Solutions for every business need
Growth comes in all shapes and sizes. Whether it’s smoother operations, sharper insights, higher revenue—or all of the above—we’ve got you covered
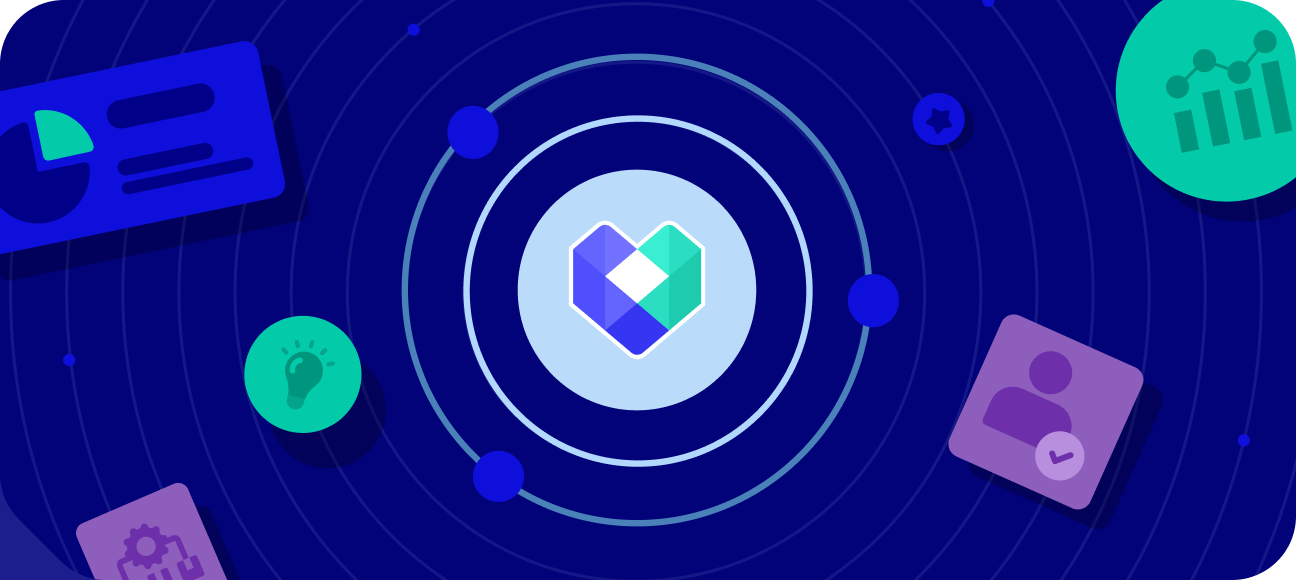
Warehouse management made simple
Gain full control over your inventory with smart automation, real-time tracking, and efficient workflows—ensuring your stock moves smoothly, every time
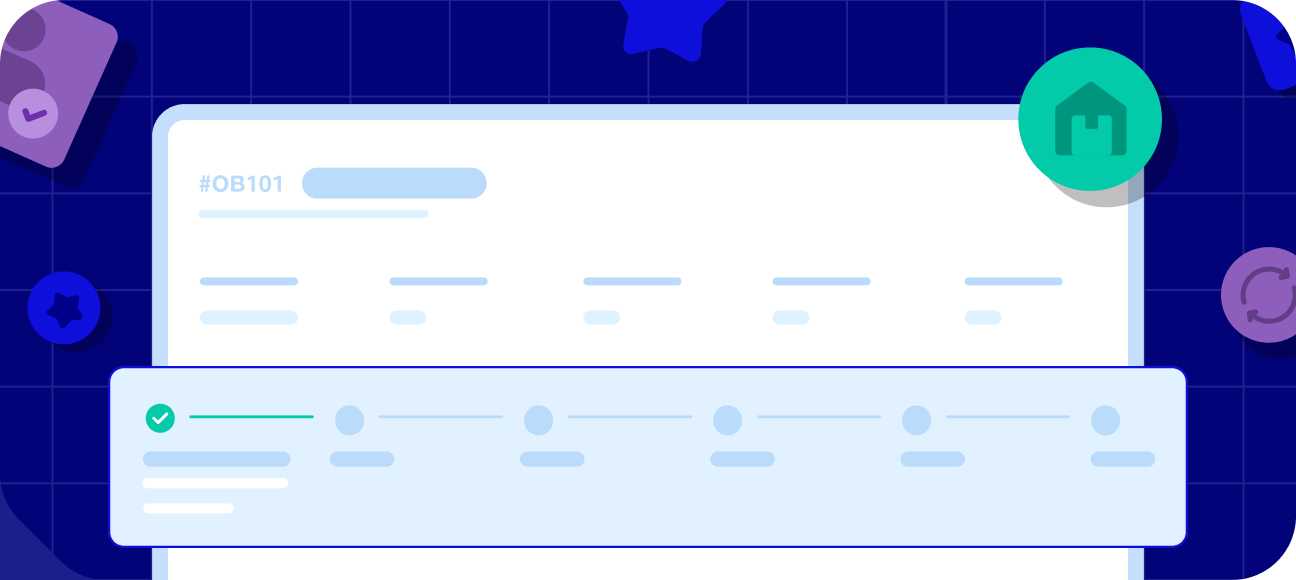
Launch hyperlocal commerce instantly
Set up and scale your hyper-local e-commerce with easy tools for web, orders, and delivery management—bringing you closer to customers, faster
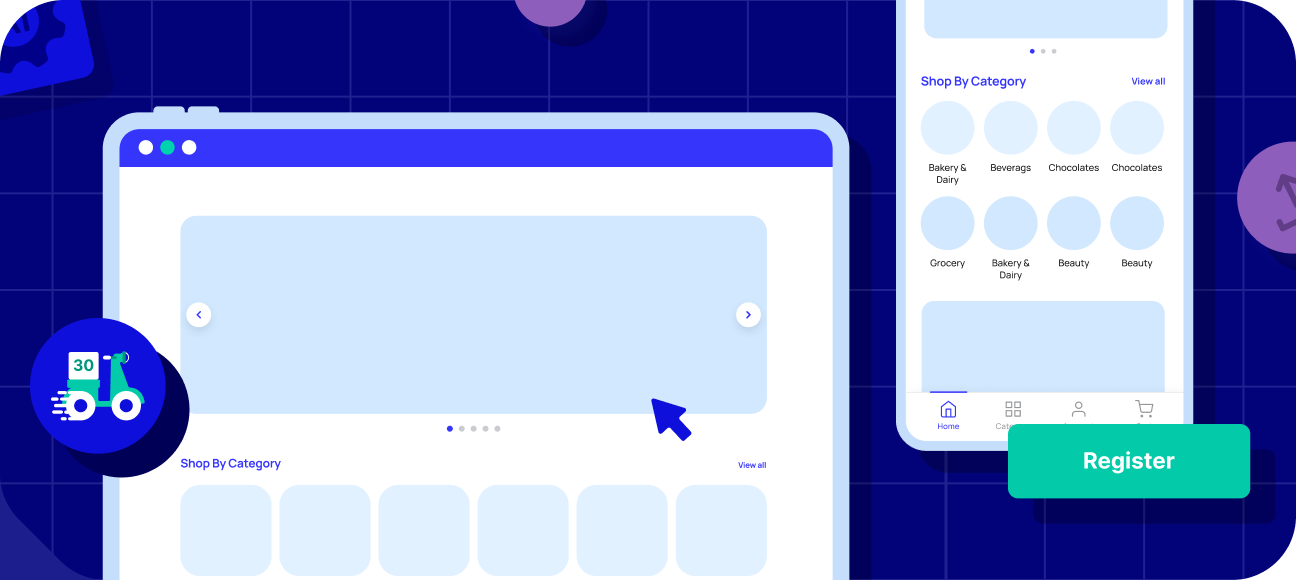
Delivery management made easy
Gain control over your deliveries with real-time visibility, smart automation, and seamless coordination—ensuring on-time arrivals, every time
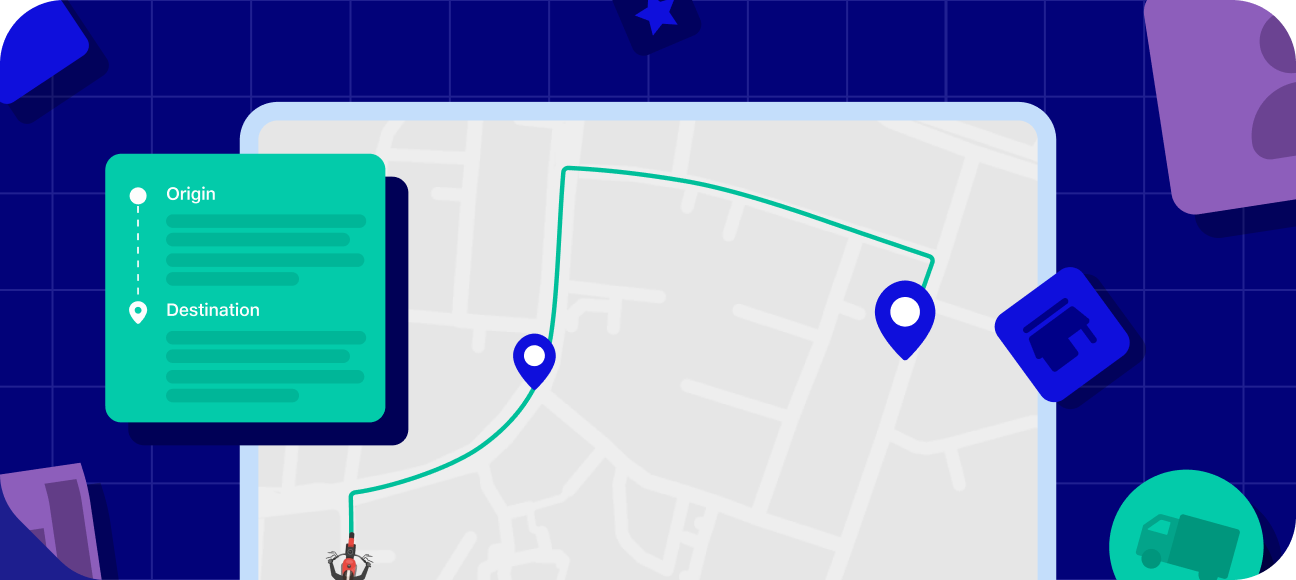
Order management made easy
Master every order with full visibility, smart automation, and effortless control—delivering the right outcomes, every time
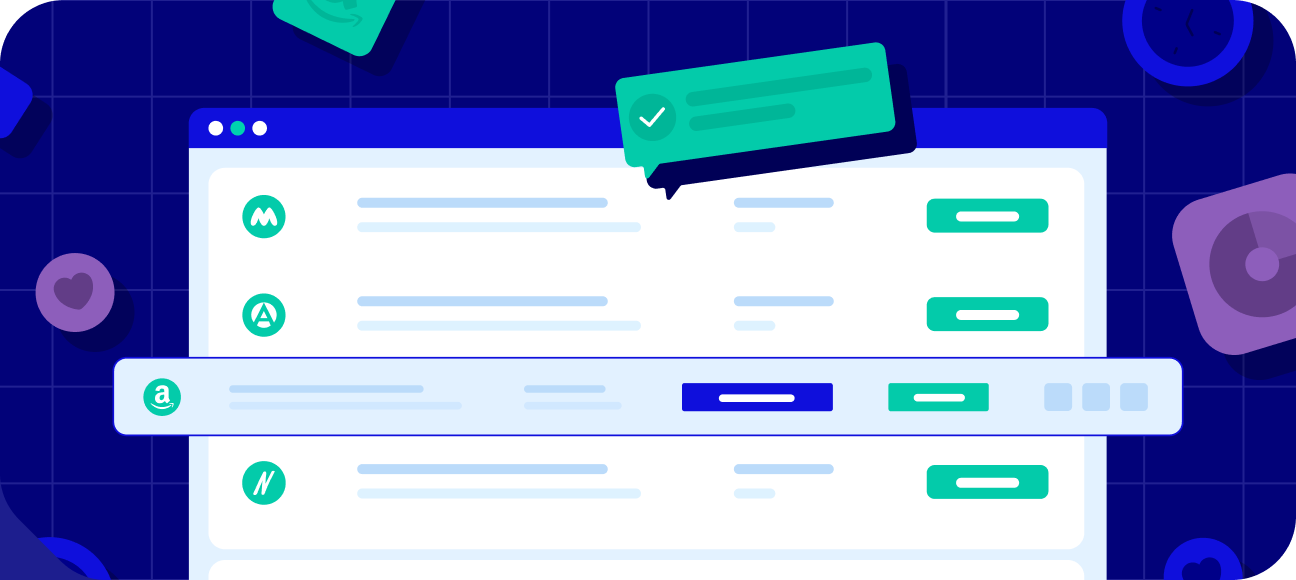
Speak to an expert
Explore how Fynd Commerce can improve every aspect of your business, from online to instore and beyond
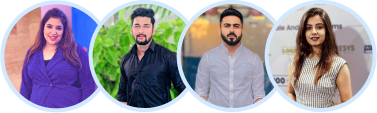
Speak to an expert
Explore how Fynd WMS powers operational excellence with our solution experts
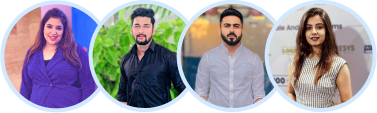
Speak to an expert
Explore how Fynd Quick powers hyperlocal businesses with our solution experts
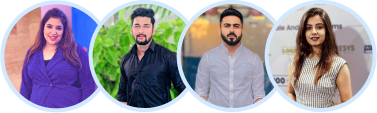
Speak to an expert
Explore how Fynd TMS powers better deliveries with our solution experts
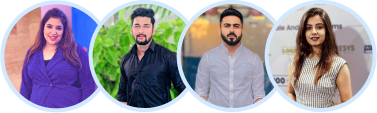
Speak to an expert
Explore how Fynd OMS powers seamless order management with our solution experts
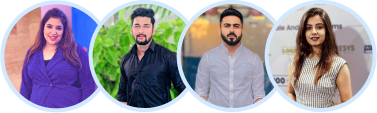
Featured Blog
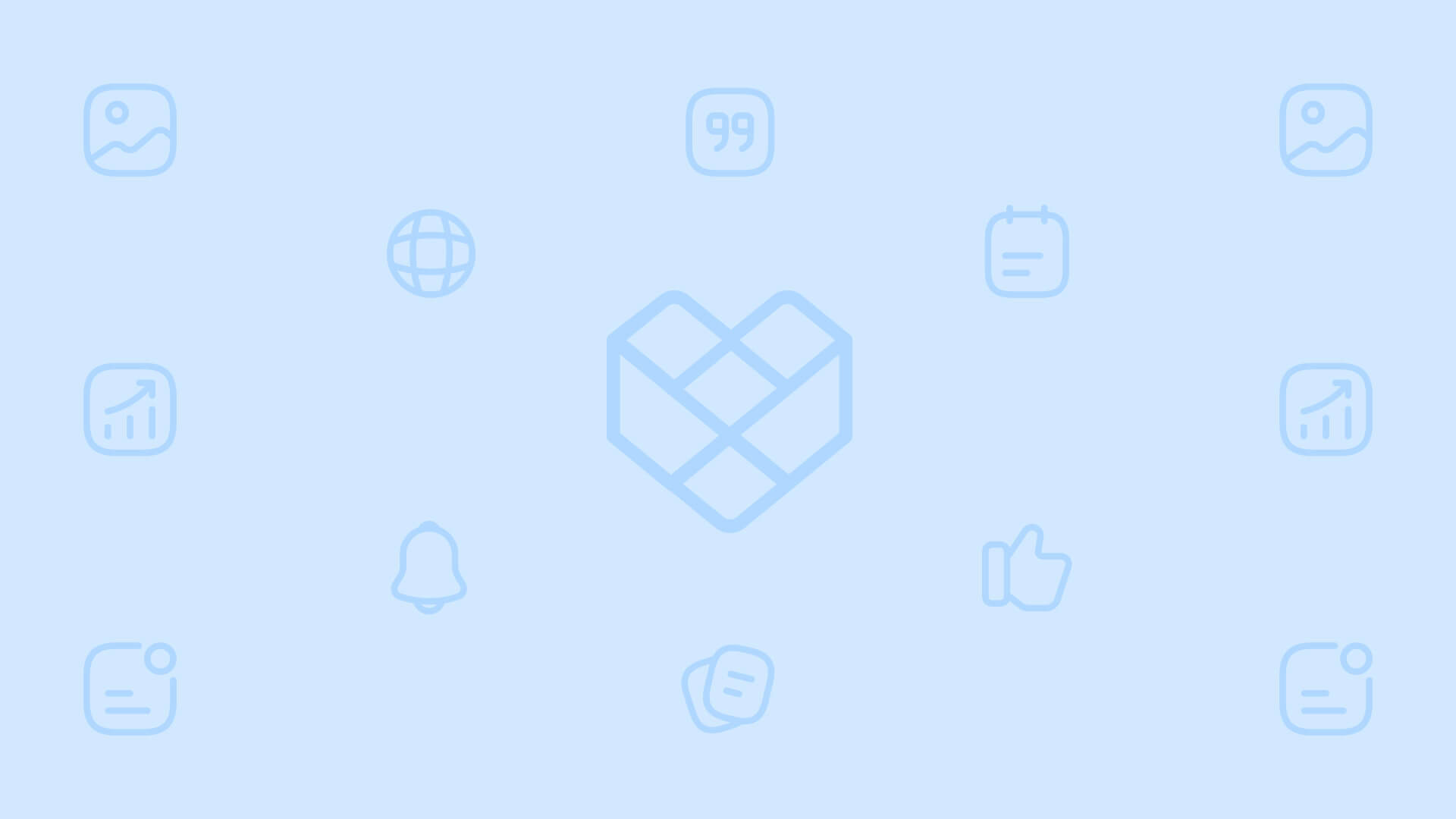
Empower your business, every step of the way
Simplify operations, scale smarter, and deliver better experiences with solutions designed to grow with your business
Take your warehouse management to the next level
Experience hassle-free inventory management with Fynd WMS, designed to keep your operations efficient and accurate. Book a demo to see how Fynd WMS can boost productivity and profits for your business!
Kickstart your quick delivery website
Experience seamless hyper-local commerce with Fynd Quick—engineered to keep things running smoothly and help you reach customers in record time. Book a demo and see how Fynd Quick can drive efficiency and growth for your business!
Level up your delivery management
See how you can manage deliveries with Fynd TMS, designed to streamline operations and keep your customers delighted. Book a demo with our team and find out how Fynd TMS can boost your efficiency and bottom line!
Take your order management to the next level
Discover how effortless order management can be with Fynd OMS, built to keep things running smoothly and make your customers happy. Book a demo with our team and see how Fynd OMS can help boost your efficiency and profits!
Implementing a Warehouse Management System (WMS) provides numerous benefits that can significantly enhance the efficiency and effectiveness of warehouse operations. A WMS automates various processes, from inventory tracking to order fulfillment, allowing businesses to streamline workflows and reduce manual errors. With real-time visibility into stock levels, companies can make informed decisions regarding inventory management, ensuring optimal stock levels while minimizing costs associated with overstocking or stockouts.
Additionally, a WMS improves labor management by optimizing employee tasks and workflows, increasing productivity and job satisfaction. One of the primary benefits of a WMS is enhanced inventory accuracy. By automating inventory management processes, businesses can track stock levels in real-time, reducing the likelihood of errors in order fulfillment. This accuracy not only ensures that customers receive the correct products on time but also helps avoid the costs associated with incorrect shipments.
Furthermore, accurate inventory data allows for better forecasting and demand planning, enabling businesses to respond effectively to market changes. Increased operational efficiency is another significant advantage of implementing a WMS. By automating routine tasks such as picking, packing, and shipping, warehouses can operate more smoothly and quickly.
What is a Warehouse Management System?
A Warehouse Management System (WMS) is a software solution that streamlines and optimizes warehouse operations. It manages the flow of goods from the moment they enter a warehouse until they are shipped out, ensuring efficient handling and storage of inventory. Key functions include inventory tracking, receiving, put-away, order picking, packing, and shipping. These functionalities help maintain accurate inventory levels, optimize storage space, and facilitate timely order fulfillment.
Implementing a WMS enhances operational efficiency, reduces errors, and improves customer satisfaction by ensuring accurate and timely deliveries. Additionally, it provides real-time visibility into inventory levels, enabling better decision-making and resource management.
Benefits of a Warehouse Management System
Implementing a Warehouse Management System (WMS) can significantly enhance a company's operational efficiency and accuracy. As businesses face increasing demands for rapid order fulfillment and precise inventory management, a WMS offers the tools necessary to streamline warehouse processes. By automating tasks and providing real-time visibility into inventory levels, organizations can improve productivity and reduce costs.
A WMS not only optimizes internal operations but also enhances customer satisfaction through timely deliveries and accurate order processing. This software solution is essential for maintaining a competitive edge in today's fast-paced logistics environment, ensuring that businesses can adapt to changing market conditions effectively.
1. Enhanced Inventory Accuracy
Enhanced inventory accuracy is a key benefit of a Warehouse Management System (WMS), as it provides real-time tracking and visibility of stock levels. By automating inventory management processes, a WMS minimizes discrepancies between recorded and actual inventory, reducing the risk of stockouts or overstocking. Accurate inventory data enables better decision-making regarding restocking and order fulfillment, ultimately leading to improved operational efficiency and increased customer satisfaction.
2. Improved Operational Efficiency
Improved operational efficiency is a significant advantage of implementing a Warehouse Management System (WMS). A WMS streamlines workflows and reduces manual labor by automating various warehouse processes, such as receiving, picking, packing, and shipping. This automation minimizes errors and speeds up order processing times, allowing businesses to handle higher volumes of orders with greater accuracy.
3. Optimized Space Utilization
A Warehouse Management System (WMS) enhances space utilization by employing strategies like slotting optimization and dynamic slotting. These features ensure that high-demand items are stored in easily accessible locations while slower-moving items occupy less prime areas. This efficient organization maximizes storage capacity and minimizes the need for additional warehouse space, ultimately leading to cost savings and improved operational efficiency.
4. Increased Labor Productivity
By automating various warehouse processes, a WMS significantly boosts labor productivity. It reduces the time spent on manual tasks such as inventory counting and order picking, allowing employees to focus on more value-added activities. This automation leads to faster order fulfillment and a more efficient workforce, ultimately enhancing overall warehouse performance and reducing labor costs.
3. Accurate Order Fulfillment
A Warehouse Management System (WMS) enhances order accuracy by automating the picking and packing processes. It provides real-time data on inventory levels and locations, ensuring that the correct items are selected for each order. This reduces the likelihood of errors, leading to higher customer satisfaction and trust in the business. Accurate order fulfillment is crucial for maintaining strong customer relationships and repeat business.
4. Real-Time Data Insights
WMS offers real-time visibility into inventory levels, order statuses, and warehouse operations. This immediate access to data allows managers to make informed decisions quickly, optimizing workflows and resource allocation. With real-time insights, businesses can respond proactively to changes in demand or operational challenges, ultimately enhancing overall efficiency and effectiveness in warehouse management.
5. Reduced Operational Costs
Implementing a WMS can lead to significant cost savings by minimizing manual labor, reducing errors, and optimizing inventory levels. By streamlining processes and improving accuracy, businesses can lower their operational expenses related to labor, storage, and inventory management. This reduction in costs contributes to improved profitability and enables organizations to invest in further growth initiatives.
6. Enhanced Customer Service
A WMS improves customer service by ensuring timely deliveries and accurate order processing. With better inventory visibility and streamlined workflows, businesses can fulfill orders more efficiently and respond quickly to customer inquiries. Enhanced customer service leads to increased satisfaction, loyalty, and positive word-of-mouth, which are essential for long-term business success.
7. Effective Labor Management
A Warehouse Management System (WMS) enhances labor management by providing real-time data on employee performance and productivity. This allows managers to allocate resources efficiently, ensuring that the right number of staff is available during peak times. By tracking individual performance metrics, a WMS helps identify training needs and rewards high-performing employees, ultimately leading to a more motivated and efficient workforce.
8. Streamlined Returns Management
A WMS simplifies the returns process by efficiently managing returned items and updating inventory levels accordingly. It provides clear visibility into return statuses and facilitates quick processing, which minimizes delays in restocking. This streamlined approach not only improves customer satisfaction by handling returns swiftly but also optimizes inventory control, ensuring that returned products are accounted for and ready for resale when possible.
9. Improved Compliance and Traceability
With a WMS, businesses can enhance compliance with industry regulations through detailed tracking of inventory movements and documentation. This capability is crucial for audits and recalls, as it allows for quick identification of affected products. By maintaining accurate records of all transactions and inventory changes, a WMS ensures that companies adhere to regulatory standards while improving overall operational transparency.
10. Advanced Reporting Capabilities
A WMS offers robust reporting tools that provide insights into various warehouse operations, such as inventory turnover rates, order fulfillment times, and labor productivity. These analytics enable managers to identify trends, assess performance against key performance indicators (KPIs), and make data-driven decisions for continuous improvement. Enhanced reporting capabilities contribute to strategic planning and operational efficiency across the organization.
11. Scalability for Growth
A Warehouse Management System (WMS) offers significant scalability, allowing businesses to adapt to changing demands easily. As a company grows, a WMS can accommodate increased inventory levels and additional warehouse locations without requiring substantial infrastructure investments. This flexibility enables organizations to expand their operations seamlessly, ensuring they can meet market demands without disruption.
12. Enhanced Security Measures
Modern WMS solutions incorporate advanced security features such as encryption, multi-factor authentication, and secure access protocols. These measures protect sensitive inventory and customer data from unauthorized access or breaches. Enhanced security not only safeguards business information but also builds customer trust, which is essential for maintaining a strong reputation in the market.
13. Continuous Monitoring and Updates
Cloud-based WMS solutions offer continuous monitoring and regular updates, ensuring that the system remains secure and up-to-date with the latest features. This proactive approach minimizes downtime and potential vulnerabilities, allowing businesses to focus on core operations without worrying about software maintenance. Regular updates also ensure that users benefit from the latest technological advancements.
14. Seamless Integration with Other Systems
A WMS can easily integrate with various business systems such as ERP, CRM, and e-commerce platforms. This seamless integration eliminates data silos and enhances operational efficiency by ensuring that all systems work together cohesively. Improved data visibility across platforms enables better decision-making and more effective management of supply chain processes.
15. Better Supplier Relationships
A Warehouse Management System (WMS) fosters better relationships with suppliers by ensuring timely and accurate inventory replenishment. With improved visibility into stock levels and automated ordering processes, businesses can maintain optimal inventory levels, reducing the risk of stockouts. This reliability strengthens partnerships with suppliers, as they can trust that orders will be placed consistently and accurately, leading to more favorable terms and collaboration.
16. Enhanced Visibility Across the Supply Chain
A WMS provides comprehensive visibility into the entire supply chain, from inbound shipments to outbound deliveries. This transparency allows businesses to monitor inventory movements in real time, facilitating better coordination with suppliers and customers. Enhanced visibility helps identify potential bottlenecks or delays, enabling proactive measures to maintain smooth operations and improve overall supply chain efficiency.
17. Streamlined Data Flow
Integrating a WMS with other business systems ensures a seamless flow of data across platforms, reducing the need for manual data entry and minimizing errors. This streamlined data flow enhances operational efficiency by providing accurate information for decision-making. Businesses can quickly access critical data related to inventory levels, order statuses, and shipping details, leading to more informed strategic planning.
18. Automation of Routine Tasks
A WMS automates routine warehouse tasks such as inventory counting, order picking, and shipping notifications. This automation reduces the reliance on manual labor, minimizes human error, and speeds up operations. By freeing employees from repetitive tasks, a WMS allows them to focus on more complex activities that require critical thinking and problem-solving skills, ultimately enhancing overall productivity.
What Does a WMS System Do?
Implementing a Warehouse Management System (WMS) is essential for modern warehouses, as it streamlines and optimizes various operations. A WMS manages the entire lifecycle of inventory, from receiving goods to shipping them out. This system automates processes, enhances accuracy, and provides real-time visibility into stock levels.
By integrating with other systems like ERP, a WMS ensures efficient order fulfillment and improved customer satisfaction. Ultimately, a WMS is crucial for businesses aiming to enhance operational efficiency and maintain a competitive edge in the logistics landscape.
1. Inventory Management
A WMS provides real-time visibility into inventory levels and locations within the warehouse. It automates tracking using technologies like barcoding and RFID, which minimize errors and ensure accurate stock counts. This capability allows businesses to optimize inventory turnover, reduce carrying costs, and prevent stockouts or overstock situations. A WMS enables better decision-making regarding inventory replenishment and management by facilitating cycle counting and demand forecasting.
2. Order Fulfillment
The order fulfillment process is significantly enhanced by a WMS, which automates picking, packing, and shipping tasks. The system directs warehouse staff to the most efficient picking routes, ensuring that orders are processed quickly and accurately. By optimizing workflows and reducing manual labor, a WMS helps improve order accuracy and speed, leading to higher customer satisfaction.
3. Receiving and Put-Away
A WMS streamlines the receiving process by automating the validation of incoming goods against purchase orders. This ensures that items are accurately accounted for upon arrival. The system also facilitates efficient put-away processes by directing staff on where to store products based on predefined rules. This organization reduces handling time and optimizes warehouse space utilization, ensuring that items are easily accessible when needed.
4. Labor Management
Labor management is another critical function of a WMS. The system allows managers to assign tasks based on employee skills and proximity to inventory locations. By monitoring performance metrics through key performance indicators (KPIs), managers can identify areas for improvement and optimize workforce productivity. This not only enhances operational efficiency but also contributes to employee satisfaction by ensuring that tasks are allocated fairly and effectively.
5. Reporting and Analytics
A WMS offers robust reporting and analytics capabilities that provide insights into warehouse operations. Businesses can generate reports on inventory levels, order fulfillment rates, labor productivity, and more. These analytics enable data-driven decision-making, helping managers identify trends and areas for improvement. By leveraging this information, companies can optimize their operations further, reduce costs, and enhance overall efficiency in their warehouse management practices.
Conclusion
mplementing a Warehouse Management System (WMS) offers many benefits that can improve warehouse operations, boost efficiency, and increase customer satisfaction. By automating tasks and providing real-time inventory tracking, businesses can streamline their supply chains and lower operating costs. A WMS helps reduce manual errors, speeds up order fulfillment, and ensures accurate stock management. To take advantage of these benefits, it's important to evaluate and choose a WMS that fits your specific business needs.
Frequently asked questions
A Warehouse Management System (WMS) is a software tool designed to manage, automate, and optimize key warehouse processes, including inventory control, order fulfillment, and labor management, enhancing efficiency and accuracy in supply chain operations.
A WMS improves inventory accuracy by automating tracking, updating stock levels in real-time, and minimizing manual errors. It ensures precise record-keeping, reducing discrepancies and preventing overstock or stockouts through better visibility and control.
The main benefits of using a WMS include improved operational efficiency, enhanced inventory accuracy, reduced labor costs, faster order fulfillment, better space utilization, and real-time data access, all leading to increased customer satisfaction.
Yes, a WMS can reduce operational costs by automating processes, minimizing errors, optimizing inventory levels, and improving labor management. These efficiencies lead to lower overhead costs and better resource allocation within warehouse operations.
Yes, training is essential for employees when implementing a WMS to ensure they can effectively use the system, understand its features, and maximize its benefits. Proper training leads to smoother operations and fewer errors.
To choose the right WMS, assess your business needs, warehouse size, and processes. Consider features like scalability, integration capabilities, cost, and user-friendliness. Additionally, research vendor support and industry-specific functionality to ensure the best fit.