Solutions for every business need
Growth comes in all shapes and sizes. Whether it’s smoother operations, sharper insights, higher revenue—or all of the above—we’ve got you covered
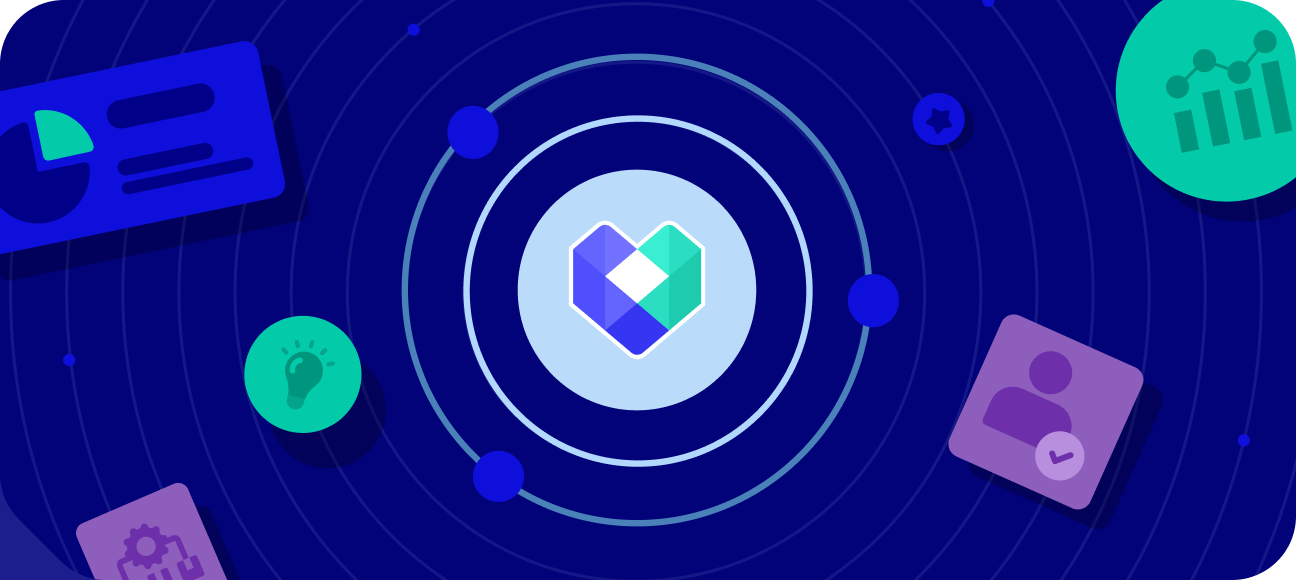
Warehouse management made simple
Gain full control over your inventory with smart automation, real-time tracking, and efficient workflows—ensuring your stock moves smoothly, every time
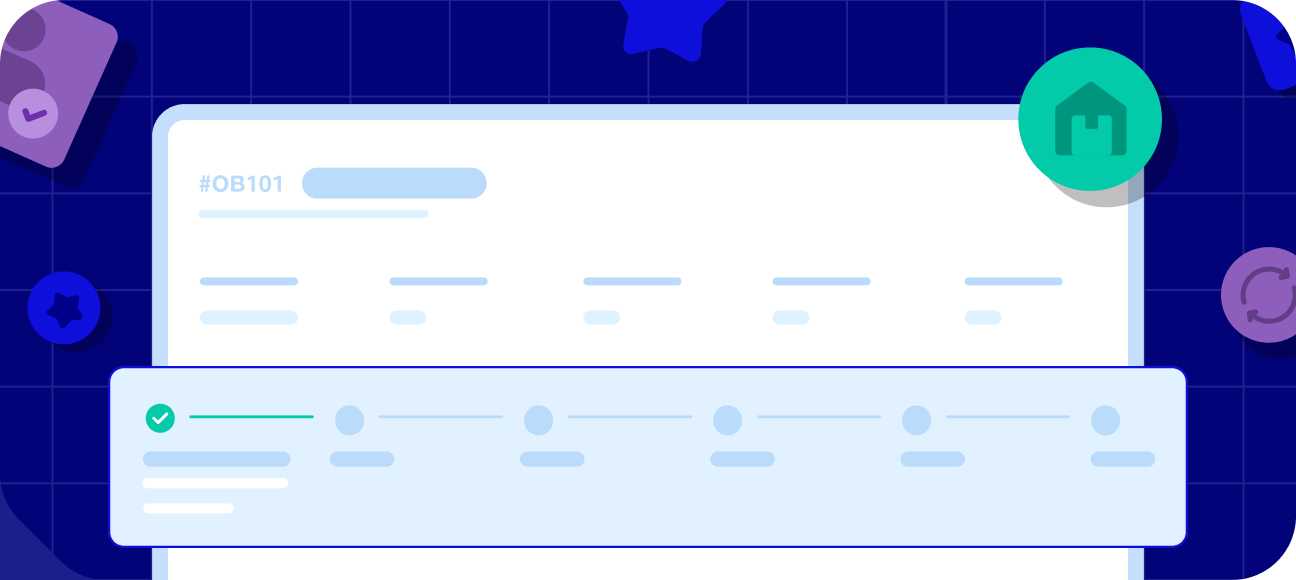
Launch hyperlocal commerce instantly
Set up and scale your hyper-local e-commerce with easy tools for web, orders, and delivery management—bringing you closer to customers, faster
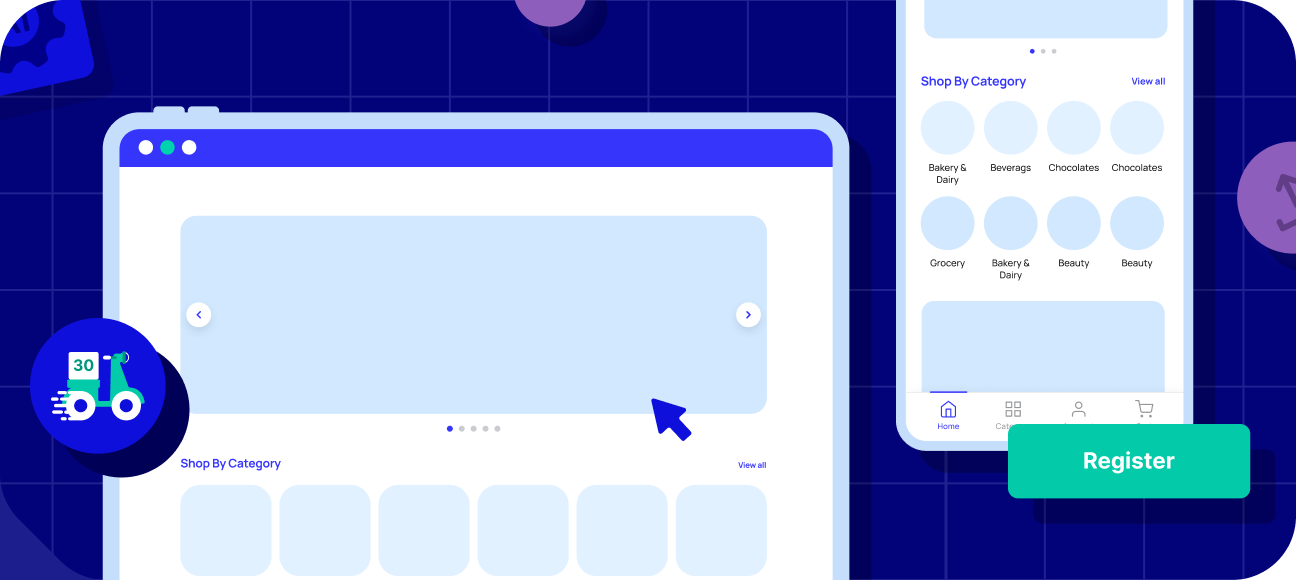
Delivery management made easy
Gain control over your deliveries with real-time visibility, smart automation, and seamless coordination—ensuring on-time arrivals, every time
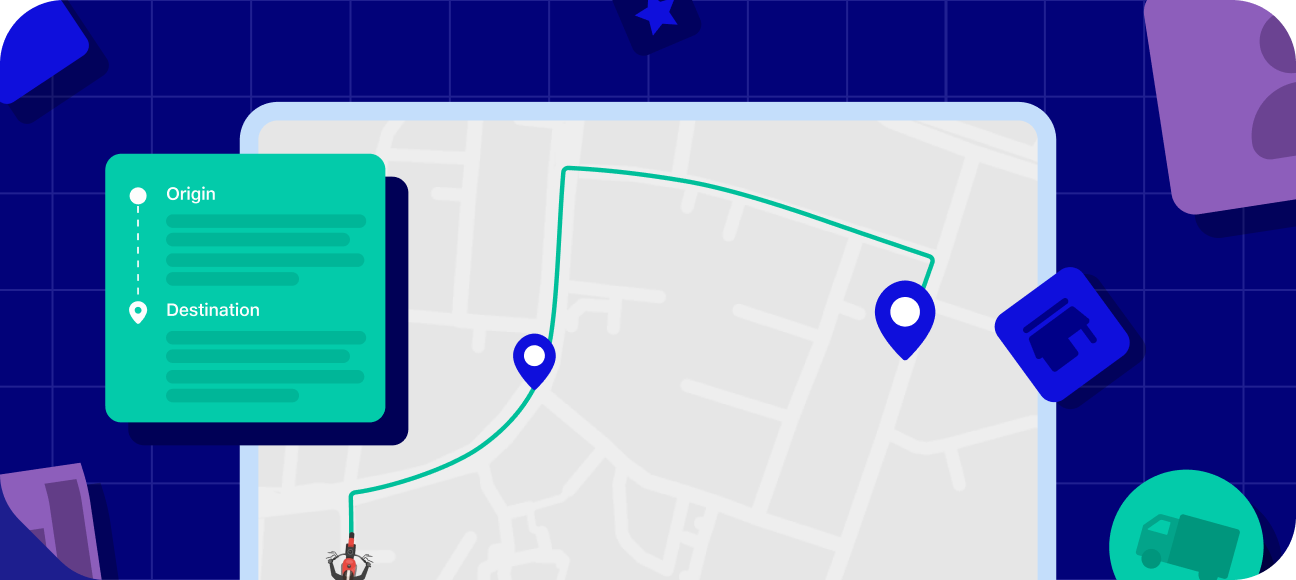
Order management made easy
Master every order with full visibility, smart automation, and effortless control—delivering the right outcomes, every time
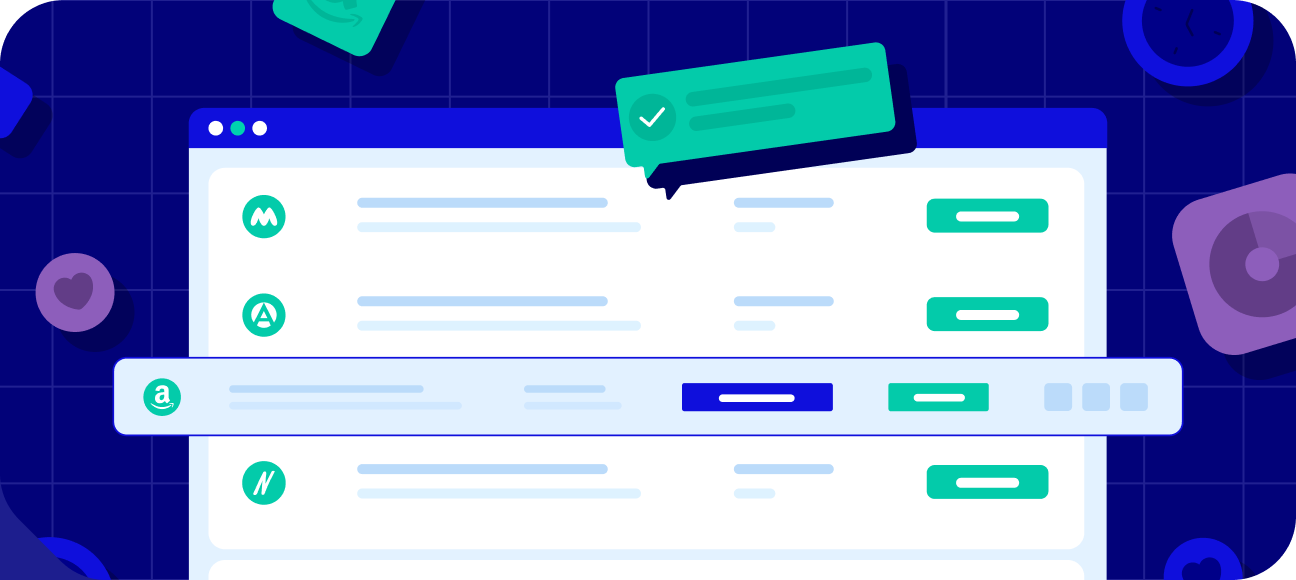
Speak to an expert
Explore how Fynd Commerce can improve every aspect of your business, from online to instore and beyond
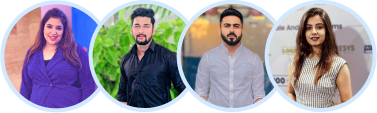
Speak to an expert
Explore how Fynd WMS powers operational excellence with our solution experts
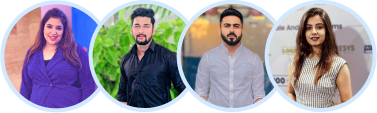
Speak to an expert
Explore how Fynd Quick powers hyperlocal businesses with our solution experts
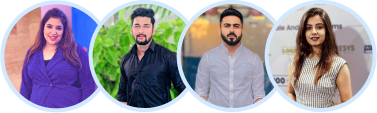
Speak to an expert
Explore how Fynd TMS powers better deliveries with our solution experts
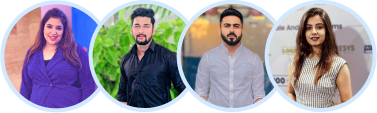
Speak to an expert
Explore how Fynd OMS powers seamless order management with our solution experts
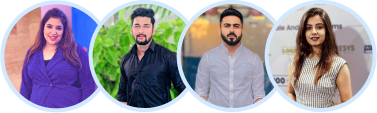
Featured Blog
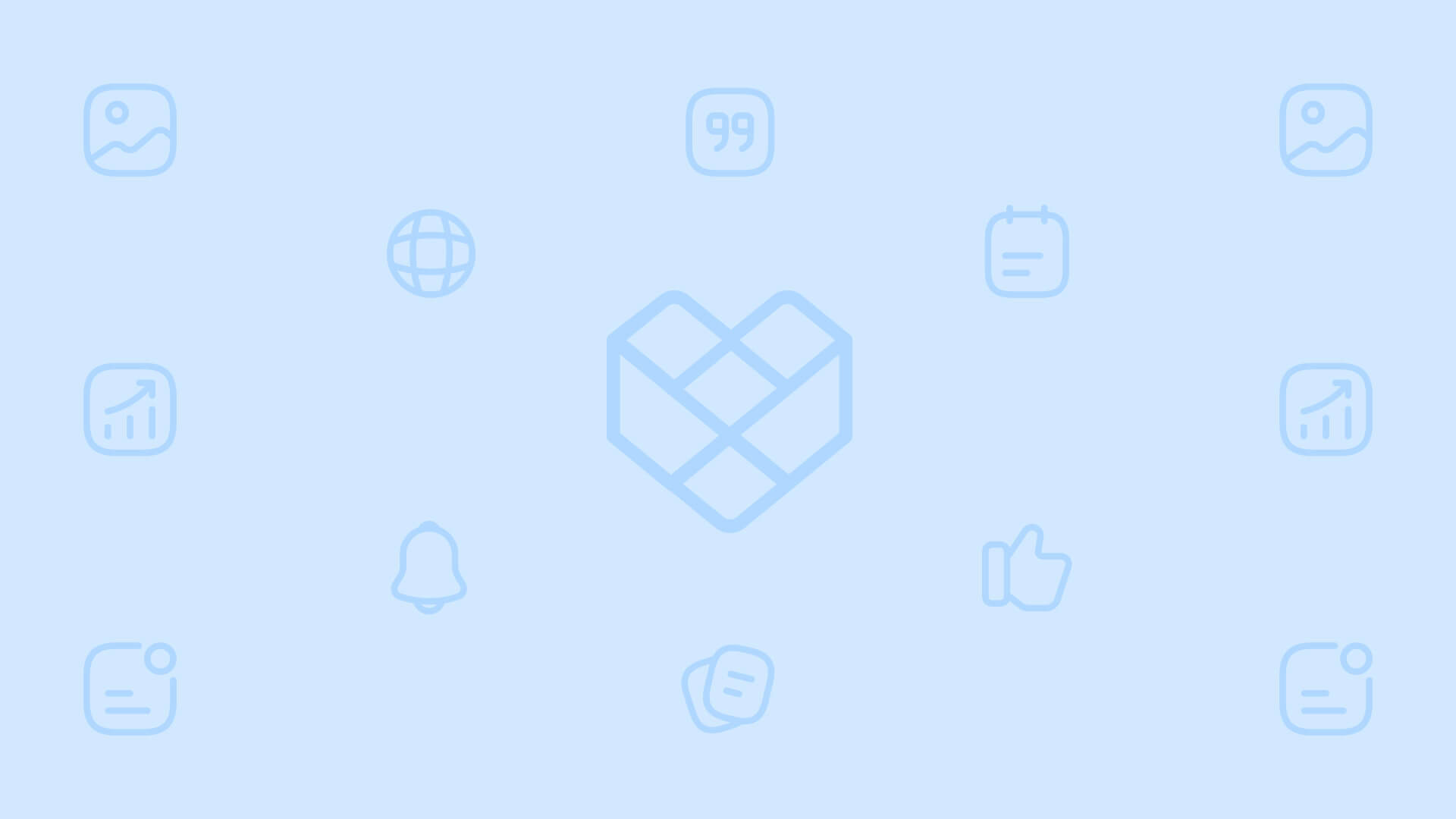
Empower your business, every step of the way
Simplify operations, scale smarter, and deliver better experiences with solutions designed to grow with your business
Take your warehouse management to the next level
Experience hassle-free inventory management with Fynd WMS, designed to keep your operations efficient and accurate. Book a demo to see how Fynd WMS can boost productivity and profits for your business!
Kickstart your quick delivery website
Experience seamless hyper-local commerce with Fynd Quick—engineered to keep things running smoothly and help you reach customers in record time. Book a demo and see how Fynd Quick can drive efficiency and growth for your business!
Level up your delivery management
See how you can manage deliveries with Fynd TMS, designed to streamline operations and keep your customers delighted. Book a demo with our team and find out how Fynd TMS can boost your efficiency and bottom line!
Take your order management to the next level
Discover how effortless order management can be with Fynd OMS, built to keep things running smoothly and make your customers happy. Book a demo with our team and see how Fynd OMS can help boost your efficiency and profits!
A Warehouse Management System (WMS) is a software platform that helps businesses manage their warehouse operations efficiently. It optimizes the entire process, from receiving and storing inventory to order fulfillment and shipping. By providing real-time visibility into inventory levels and warehouse activities, a WMS allows companies to streamline processes, improve accuracy, and reduce errors. This results in faster order processing, lower labor costs, and increased customer satisfaction.
One of the core functions of a WMS is inventory management. The system tracks every item as it enters, moves within, and exits the warehouse, ensuring accurate stock levels and reducing the risk of overstocking or stockouts. WMS also aids in space optimization by directing warehouse staff on where to store items for maximum efficiency.
In addition to inventory control, a WMS supports order picking, packing, and shipping. Advanced systems offer features like barcode scanning, RFID tracking, and integration with transportation management systems (TMS) to automate key processes. The result is a smoother workflow, faster delivery times, and greater operational efficiency. A WMS is essential for businesses looking to improve warehouse performance, lower operational costs, and enhance customer service through better inventory and workflow management.
Is WMS Useful for Your Business
A Warehouse Management System (WMS) is a helpful tool for businesses that manage a lot of inventory. It helps track products in real time, showing exactly what is in stock and where it is located in the warehouse. This makes it easier to find and ship products quickly, reducing mistakes.
By using a WMS, companies can also save space by organizing items better, which leads to smoother operations. In addition, a WMS can automate many tasks that are usually done by hand, such as counting stock and updating records. This reduces human errors and saves time. It also helps businesses keep up with customer demands and grow without losing efficiency.
Warehouse Management Statistics
Warehouse management statistics highlight the growing importance of efficiency in supply chain operations. Global warehouse automation is expected to reach $30 billion by 2026, driven by the need for faster order fulfillment and reduced operational costs. Studies show that companies using Warehouse Management Systems (WMS) see a 25% increase in labor productivity and a 20% reduction in inventory inaccuracies.
Additionally, warehouses with automated systems report 30-40% faster order processing times. E-commerce growth and consumer demand for quick delivery are pushing businesses to invest in smarter warehouse solutions, making WMS and automation critical for modern supply chains.
Benefits of Implementing a WMS
Implementing a Warehouse Management System (WMS) offers significant benefits, improving efficiency, accuracy, and cost-effectiveness in warehouse operations. A WMS automates key tasks such as inventory tracking, order picking, and shipping, reducing manual errors and speeding up workflows. It enhances inventory accuracy by providing real-time data on stock levels, preventing stockouts and overstocking.
Additionally, a WMS optimizes warehouse space utilization and streamlines labor management, leading to lower operational costs. With better control over inventory and faster order processing, businesses can improve customer satisfaction and respond quickly to market demands, making WMS essential for competitive supply chain operations.
1. Increased Efficiency
A WMS automates critical warehouse tasks like inventory tracking, order picking, and shipping, significantly reducing manual efforts. By streamlining workflows, it accelerates the overall process, allowing for faster order processing and fulfillment. This boosts productivity and ensures that operations run smoothly, helping businesses meet demand more efficiently and reducing delays in the supply chain.
2. Improved Accuracy
With features such as barcode scanning, RFID technology, and real-time data access, a WMS greatly enhances inventory accuracy. It helps track stock movement precisely, minimizing errors like misspeaks or incorrect shipments. This level of accuracy ensures that stock levels are always updated, preventing costly issues such as stockouts, overstocking, and returns due to faulty orders.
3. Optimized Space Utilization
A WMS helps optimize the layout and storage within a warehouse by guiding where to store products based on available space and picking patterns. This ensures maximum space usage, reducing wasted areas and improving the flow of goods. Efficient space utilization also leads to faster movement of items, enhancing overall warehouse performance and reducing operational bottlenecks.
4. Reduced Labour Costs
By automating routine tasks and streamlining workflows, a WMS reduces the need for excessive manual labor. This decreases the number of employees required for day-to-day operations, lowering labor costs. The system allows staff to focus on more critical tasks, improving workforce productivity while reducing errors caused by manual handling, ultimately saving time and money.
5. Enhanced Customer Satisfaction
With faster order processing, improved accuracy, and better inventory management, a WMS ensures that customer orders are fulfilled on time and without mistakes. This leads to fewer returns, quicker deliveries, and higher customer satisfaction rates. The system’s ability to scale with demand also ensures businesses can meet customer expectations during peak periods or unexpected surges in orders.
Arranging Your Warehouse
Arranging your warehouse efficiently is crucial for optimizing space, improving workflows, and reducing errors. A well-organized warehouse ensures faster order fulfillment, better inventory management, and enhanced productivity.
By strategically placing high-demand products, utilizing clear labeling systems, and maintaining proper aisle spacing, you can streamline operations. Effective warehouse arrangement not only saves time but also reduces labor costs and prevents bottlenecks in daily operations. Prioritize safety and accessibility to ensure smoother movement and increased overall efficiency in your warehouse processes.
- Group Similar Items: Store related products together to streamline picking processes and reduce the time spent searching for items.
- Use Vertical Space: Maximize storage capacity by utilizing vertical racking systems, making the most of the available warehouse space.
- Label Clearly: Implement clear labeling systems for shelves and bins to improve inventory tracking and reduce picking errors.
- Design Wide Aisles: Ensure aisles are wide enough for forklifts or other equipment to move freely, preventing accidents and delays.
- Place High-Demand Items Nearby: Position frequently picked products closer to packing stations for quicker access and faster order fulfillment.
- Implement Safe Storage: Store heavy and bulky items on lower shelves to minimize the risk of accidents and improve accessibility.
- Maintain Regular Reviews: Periodically assess your warehouse layout to optimize storage and adjust to evolving inventory needs or demand changes.
Receiving and Managing New Stock
Receiving and managing new stock effectively is crucial for maintaining optimal inventory levels and ensuring seamless warehouse operations. The process begins with thoroughly inspecting incoming shipments for accuracy and quality, checking for any damage or discrepancies. Verifying that items match purchase orders helps prevent inventory inaccuracies and ensures that all necessary items are available for order fulfillment.
Once confirmed, organizing and labeling stock properly enhances accessibility and efficiency, enabling quicker retrieval during picking. Recording inventory in the Warehouse Management System (WMS) allows for real-time tracking of stock levels, facilitating informed decision-making for future restocking and improving overall operational efficiency in the warehouse.
Inspecting Incoming Shipments
A thorough inspection of incoming shipments is essential to identify any damage or discrepancies. Compare items against purchase orders and packing slips to ensure everything is correct. Addressing issues promptly with suppliers prevents inventory inaccuracies and stockouts. This step protects the integrity of your inventory and helps maintain strong supplier relationships by ensuring accountability for any discrepancies found during the receiving process.
Organizing Received Stock
Once shipments are verified, it’s important to organize the stock systematically within the warehouse. Use clear labeling and designated storage areas to facilitate easy access and efficient picking. Group similar items together, which not only helps reduce search time but also promotes better inventory management. An organized storage system enhances operational efficiency and minimizes the risk of errors during order fulfillment.
Recording in the WMS
After organizing, promptly record all received stock in your Warehouse Management System (WMS). Accurate data entry regarding stock quantities and locations is vital for maintaining real-time inventory visibility. This practice prevents issues like stockouts and overstocking while allowing for more effective inventory audits. Keeping the WMS updated ensures that all team members have access to the latest information, supporting better decision-making.
Implementing FIFO or LIFO
Consider implementing inventory management methods like First-In, First-Out (FIFO) or Last-In, First-Out (LIFO) based on the nature of your products. FIFO is particularly effective for perishable items, ensuring that older stock is sold first and reducing waste. Conversely, LIFO can be advantageous for items with fluctuating prices, allowing businesses to sell the newest stock first. Choose the method that aligns best with your inventory management goals.
Shipping Your Orders
Shipping orders efficiently is vital for customer satisfaction and overall business success. The process begins with accurately picking items from inventory, ensuring that the right products are selected for each order. After picking, careful packing is essential to prevent damage during transit; this includes using suitable packing materials that protect the items.
Choosing the right shipping method based on cost, speed, and delivery requirements ensures the timely arrival of orders, which is crucial for maintaining customer trust. Properly labeling packages and maintaining organized documentation further streamline the shipping process, making it easier to track shipments and resolve any issues that may arise.
Picking Orders
The first step in the shipping process is picking the correct items from the warehouse. Utilize efficient picking methods, such as batch picking or wave picking, to streamline this task. Ensure that employees have access to clear order lists, minimizing the chances of errors. Training staff on the importance of accuracy in picking is essential to ensure customer satisfaction and reduce returns.
Packing Orders
Once items are picked, they must be packed carefully to prevent damage during transit. Use appropriate packing materials, such as bubble wrap or foam peanuts, to cushion fragile items. Label packages with shipping information, including the destination address and any necessary handling instructions. Proper packing not only protects products but also enhances the overall presentation, leading to a better customer experience.
Labeling and Documentation
Labeling is a critical component of the shipping process. Ensure that each package has a clear shipping label that includes the recipient's address, return address, and tracking information. Document all shipments in your Warehouse Management System (WMS) to maintain accurate records of what has been shipped and when. This step enables efficient tracking and helps resolve any issues that may arise during transit.
Timely Shipping
Timely shipping is essential for customer satisfaction and loyalty. Establish efficient processes to ensure that orders are shipped as quickly as possible after being packed. Monitor shipping carriers for reliability and cost-effectiveness, and consider offering multiple shipping options to meet different customer needs. Prompt delivery not only enhances the customer experience but also builds trust and encourages repeat purchases.
Measuring Warehouse Performance
Measuring warehouse performance is essential for identifying areas of improvement and optimizing operations. Key performance indicators (KPIs) provide valuable insights into various aspects of warehouse efficiency, including order accuracy, inventory turnover, and picking speed. By regularly analyzing these metrics, businesses can assess their operational effectiveness and implement targeted strategies to enhance productivity.
For instance, tracking order fulfillment times can help identify bottlenecks in the shipping process, while monitoring inventory accuracy ensures that stock levels align with demand. Additionally, employee performance metrics can highlight training needs or process inefficiencies. By focusing on continuous improvement, organizations can enhance their warehouse operations, reduce costs, and ultimately improve customer satisfaction.
Technology in Warehouse Management
Technology plays a transformative role in warehouse management, enhancing efficiency, accuracy, and productivity. Advanced Warehouse Management Systems (WMS) enable real-time inventory tracking, automated order processing, and improved data analytics, allowing businesses to make informed decisions.
Automation technologies such as robotics and conveyor systems streamline picking and packing processes, reducing labor costs and minimizing errors. Furthermore, integrating Internet of Things (IoT) devices provides valuable insights into equipment performance and inventory levels. Overall, leveraging technology in warehouse management not only optimizes operations but also enhances customer satisfaction by ensuring timely and accurate order fulfillment.
- Warehouse Management Systems (WMS): WMS software automates inventory tracking and order processing, providing real-time visibility into stock levels and enhancing operational efficiency in warehouses.
- Automation Technologies: Robotics and automation streamline tasks like picking, packing, and sorting, reducing labor costs while improving speed and accuracy in warehouse operations.
- Internet of Things (IoT): IoT devices provide real-time data on equipment performance and inventory levels, helping optimize operations and improve decision-making processes in warehouses.
- Data Analytics: Advanced analytics tools analyze warehouse performance metrics, enabling businesses to identify trends, forecast demand, and implement strategies for continuous improvement.
- Mobile Technologies: Mobile devices enable warehouse staff to access information on the go, enhancing communication, speeding up processes, and improving overall operational efficiency.
Conclusion
In conclusion, effective warehouse management is vital for businesses striving to optimize their supply chain operations and enhance customer satisfaction. By implementing a robust Warehouse Management System (WMS) and leveraging modern technologies, organizations can streamline processes, improve inventory accuracy, and reduce operational costs.
The integration of automation, IoT devices, and data analytics further enables real-time visibility into warehouse activities, empowering businesses to make informed decisions and respond swiftly to market demands.
Frequently asked questions
A Warehouse Management System (WMS) is software that optimizes warehouse operations, including inventory tracking, order fulfillment, and shipping, enhancing efficiency and accuracy in managing stock levels.
A WMS improves efficiency by automating tasks such as inventory management and order processing, reducing manual errors, and speeding up workflows, resulting in faster order fulfillment and lower operational costs.
Automating warehouse processes reduces labor costs, minimizes errors, and increases speed and accuracy. It streamlines operations, enhances productivity, and allows staff to focus on more critical tasks.
Warehouse performance can be measured using key performance indicators (KPIs) such as order accuracy, inventory turnover, picking speed, and fulfillment times to identify areas for improvement.
Inventory accuracy is crucial because it prevents stockouts and overstocking, improves customer satisfaction, and enhances decision-making related to purchasing, production, and inventory management strategies.
Technology enhances warehouse management by providing real-time data, automating tasks, improving inventory tracking, and enabling data analytics, which all contribute to more efficient operations and better decision-making.