Solutions for every business need
Growth comes in all shapes and sizes. Whether it’s smoother operations, sharper insights, higher revenue—or all of the above—we’ve got you covered
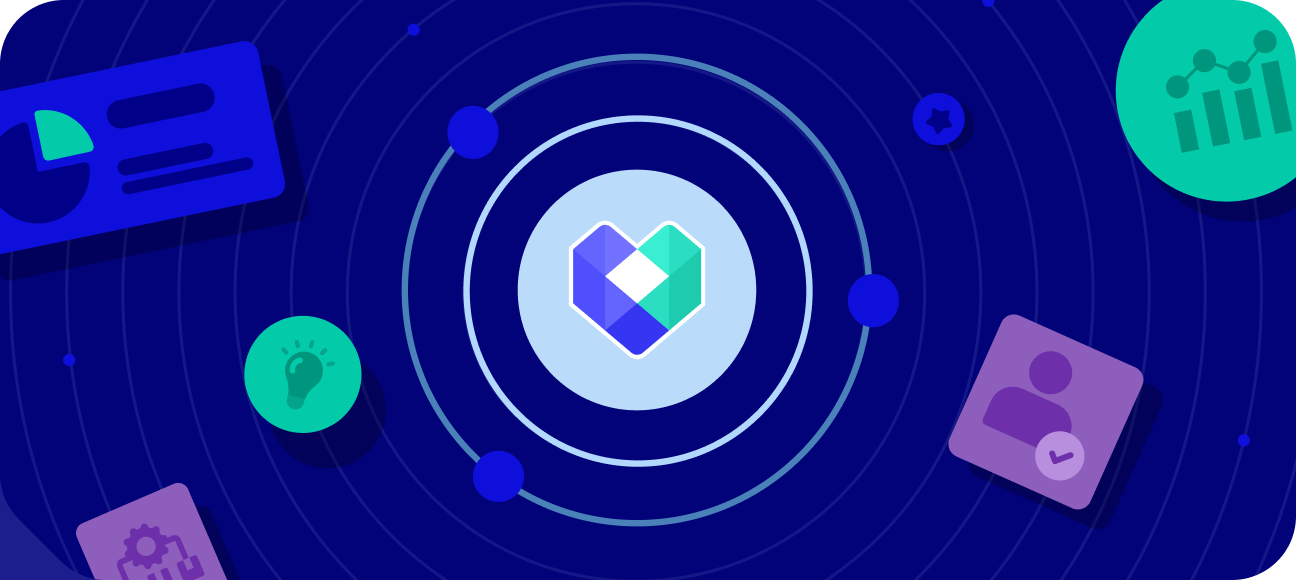
Warehouse management made simple
Gain full control over your inventory with smart automation, real-time tracking, and efficient workflows—ensuring your stock moves smoothly, every time
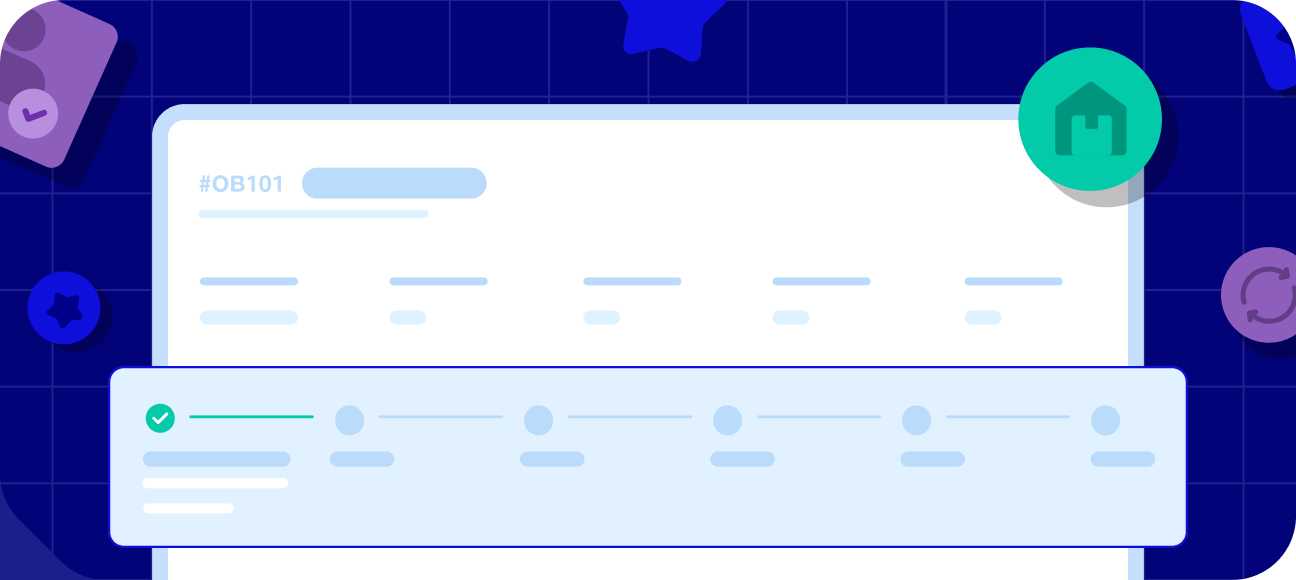
Launch hyperlocal commerce instantly
Set up and scale your hyper-local e-commerce with easy tools for web, orders, and delivery management—bringing you closer to customers, faster
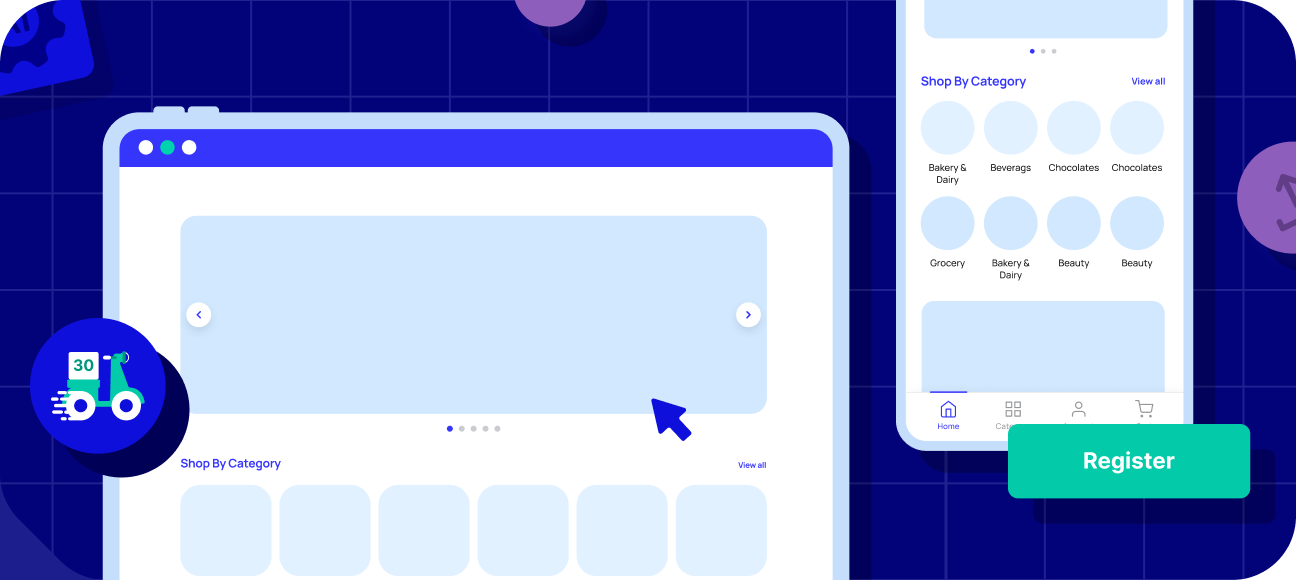
Delivery management made easy
Gain control over your deliveries with real-time visibility, smart automation, and seamless coordination—ensuring on-time arrivals, every time
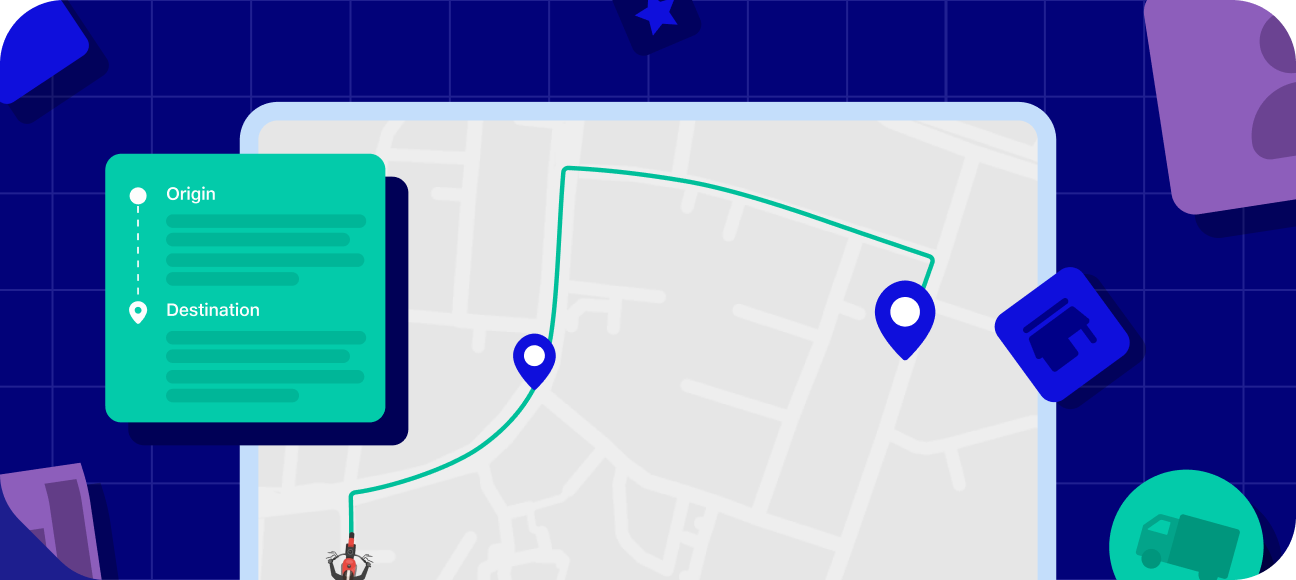
Order management made easy
Master every order with full visibility, smart automation, and effortless control—delivering the right outcomes, every time
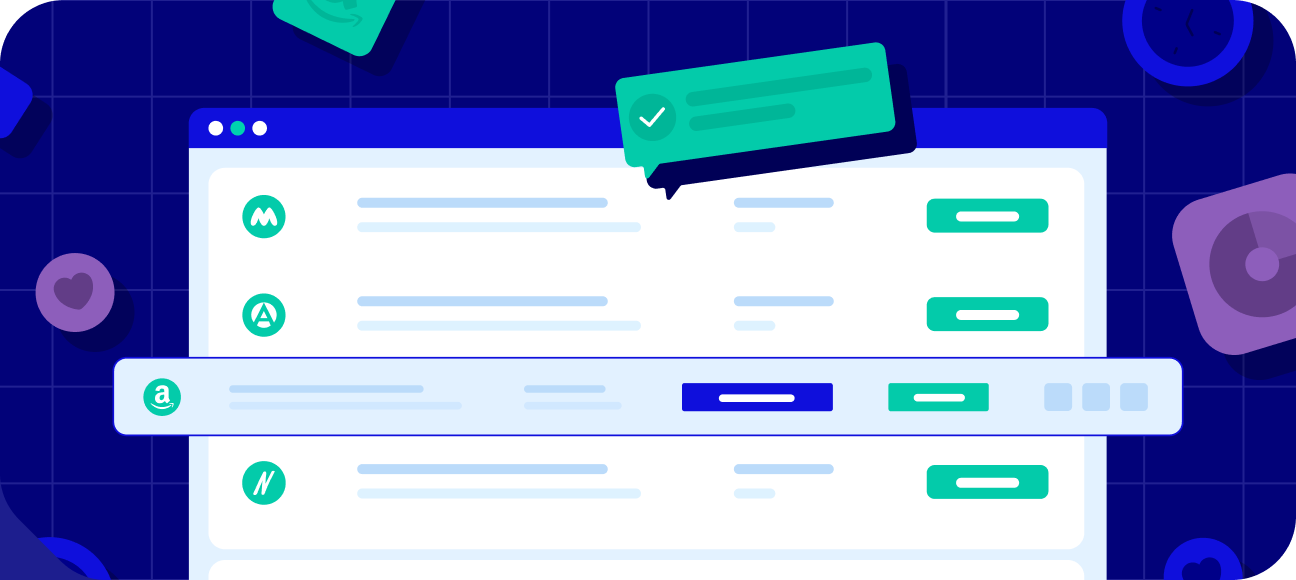
Speak to an expert
Explore how Fynd Commerce can improve every aspect of your business, from online to instore and beyond
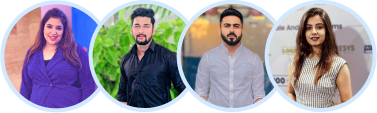
Speak to an expert
Explore how Fynd WMS powers operational excellence with our solution experts
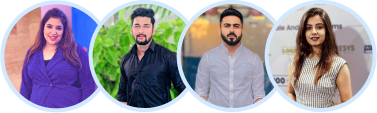
Speak to an expert
Explore how Fynd Quick powers hyperlocal businesses with our solution experts
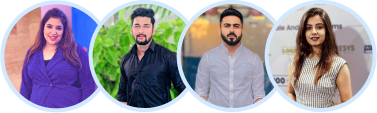
Speak to an expert
Explore how Fynd TMS powers better deliveries with our solution experts
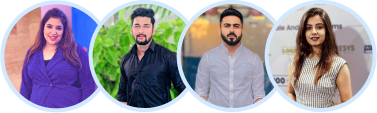
Speak to an expert
Explore how Fynd OMS powers seamless order management with our solution experts
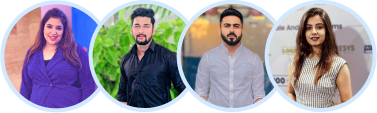
Featured Blog
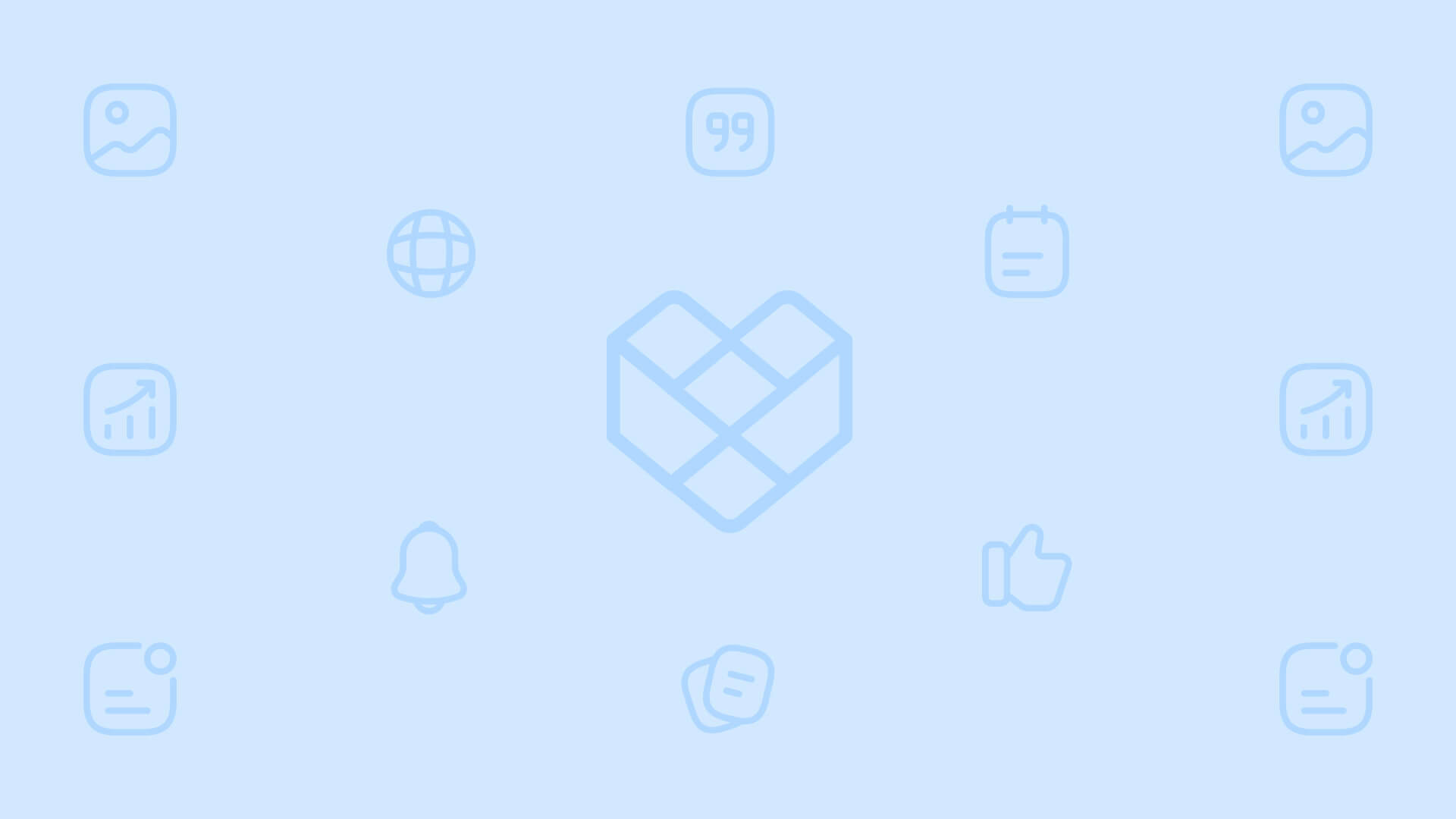
Empower your business, every step of the way
Simplify operations, scale smarter, and deliver better experiences with solutions designed to grow with your business
Take your warehouse management to the next level
Experience hassle-free inventory management with Fynd WMS, designed to keep your operations efficient and accurate. Book a demo to see how Fynd WMS can boost productivity and profits for your business!
Kickstart your quick delivery website
Experience seamless hyper-local commerce with Fynd Quick—engineered to keep things running smoothly and help you reach customers in record time. Book a demo and see how Fynd Quick can drive efficiency and growth for your business!
Level up your delivery management
See how you can manage deliveries with Fynd TMS, designed to streamline operations and keep your customers delighted. Book a demo with our team and find out how Fynd TMS can boost your efficiency and bottom line!
Take your order management to the next level
Discover how effortless order management can be with Fynd OMS, built to keep things running smoothly and make your customers happy. Book a demo with our team and see how Fynd OMS can help boost your efficiency and profits!
Implementing a Warehouse Management System (WMS) is crucial for businesses looking to streamline their operations. According to industry reports, companies that adopt WMS can achieve up to a 20% reduction in operational costs and a 30% increase in inventory accuracy. A WMS automates various processes, from receiving and storing inventory to order fulfillment and shipping, allowing businesses to maximize efficiency and minimize errors.
The WMS implementation process typically involves several key steps: planning, designing, configuring, testing, training, and going live. During the planning phase, it’s essential to assess your current systems and processes to identify specific needs and goals. For example, a retailer like Amazon uses advanced WMS technology to manage millions of items across multiple warehouses, showcasing the scalability and effectiveness of WMS solutions in handling high volumes.
By addressing challenges such as inventory discrepancies and inefficient order processing, a well-implemented WMS can significantly enhance operational performance. Fynd WMS offers a comprehensive solution that simplifies the implementation process, ensuring that businesses can harness the full potential of their warehouse operations. With its user-friendly interface and robust features, Fynd WMS stands out as a reliable partner for your WMS implementation journey.
Understanding the Warehouse Management System
A Warehouse Management System (WMS) is a specialized software solution that helps businesses manage their warehouse operations more effectively. It streamlines processes such as inventory tracking, order fulfillment, and shipping, ensuring that goods are stored, retrieved, and delivered efficiently. The importance of a WMS cannot be overstated, as it enables companies to optimize their warehouse space, reduce errors, and save time.
By providing real-time data on inventory levels and locations, a WMS helps businesses make informed decisions and respond quickly to customer demands. In a competitive market, having a reliable WMS is essential for improving operational efficiency and enhancing customer satisfaction. Overall, implementing a WMS can lead to significant cost savings and a more organized warehouse environment.
A Step-by-Step Guide to Implementation of WMS
Implementing a Warehouse Management System (WMS) can greatly improve your warehouse operations by streamlining processes and enhancing accuracy. This step-by-step guide will walk you through the crucial stages of WMS implementation, starting with an assessment of your current practices and culminating in the go-live phase.
Each step is designed to help businesses transition smoothly to a more organized and efficient warehouse management process. By following these guidelines, companies can expect to see increased productivity, reduced errors, and improved customer satisfaction, ultimately maximizing the overall effectiveness of their warehouse operations.
Step 1: Assess Current Processes
Start by thoroughly evaluating your existing warehouse operations, focusing on workflows, inventory management, order processing, and communication channels. Engage key stakeholders, including warehouse managers and staff, to gather insights on strengths and weaknesses. Document pain points, such as order inaccuracies and delays, to understand specific challenges. This assessment will set the foundation for establishing realistic goals and ensuring that the new WMS effectively addresses the identified issues.
Step 2: Define Requirements
Once you’ve assessed your current processes, compile a comprehensive list of requirements for the WMS. Include essential features like inventory tracking, order management, and reporting capabilities, ensuring integration with other systems, such as ERP software. Involve various departments—finance, operations, and IT—to gather diverse perspectives. Consider scalability, user-friendliness, and customization options. A clear and detailed requirements list will guide you in selecting the right WMS tailored to your business needs.
Step 3: Select a WMS Vendor
Research potential WMS vendors by comparing their offerings, customer reviews, and support services. Look for vendors with a strong track record in your industry and those offering customizable solutions. Request demonstrations to see how their software performs in real-world scenarios. Evaluate their commitment to customer support and training, as these are crucial during and after implementation. Selecting the right vendor is essential for ensuring a successful WMS implementation.
Step 4: Design and Configure the System
Work closely with your chosen vendor to design and configure the WMS according to your warehouse layout and operational processes. This may include mapping out storage locations and setting up inventory management rules. Customize the system to fit your workflows, such as order picking and packing methods. Engage key personnel during this phase to ensure the design meets operational needs. Consider implementing automation features like barcode scanning for accuracy.
Step 5: Conduct Testing
Conduct comprehensive testing to identify any issues or areas for improvement. This includes both functional testing, ensuring all features operate correctly, and user acceptance testing with actual users. Involve key stakeholders to gather feedback on usability and functionality. Address any problems identified during testing and refine the system accordingly. Consider running parallel operations where both the old and new systems are used temporarily to validate results and ensure accuracy.
Step 6: Develop a Change Management Plan
Creating a change management plan is vital for a smooth transition to the new WMS. This plan should detail how changes will be communicated to staff, the training schedule, and available support. Clearly outline the benefits of the new system and how it will positively impact employees' tasks. Address potential concerns to reassure employees. Involving them early in the process helps mitigate resistance to change and fosters a collaborative environment.
Step 7: Train Employees
Provide thorough training for all employees who will be using the WMS. This training should cover system navigation, order processing, inventory management, and reporting features. Use various training methods, such as hands-on sessions, online tutorials, and user manuals, to cater to different learning styles. Incorporate real-life scenarios to help employees understand the system's impact on their daily work. Ongoing support resources, like a help desk, will enhance user confidence.
Step 8: Go Live
Once testing and training are complete, it’s time to go live with the WMS. Launch the system during a low-activity period to minimize disruptions. Closely monitor the implementation, focusing on system performance and user feedback. Address immediate challenges as they arise and provide necessary support to employees adjusting to the new system. A well-planned communication strategy will keep all stakeholders informed about progress and any encountered issues during the transition.
Step 9: Monitor Performance Metrics
After going live, establish key performance indicators (KPIs) to measure the WMS's effectiveness. Common KPIs include order accuracy rates, inventory turnover, shipping times, and employee productivity. Regularly analyze these metrics to assess the new system's impact on warehouse operations. Set performance benchmarks and compare them against historical data to identify improvements and areas needing further attention, ensuring the WMS continues to meet business goals.
Step 10: Gather User Feedback
After the WMS has been operational for several weeks or months, collect feedback from users to assess their experiences. Conduct surveys, hold feedback sessions, or use suggestion boxes to gather insights. Inquire about challenges they face and features they find particularly useful. This feedback is invaluable for making necessary adjustments and improvements, ensuring the WMS effectively meets user needs and enhances overall warehouse operations.
Step 11: Evaluate and Optimize
Regularly assess the WMS’s performance against your initial goals and objectives. Gather user feedback to identify pain points or areas needing improvement. Conduct periodic evaluations of inventory accuracy, order fulfillment rates, and overall warehouse efficiency. Use this data to make adjustments and optimize the system further. Continuous assessment and optimization will help ensure the WMS remains effective and aligned with your evolving business needs over time.
Step 12: Scale and Adapt
As your business grows, ensure your WMS can scale accordingly. Periodically evaluate the system to determine if it can handle increased inventory, more complex workflows, or additional locations. If necessary, consult with your vendor about upgrading features or adding modules to accommodate changing needs. Adapting your WMS to align with your business growth will help maintain operational efficiency and continue delivering value over time, supporting long-term success.
WMS Implementation Best Practices
Implementing a Warehouse Management System (WMS) is a crucial step for businesses looking to enhance operational efficiency, accuracy, and customer satisfaction. However, the success of a WMS implementation largely depends on following best practices that ensure a smooth transition and optimal use of the system.
By adhering to proven strategies, organizations can minimize disruptions, maximize the benefits of their new system, and achieve their warehouse management goals effectively. This guide outlines essential best practices for WMS implementation to help businesses streamline their processes and enhance overall performance.
Conduct a Thorough Needs Assessment
Before implementing a WMS, conduct a detailed needs assessment to identify specific requirements based on current warehouse operations. Engage stakeholders across departments to understand pain points and desired features. This assessment ensures the selected WMS aligns with organizational goals and operational needs, reducing the likelihood of costly adjustments later in the implementation process.
Involve Key Stakeholders
Involving key stakeholders, including warehouse managers, staff, and IT personnel, is essential for successful WMS implementation. Their insights into daily operations can help identify challenges and opportunities that may not be apparent from a management perspective. Engaging these individuals fosters a sense of ownership and collaboration, increasing user acceptance and support for the new system.
Develop a Comprehensive Implementation Plan
A well-structured implementation plan outlines each phase of the WMS deployment, including timelines, resource allocation, and responsibilities. This plan should detail the necessary training, system configuration, and testing procedures. A comprehensive approach ensures that all implementation aspects are addressed, reducing the risk of oversights and enhancing overall project efficiency.
Provide Adequate Training
Effective training is critical for ensuring employees can use the new WMS confidently and efficiently. Develop a training program that accommodates various learning styles using hands-on sessions, online resources, and user manuals. Including real-life scenarios during training helps employees understand the system's impact on their daily tasks, leading to smoother adoption and improved performance.
Test Thoroughly Before Going Live
Conduct extensive testing of the WMS prior to the official launch. This should include functional testing to verify all features operate as intended and user acceptance testing to gather feedback from actual users. Address any identified issues during this phase to ensure a seamless transition and reduce the risk of disruptions when the system goes live.
Monitor Performance Metrics
After implementation, continuously monitor key performance indicators (KPIs) to evaluate the effectiveness of the WMS. Common metrics include order accuracy, inventory turnover, and shipping times. Regular analysis of these metrics allows organizations to identify areas for improvement and make necessary adjustments, ensuring the WMS continues to meet business objectives and enhance operational efficiency.
Foster a Culture of Continuous Improvement
Promoting a culture of continuous improvement encourages employees to provide feedback on the WMS and suggest enhancements. Regularly assess the system's performance against organizational goals and gather user input to identify areas needing optimization. This proactive approach helps organizations adapt their WMS to evolving business needs, ensuring it remains an effective tool for enhancing warehouse operations.
Importance of WMS Implementation
Warehouse Management System (WMS) implementation is a critical aspect of modern supply chain management. As businesses grow and logistics become more complex, the need for efficient inventory and order management becomes paramount. A well-implemented WMS optimizes warehouse operations, enhances visibility, and improves overall productivity.
By automating various processes, it allows companies to respond quickly to market demands, reduce costs, and increase customer satisfaction. Understanding the importance of WMS implementation can help organizations leverage technology to streamline their operations and maintain a competitive edge.
Improved Inventory Accuracy
Implementing a Warehouse Management System (WMS) significantly enhances inventory accuracy by automating tracking and management processes throughout the warehouse. This automation not only reduces the chances of human error but also ensures real-time visibility into stock levels across multiple locations. With accurate and timely inventory data, businesses can effectively prevent stock outs and overstock situations, which leads to better decision-making and optimized inventory management practices that ultimately contribute to operational efficiency.
Enhanced Operational Efficiency
A WMS streamlines warehouse operations by automating essential tasks such as order picking, packing, and shipping. By reducing reliance on manual intervention, a WMS accelerates operational processes and minimizes delays that often arise from human errors. This streamlined approach allows employees to work more productively and efficiently, leading to increased throughput within the warehouse. As a result, businesses can fulfill orders faster and improve service delivery to customers.
Better Order Fulfillment
Implementing a WMS ensures accurate and efficient order processing, leading to higher fulfillment rates. With features like automated picking, batch processing, and real-time inventory updates, businesses can fulfill customer orders quickly and precisely. This enhanced efficiency boosts customer satisfaction and strengthens brand trust, encouraging repeat business and fostering loyalty. Effective order fulfillment is crucial for gaining a competitive advantage in today’s marketplace.
Cost Reduction
WMS implementation can result in significant cost savings by optimizing inventory levels and reducing labor costs in the warehouse. Improved inventory management minimizes excess stock, lowering holding costs and waste. Furthermore, automation decreases labor hours spent on manual tasks, further reducing operational expenses. By cutting unnecessary costs and enhancing efficiency, companies can allocate resources more effectively and reinvest savings into other critical areas of their business.
Enhanced Data Visibility and Reporting
It provides organizations with valuable insights through robust data visibility and comprehensive reporting capabilities. Users can access real-time information regarding inventory levels, order status, and various warehouse performance metrics. This access to accurate data enables informed decision-making, facilitates the identification of areas requiring improvement, and assists in setting strategic goals based on thorough analysis. By leveraging this information, businesses can enhance operational efficiency and support long-term growth initiatives.
Scalability and Flexibility
As businesses grow, their warehouse operations must adapt to evolving demands and market conditions. A well-implemented WMS offers the scalability and flexibility necessary to accommodate such growth seamlessly. The system can easily integrate with other existing software and adapt to new processes. This capability ensures that businesses can expand their operations while maintaining efficiency, allowing them to meet customer expectations and remain competitive in their respective industries over time.
Challenges in WMS Implementation
Implementing a Warehouse Management System (WMS) can significantly enhance operational efficiency and inventory accuracy. However, the process is not without its challenges. Businesses often face obstacles that can hinder the successful implementation and adoption of the new system. Identifying these challenges early on is crucial for developing effective strategies to mitigate them.
By understanding the potential pitfalls—such as resistance to change, inadequate training, and integration issues—organizations can navigate the implementation process more smoothly, ensuring that they fully leverage the benefits of their WMS.
Resistance to Change
One of the most common challenges in WMS implementation is resistance from employees who may be hesitant to adopt new technologies and processes. Change can be intimidating, and employees might feel insecure about their roles. Overcoming this resistance requires effective communication about the benefits of the new system and involving employees in the implementation process to foster a sense of ownership.
Inadequate Training
A successful WMS implementation relies heavily on proper training for all users. Inadequate training can lead to confusion and mistakes, undermining the system's effectiveness. To address this challenge, businesses should develop a comprehensive training program that includes hands-on sessions, online resources, and ongoing support, ensuring that employees feel confident in using the new system.
Data Migration Issues
Transferring existing data into a new WMS can be a complex and error-prone process. Inaccurate or incomplete data migration can lead to discrepancies and operational inefficiencies. To mitigate this challenge, organizations should conduct thorough data audits and cleansing before migration, ensuring that only accurate and relevant information is transferred to the new system.
Integration with Existing Systems
Integrating a new WMS with existing systems, such as ERP or TMS, can pose significant challenges. Compatibility issues may arise, leading to data silos and disrupted workflows. To avoid integration problems, businesses should conduct a thorough analysis of their existing systems and ensure that the new WMS is compatible. Collaboration with vendors for seamless integration is also essential.
Underestimating Time and Costs
Many organizations underestimate the time and costs involved in implementing a WMS. This can lead to budget overruns and project delays. To counter this challenge, businesses should conduct a detailed project scope analysis, including timelines and costs, before commencing implementation. Establishing realistic expectations will help manage resources effectively and keep the project on track.
Lack of Stakeholder Buy-in
Successful WMS implementation requires buy-in from key stakeholders, including management, staff, and IT teams. If stakeholders are not fully engaged or supportive, the project can face significant roadblocks. To overcome this challenge, organizations should involve stakeholders early in the process, addressing their concerns and highlighting the benefits of the WMS for their specific roles and departments.
Factors to Consider When Choosing a WMS
Choosing the right Warehouse Management System (WMS) is crucial for optimizing warehouse operations and improving overall efficiency. With a wide range of options available in the market, businesses must thoroughly evaluate their specific needs and objectives before making a selection.
A well-chosen WMS can streamline processes, enhance inventory accuracy, and ultimately improve customer satisfaction. It’s essential to consider aspects like scalability, ease of integration, cost, and user-friendliness to ensure the chosen system aligns with the company's goals and operational demands. Here are some key factors to consider when selecting a WMS for your business:
- Scalability: Ensure the WMS can grow with your business. It should accommodate increased inventory levels and additional warehouse locations.
- Integration Capabilities: Choose a WMS that easily integrates with your existing systems, such as ERP or TMS. This will facilitate seamless data flow and improve operational efficiency.
- User-Friendliness: The interface should be intuitive and easy to navigate, enabling employees to learn the system quickly. A user-friendly design minimizes training time and encourages adoption.
- Customization Options: Look for a WMS that offers customization features to tailor the system to your specific workflows. This flexibility can enhance efficiency and address unique operational needs.
- Cost-Effectiveness: Consider the total cost of ownership, including licensing fees, implementation costs, and ongoing maintenance. Ensure the WMS aligns with your budget.
- Vendor Support and Training: Evaluate the level of support and training provided by the vendor. Strong customer support can significantly ease the implementation process.
- Reporting and Analytics: Choose a WMS that offers robust reporting and analytics capabilities. These features allow you to monitor performance metrics and make data-driven decisions.
- Industry-Specific Features: If your business operates in a specific industry, look for a WMS that offers tailored features addressing your sector's unique challenges.
Conclusion
Implementing a Warehouse Management System (WMS) can revolutionize warehouse operations by boosting accuracy, streamlining processes, and enhancing customer satisfaction. To ensure a successful transition, businesses should follow best practices like conducting detailed assessments, engaging key stakeholders, and offering thorough training to employees.
Continuous monitoring of performance metrics and fostering a culture of continuous improvement will enable organizations to maximize long-term benefits from their WMS. A well-executed WMS implementation not only increases operational efficiency but also drives sustainable growth in a competitive market. Fynd WMS offers an intuitive platform that helps businesses unlock these benefits seamlessly.
Frequently asked questions
A WMS is software designed to manage and optimize warehouse operations, including inventory tracking, order fulfillment, and shipping. It helps streamline processes, reduce errors, and improve overall efficiency.
Implementing a WMS is crucial for enhancing operational efficiency, reducing inventory costs, and improving customer satisfaction. It enables better visibility into inventory and workflow, facilitating informed decision-making.
The implementation timeline for a WMS can vary widely based on factors like warehouse size, complexity, and customization needs. Generally, it can take anywhere from a few weeks to several months.
Key benefits of a WMS include improved inventory accuracy, faster order processing, enhanced labor productivity, better customer service, and reduced operational costs.
To ensure success, conduct a thorough needs assessment, involve key stakeholders, provide adequate training, and monitor performance metrics after implementation. Following best practices is crucial for achieving desired outcomes.
Yes, many WMS solutions can integrate seamlessly with other systems, such as Enterprise Resource Planning (ERP) and Transportation Management Systems (TMS). This integration enhances data flow and improves overall operational efficiency.