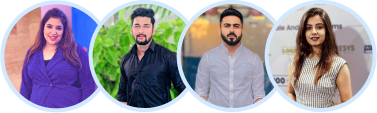
Featured Blog
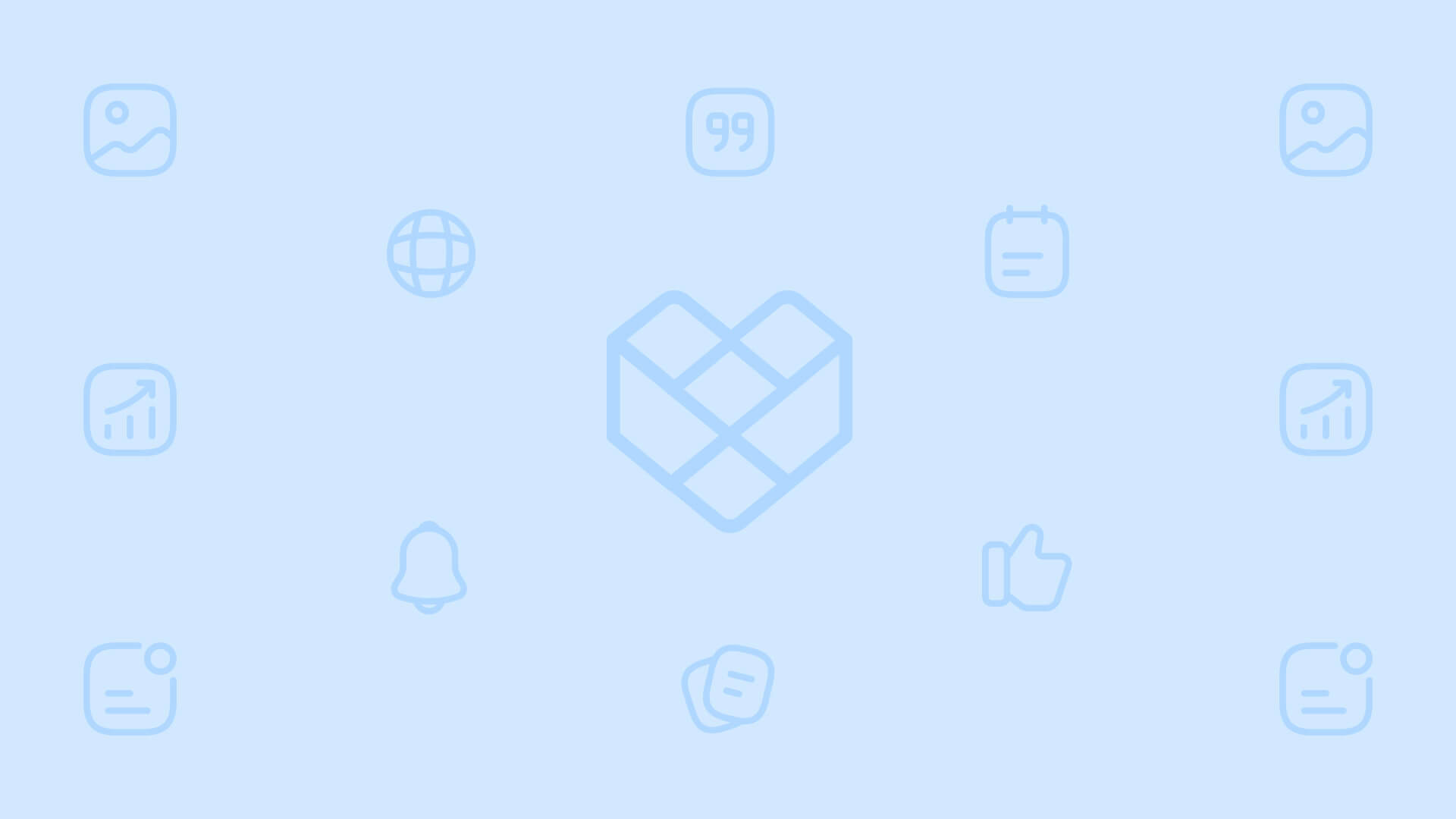
Empower your business, every step of the way
Simplify operations, scale smarter, and deliver better experiences with solutions designed to grow with your business
Take your warehouse management to the next level
Experience hassle-free inventory management with Fynd WMS, designed to keep your operations efficient and accurate. Book a demo to see how Fynd WMS can boost productivity and profits for your business!
Kickstart your quick delivery website
Experience seamless hyper-local commerce with Fynd Quick—engineered to keep things running smoothly and help you reach customers in record time. Book a demo and see how Fynd Quick can drive efficiency and growth for your business!
Level up your delivery management
See how you can manage deliveries with Fynd TMS, designed to streamline operations and keep your customers delighted. Book a demo with our team and find out how Fynd TMS can boost your efficiency and bottom line!
Take your order management to the next level
Discover how effortless order management can be with Fynd OMS, built to keep things running smoothly and make your customers happy. Book a demo with our team and see how Fynd OMS can help boost your efficiency and profits!
WMS integration refers to the process of connecting a Warehouse Management System (WMS) with other business-critical systems such as ERP, TMS, or e-commerce platforms to improve operational efficiency. With over 85% of companies aiming to digitize their supply chain by 2025, integrated systems are becoming a necessity. By ensuring real-time data flow across systems, WMS integration helps streamline inventory management, reduce manual errors, and improve overall supply chain visibility.
One key benefit of WMS integration is its ability to reduce operational costs by as much as 20%, thanks to optimized workflows and better inventory tracking. Seamless communication between WMS and ERP systems enables faster order fulfillment while integrating with transportation management systems (TMS) improves shipping efficiency by up to 25%. This allows businesses to reduce lead times and ensure accurate deliveries. Moreover, integrations with e-commerce platforms help maintain real-time inventory updates, minimizing stockouts and overstock situations.
For businesses looking to enhance warehouse performance, the Fynd platform offers a flexible and scalable WMS solution that can be easily integrated with various systems. By adopting Fynd's WMS, companies can ensure that their warehouse operations are fully aligned with their broader business goals, enabling smarter decision-making and a more agile supply chain.
What is WMS Integration?
A Warehouse Management System (WMS) is software designed to manage and control daily warehouse operations, such as inventory tracking, order picking, packing, and shipping. It helps businesses streamline their warehousing processes, improve accuracy, and boost operational efficiency.
WMS integration refers to connecting the WMS with other essential systems like Enterprise Resource Planning (ERP), Transportation Management Systems (TMS), and e-commerce platforms. This integration allows for the seamless flow of information between systems, reducing manual data entry, minimizing errors, and improving decision-making. By integrating a WMS with other systems, businesses can automate workflows, gain real-time inventory visibility, optimize resource allocation, and enhance overall warehouse performance, resulting in smoother operations and cost savings.
Why is WMS Integration Important?
WMS integration is the process of connecting a Warehouse Management System (WMS) with other essential business systems like ERP, TMS, or e-commerce platforms. This integration allows data to flow seamlessly between systems, reducing manual tasks and minimizing errors. It improves warehouse operations by providing real-time inventory updates, streamlining workflows, and enhancing decision-making. WMS integration also speeds up order fulfillment, leading to faster shipping and better customer satisfaction. Additionally, it helps businesses reduce operational costs by optimizing resource allocation and improving overall efficiency across the supply chain.
- Streamlined Operations: Integration ensures seamless communication between systems, improving overall warehouse efficiency.
- Real-time Data: It provides up-to-date inventory information, enabling better decision-making.
- Reduced Errors: Automation reduces the need for manual data entry, lowering the risk of mistakes.
- Faster Order Fulfillment: Integrated systems speed up the order processing and shipping cycle.
- Cost Efficiency: By optimizing workflows, WMS integration helps reduce operational costs.
- Improved Inventory Management: Integration ensures accurate tracking of stock levels, preventing overstocking or stockouts.
- Enhanced Customer Experience: Faster and more accurate order fulfillment leads to improved customer satisfaction and retention.
- Better Scalability: WMS integration allows businesses to easily scale operations as they grow or expand into new markets.
- Data Synchronization: Real-time data synchronization across systems ensures that all departments have access to the same updated information.
- Compliance and Reporting: Integrated systems help businesses stay compliant with industry regulations and generate reports more efficiently.
- Increased Productivity: Automation of tasks like inventory updates and order tracking frees up staff for more strategic activities.
Types of WMS Integration
WMS integration involves different methods to connect a Warehouse Management System (WMS) with other crucial business systems, creating a unified operational environment. Each type of WMS integration addresses specific business needs and workflows, allowing companies to choose the most effective methods for improving efficiency, streamlining processes, and optimizing their supply chain.
Understanding these various integration types is essential for organizations looking to enhance their warehouse operations and ensure seamless communication between systems. Below are some key types of WMS integration:
1. ERP Integration
Integrating a Warehouse Management System with an Enterprise Resource Planning system creates a seamless connection that allows businesses to synchronize crucial data across financial, inventory, and order management platforms. This integration ensures that all departments—from sales to finance—are aligned and can access real-time information, leading to more informed decision-making. Additionally, it automates routine tasks like invoicing, financial reporting, and inventory management, which reduces manual errors and improves operational efficiency.
2. TMS Integration
Connecting a Warehouse Management System with a Transportation Management System optimizes the shipping process by improving key logistics functions like route planning, load optimization, and carrier management. This integration facilitates real-time visibility into shipment statuses, allowing businesses to monitor deliveries and respond quickly to any changes in logistics or unexpected delays. By enhancing communication between warehousing and transportation teams, this integration can reduce transit times and lower overall shipping costs.
3. E-commerce Platform Integration
Integrating a WMS with e-commerce platforms creates a vital link that allows for real-time inventory updates and order processing directly from online sales channels. This connection not only enhances the customer experience by ensuring accurate stock levels are displayed but also automates order fulfillment processes, significantly reducing manual data entry. As a result, orders can be processed and shipped more quickly, minimizing delays and improving accuracy.
4. Barcode and RFID System Integration
Connecting a Warehouse Management System (WMS) to barcode scanners or RFID systems significantly enhances inventory accuracy and efficiency in product tracking. This integration automates data collection during crucial processes like picking, packing, and shipping, which reduces manual errors and minimizes labor costs. By streamlining inventory counts and providing better control over stock levels, businesses can improve their overall warehouse productivity.
5. EDI Integration
Electronic Data Interchange (EDI) integration enables the automated exchange of essential business documents, such as purchase orders, invoices, and shipment notifications, between companies and their trading partners. This integration streamlines communication across the supply chain, significantly reducing paperwork and manual data entry. It accelerates transaction processing, enhances accuracy, and ensures that all parties have access to the same up-to-date information.
Benefits of Integrating WMS with Other Systems
Integrating a Warehouse Management System (WMS) with other key business systems offers numerous advantages that can significantly enhance operational efficiency and productivity across various departments. By creating a connected environment, businesses can streamline processes, improve data accuracy, and facilitate better communication among teams.
This integration not only helps organizations adapt quickly to market changes and respond to customer demands more effectively but also drives profitability by optimizing resource utilization. Below are some of the key benefits of integrating WMS with other systems that can transform business operations for the better:
1. Enhanced Inventory Accuracy
Integrating WMS with systems like ERP and barcode scanning solutions significantly improves inventory accuracy through real-time data updates. Automated tracking of stock levels ensures that inventory records reflect actual quantities, minimizing discrepancies and preventing stockouts or overstock situations. Enhanced inventory management not only boosts operational efficiency but also elevates customer satisfaction by guaranteeing that products are available when needed, ultimately fostering trust and loyalty among customers.
2. Improved Order Fulfillment
When WMS integrates with order management and e-commerce platforms, businesses can streamline their order fulfillment processes more effectively. This integration facilitates quicker processing of orders, ensuring that items are picked, packed, and shipped promptly. Consequently, customers receive their orders on time, resulting in heightened satisfaction and increased chances of repeat business. Efficient order fulfillment also helps reduce operational costs related to delays and errors, ultimately enhancing the bottom line.
3. Streamlined Communication
Integrating WMS with other systems fosters better communication between departments such as warehousing, sales, and finance. This seamless flow of information guarantees that all teams have access to the same data, promoting collaboration and reducing misunderstandings. Improved communication leads to more coordinated efforts in areas like inventory management, order processing, and customer service. As a result, overall operational efficiency is enhanced, benefiting the entire organization.
4. Cost Reduction
Integrating WMS with other key systems enables businesses to identify cost-saving opportunities and optimize their operations effectively. Improved inventory management, for instance, leads to reduced carrying costs, while streamlined order fulfillment helps lower labor expenses. Additionally, automation minimizes manual data entry, decreasing the potential for errors and associated costs. Overall, this integration empowers organizations to operate more efficiently and allocate resources more effectively, contributing to a healthier bottom line.
5. Better Data Insights
WMS integration equips businesses with access to valuable data and analytics that can guide strategic decision-making. By consolidating information from various sources, organizations can gain insights into inventory turnover, order trends, and customer preferences. This data-driven approach empowers businesses to make informed decisions regarding inventory management, pricing strategies, and marketing efforts. Ultimately, these insights lead to improved profitability and a competitive edge in the marketplace.
6. Increased Operational Efficiency
Integrating WMS with other key systems automates numerous processes, such as order processing, inventory management, and shipping. This automation reduces manual tasks, enabling employees to focus on higher-value activities. Consequently, organizations can increase their overall operational efficiency, speeding up workflows and reducing cycle times. As processes become more streamlined, businesses can handle higher volumes of work without the need for additional resources, ultimately enhancing productivity.
7. Enhanced Customer Experience
WMS integration improves the customer experience by ensuring accurate order processing and timely deliveries. When businesses have real-time access to inventory data and order status, they can provide customers with up-to-date information regarding their purchases. This transparency fosters trust and satisfaction, encouraging repeat business and positive word-of-mouth referrals. By delivering consistent, high-quality service, organizations can cultivate long-lasting customer relationships.
8. Scalability and Flexibility
Integrating WMS with other systems provides businesses with the scalability and flexibility needed to adapt to changing market demands. As organizations grow or expand into new markets, integrated systems allow for easier adjustments in operations, such as adding new warehouse locations or updating inventory practices. This adaptability helps companies stay competitive and meet evolving customer expectations without significant disruptions.
9. Improved Compliance and Reporting
WMS integration helps businesses maintain compliance with industry regulations by automating record-keeping and reporting processes. By consolidating data from various sources, organizations can generate accurate reports required for regulatory compliance and audits. This automation minimizes the risk of errors associated with manual reporting, ensuring that businesses meet legal requirements efficiently. Enhanced compliance management can also protect businesses from potential fines and penalties.
10. Better Forecasting and Planning
WMS integration enhances forecasting and planning capabilities by providing accurate, real-time data about inventory levels, order patterns, and customer behavior. This information allows businesses to anticipate demand more effectively and plan their inventory and staffing needs accordingly. Better forecasting minimizes excess inventory and stockouts, leading to more efficient operations and improved customer satisfaction.
11. Enhanced Supply Chain Collaboration
Integrating WMS with other business systems fosters better collaboration among supply chain partners, including suppliers, distributors, and retailers. By sharing real-time data, organizations can coordinate efforts more effectively, improving visibility and responsiveness throughout the supply chain. Enhanced collaboration leads to reduced lead times, optimized inventory levels, and improved service levels, benefiting all parties involved.
12. Increased Accuracy in Demand Planning
WMS integration allows for the collection and analysis of data from various sales channels, enabling more accurate demand planning. By understanding customer buying patterns and preferences, businesses can optimize inventory levels to align with anticipated demand. This accuracy reduces the risk of overstocking or understocking, ultimately leading to improved financial performance and customer satisfaction.
Best Practices for WMS Integration in 2024
In 2024, integrating a Warehouse Management System (WMS) with other business systems is essential for enhancing efficiency and productivity. To achieve successful integration, businesses need to follow best practices that ensure smooth connections between systems. These practices help minimize disruptions, enhance data accuracy, and optimize workflows. By focusing on the right strategies, organizations can improve inventory management, order fulfillment, and overall operational performance. Below are some key best practices for WMS integration in 2024:
1. Assess Business Needs
Before starting the integration process, it’s important to thoroughly evaluate your business needs and objectives. This involves identifying which systems need to be integrated and defining the specific functionalities required for your operations. A clear understanding of your goals will help you create a focused integration strategy that aligns with your organization’s objectives, enhances productivity, and ultimately improves overall efficiency in your supply chain management processes.
2. Choose the Right Integration Tools
Selecting the right integration tools is crucial for successful WMS integration. Take the time to evaluate different options based on your existing systems, their scalability, and ease of use. Choosing robust integration platforms can greatly simplify the integration process, ensuring compatibility across different systems. By facilitating seamless data flow between your WMS and other applications, these tools enhance operational performance and support better decision-making throughout the organization.
3. Prioritize Data Accuracy
Ensuring data accuracy is essential for effective WMS integration. Implementing strong data validation protocols is crucial to minimize errors during the integration process. Regularly auditing and cleansing data will ensure that it remains accurate and up-to-date, thus avoiding costly mistakes. High-quality data not only improves decision-making but also enhances inventory management, enabling organizations to better serve their customers and increase overall satisfaction through reliable service delivery.
4. Implement Real-Time Tracking
Integrating real-time tracking capabilities into your WMS is vital for maintaining up-to-date information on inventory levels and order status. This enhanced visibility empowers organizations to respond quickly to changes in demand and improves overall operational efficiency. Real-time tracking not only streamlines communication among team members but also provides customers with accurate information regarding their orders, thereby enhancing customer satisfaction and fostering long-term loyalty.
5. Train Employees
Providing comprehensive training for employees on the integrated system is crucial for a successful implementation. Ensure that all staff members fully understand how to use the new tools and processes effectively. Regular training sessions and ongoing support will help employees adapt to any changes, optimize their performance, and build confidence in using the integrated system. This commitment to training ultimately leads to better operational outcomes and enhances overall team productivity.
6. Test Before Full Implementation
Conducting thorough testing of the integration before rolling it out across the organization is essential. This testing phase allows you to identify and address any potential issues proactively. By testing the integration in a controlled environment, you can ensure that all systems work together smoothly and efficiently. This meticulous approach minimizes disruptions during the transition and sets a strong foundation for successful integration and operational performance in the long run.
7. Monitor and Optimize Performance
Once the integration is complete, it’s crucial to continuously monitor the performance of the WMS and other connected systems. Track key performance indicators (KPIs) to assess how well the integration meets your business objectives and operational goals. Using insights gained from this monitoring, you can make necessary adjustments and optimize workflows, ensuring sustained efficiency and productivity while adapting to evolving market demands and customer expectations.
8. Maintain Strong Vendor Relationships
Establishing and maintaining strong relationships with your WMS and integration tool vendors is vital for ongoing success. Open communication facilitates prompt support and access to software updates, enhancing the integration’s performance. Collaborating closely with vendors can also provide valuable insights into best practices, new features, and emerging industry trends. This proactive engagement helps ensure that your operations continue to improve and adapt to changing business environments.
Challenges in WMS Integration
Integrating a Warehouse Management System (WMS) with other business systems can greatly enhance operational efficiency, but it also comes with its set of challenges. Businesses often encounter hurdles such as data compatibility issues, resistance to change, and the complexity of integration processes. These challenges can hinder the successful implementation of WMS integration, affecting overall productivity and performance.
Understanding these potential obstacles is essential for organizations to prepare effectively and develop strategies to overcome them. Here are some key challenges in WMS integration:
1. Data Compatibility Issues
Data compatibility issues arise when different systems use varying data formats or structures, making it difficult for them to communicate effectively. Inconsistent data types can lead to errors in data exchange, causing inaccuracies in inventory records and order processing. This challenge often requires additional time and resources to resolve, as organizations may need to standardize data formats or utilize middleware solutions to facilitate seamless integration.
2. Resistance to Change
Employees may resist changes brought about by WMS integration due to fear of the unknown or concerns about their ability to adapt to new processes. This resistance can slow down the integration process and affect morale, leading to decreased productivity. To address this challenge, organizations should prioritize communication and training, helping employees understand the benefits of integration and equipping them with the necessary skills to navigate the new system.
3. Complexity of Integration Processes
The integration process itself can be complex, involving multiple systems, stakeholders, and technologies. This complexity increases the risk of errors and delays, as businesses must coordinate various components to ensure a successful integration. Organizations may need to invest in expert resources or consultants to manage this complexity effectively, adding to the overall cost and time required for implementation.
4. Limited IT Resources
Many organizations face limitations in their IT resources, which can hinder the successful integration of WMS with other systems. Insufficient personnel, budget constraints, and outdated technology can create barriers to effective implementation. Businesses may need to allocate additional resources or seek external support to address these limitations, ensuring they have the necessary capabilities to complete the integration smoothly.
5. Security Concerns
Integrating multiple systems can introduce security vulnerabilities, particularly when sensitive data is shared across platforms. Organizations must ensure that proper security protocols and measures are in place to protect against potential data breaches. This challenge requires ongoing monitoring and updates to security systems, as well as training employees on best practices for data security during the integration process.
Conclusion
While WMS integration offers numerous benefits, it also presents significant challenges that organizations must navigate to ensure successful implementation. By understanding these hurdles and employing best practices, businesses can enhance their operational efficiency and productivity. A well-integrated WMS not only streamlines warehouse processes but also supports better decision-making and customer satisfaction. For companies looking to optimize their warehouse management, Fynd offers a robust WMS solution designed to seamlessly integrate with your existing systems, driving efficiency and growth in your operations.
Frequently asked questions
WMS integration is the process of connecting a Warehouse Management System with other business systems, such as ERP, TMS, or e-commerce platforms. This connection facilitates seamless data flow, automates processes, and improves operational efficiency.
Integrating WMS enhances inventory accuracy, improves order fulfillment, streamlines communication, reduces costs, and provides better data insights. These benefits lead to increased efficiency and customer satisfaction in warehouse operations.
Common challenges include data inconsistency, system compatibility issues, employee resistance to change, and the complexity of the integration process. Addressing these challenges requires thorough planning and testing to ensure a smooth transition.
To maintain data accuracy, establish validation protocols, regularly audit data, and cleanse outdated information. High-quality data is essential for effective decision-making and overall operational success.
Best practices include assessing business needs, choosing the right integration tools, prioritizing data accuracy, training employees, testing before full implementation, and continuously monitoring performance to optimize workflows.
Fynd offers a robust Warehouse Management System designed for seamless integration with existing business systems. With expert support and customizable solutions, Fynd helps businesses enhance their warehouse operations and achieve greater efficiency.