Solutions for every business need
Growth comes in all shapes and sizes. Whether it’s smoother operations, sharper insights, higher revenue—or all of the above—we’ve got you covered
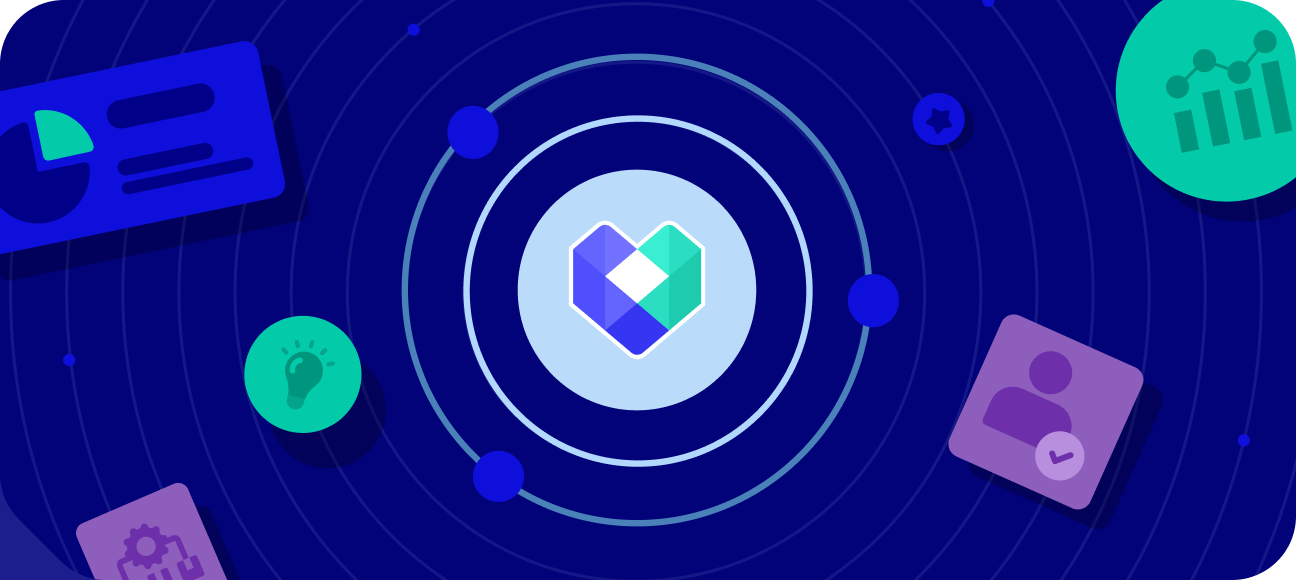
Warehouse management made simple
Gain full control over your inventory with smart automation, real-time tracking, and efficient workflows—ensuring your stock moves smoothly, every time
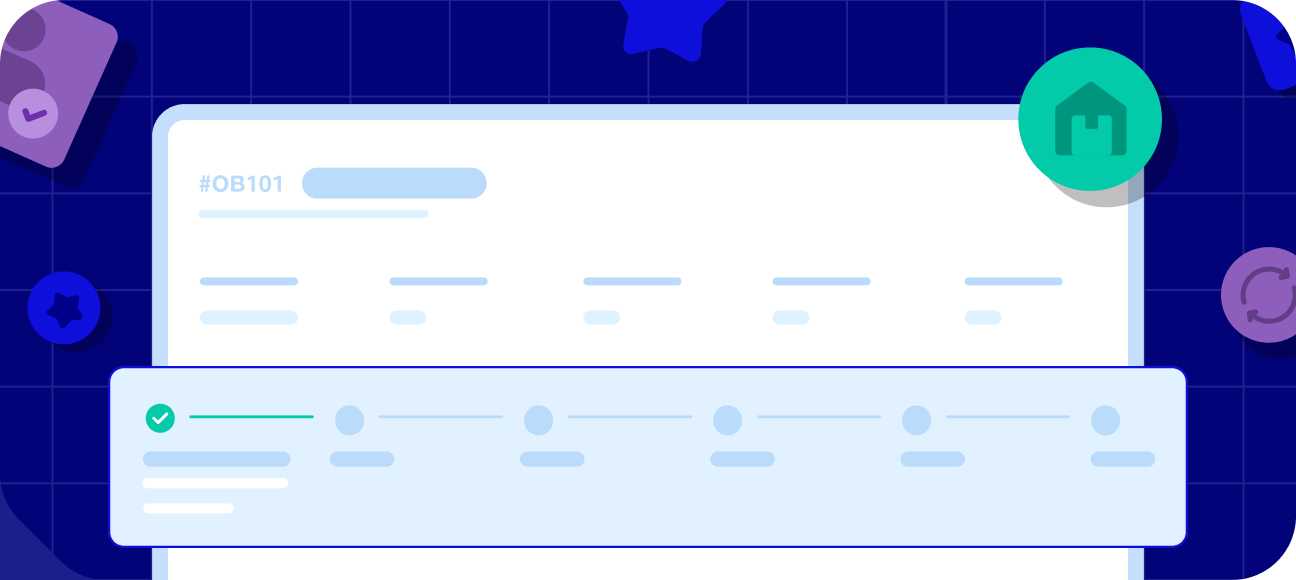
Launch hyperlocal commerce instantly
Set up and scale your hyper-local e-commerce with easy tools for web, orders, and delivery management—bringing you closer to customers, faster
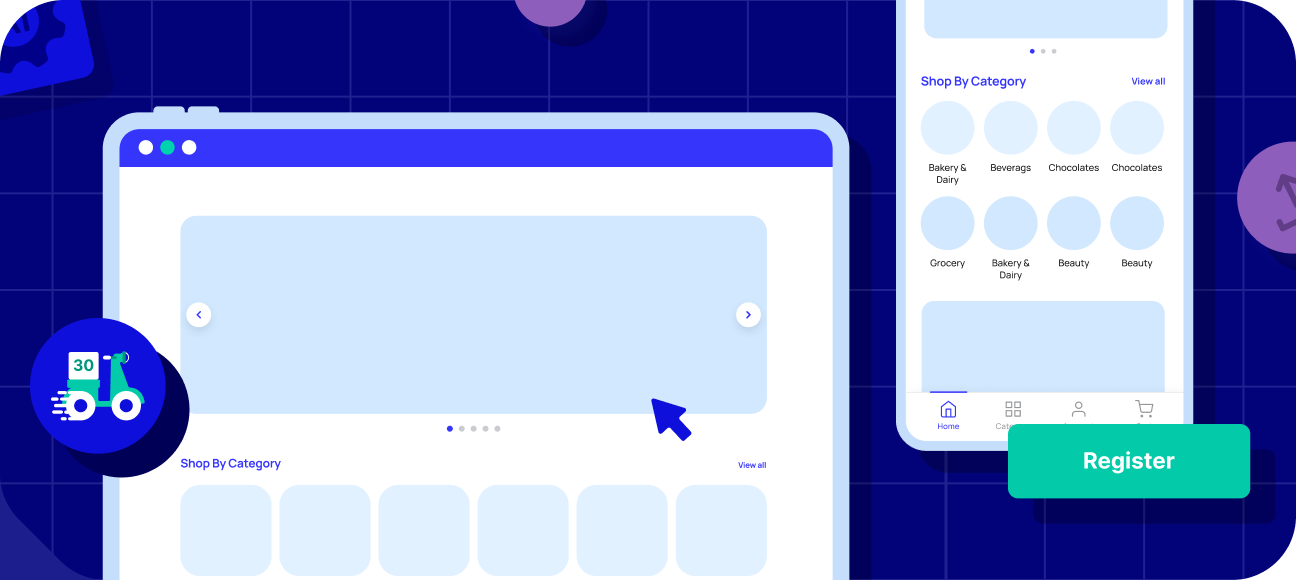
Delivery management made easy
Gain control over your deliveries with real-time visibility, smart automation, and seamless coordination—ensuring on-time arrivals, every time
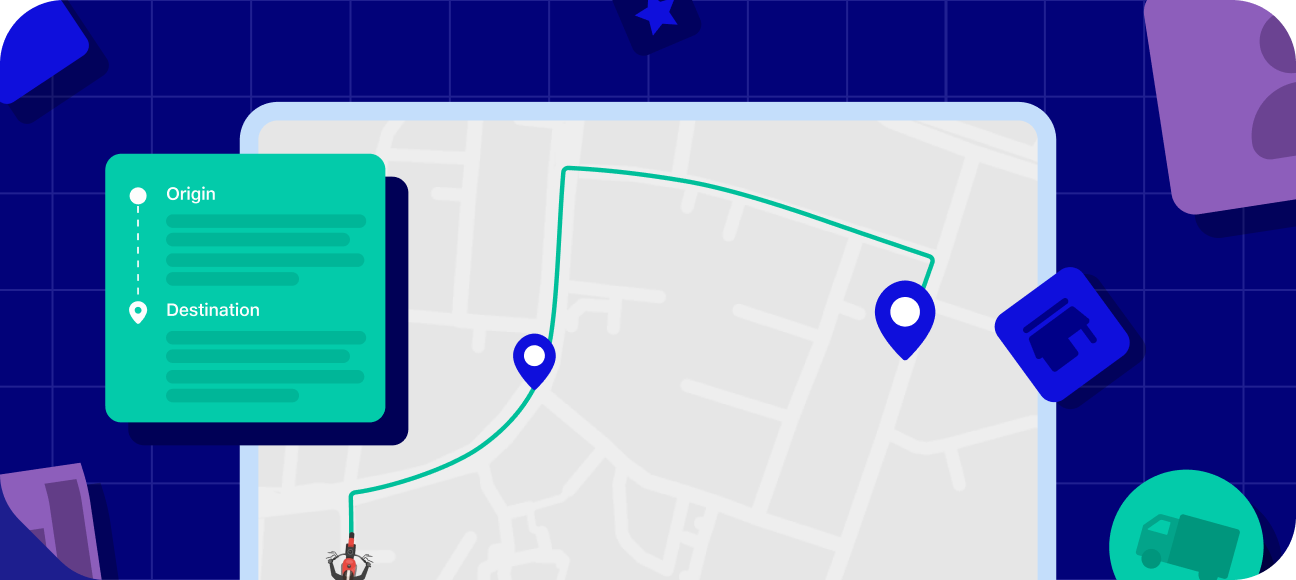
Order management made easy
Master every order with full visibility, smart automation, and effortless control—delivering the right outcomes, every time
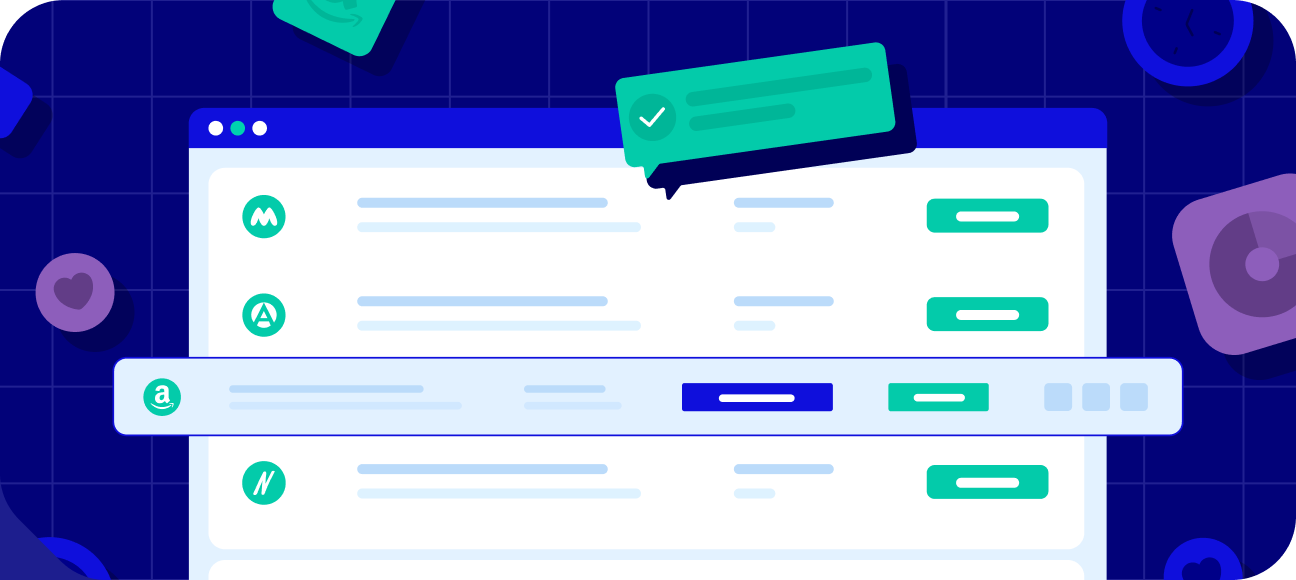
Speak to an expert
Explore how Fynd Commerce can improve every aspect of your business, from online to instore and beyond
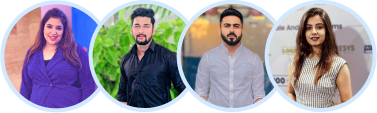
Speak to an expert
Explore how Fynd WMS powers operational excellence with our solution experts
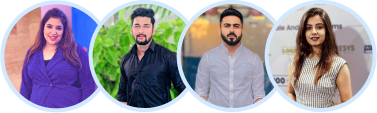
Speak to an expert
Explore how Fynd Quick powers hyperlocal businesses with our solution experts
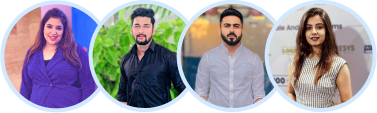
Speak to an expert
Explore how Fynd TMS powers better deliveries with our solution experts
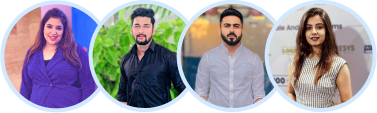
Speak to an expert
Explore how Fynd OMS powers seamless order management with our solution experts
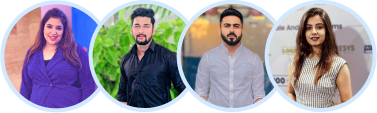
Featured Blog
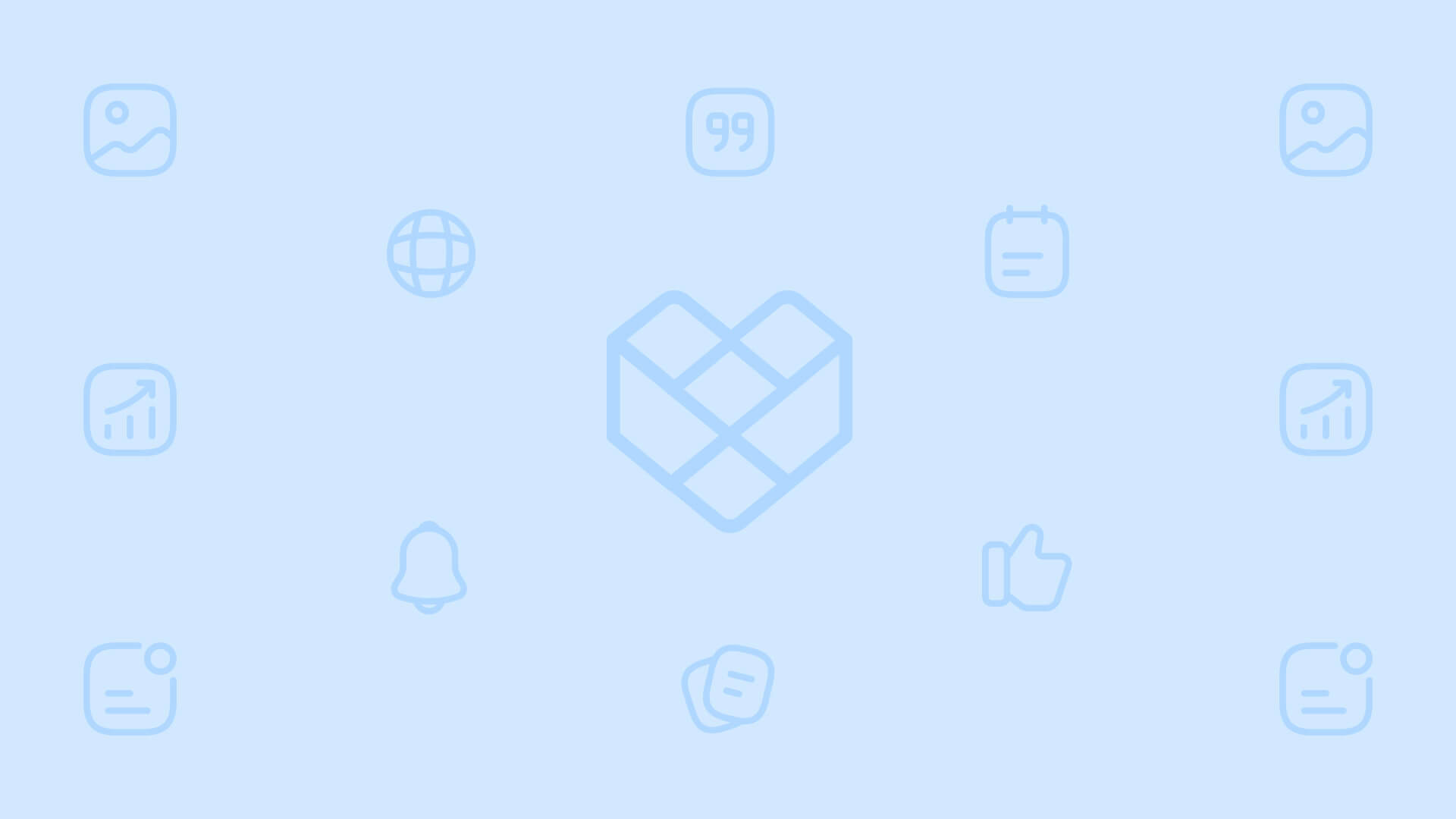
Empower your business, every step of the way
Simplify operations, scale smarter, and deliver better experiences with solutions designed to grow with your business
Take your warehouse management to the next level
Experience hassle-free inventory management with Fynd WMS, designed to keep your operations efficient and accurate. Book a demo to see how Fynd WMS can boost productivity and profits for your business!
Kickstart your quick delivery website
Experience seamless hyper-local commerce with Fynd Quick—engineered to keep things running smoothly and help you reach customers in record time. Book a demo and see how Fynd Quick can drive efficiency and growth for your business!
Level up your delivery management
See how you can manage deliveries with Fynd TMS, designed to streamline operations and keep your customers delighted. Book a demo with our team and find out how Fynd TMS can boost your efficiency and bottom line!
Take your order management to the next level
Discover how effortless order management can be with Fynd OMS, built to keep things running smoothly and make your customers happy. Book a demo with our team and see how Fynd OMS can help boost your efficiency and profits!
A Warehouse Management System (WMS) is a sophisticated software solution designed to optimize and streamline warehouse operations. It encompasses all activities related to managing goods from the moment they enter a warehouse until they are shipped out. This includes processes such as receiving, inventory management, order fulfillment, and shipping. By providing real-time visibility into inventory levels and locations, a WMS enables organizations to manage their resources more effectively, ensuring that the right products are available at the right time and place.
The significance of a WMS has grown in tandem with the increasing complexity of supply chains and the rising expectations for faster delivery times. As e-commerce continues to expand, businesses face pressure to fulfill orders quickly and accurately. A WMS addresses these challenges by automating manual tasks, relieving businesses from the burden of repetitive work, reducing errors, and enhancing overall operational efficiency. It integrates with other systems, such as Enterprise Resource Planning (ERP) and Transportation Management Systems (TMS), creating a seamless flow of information across the supply chain.
In addition to improving efficiency, a WMS also contributes to better decision-making through advanced analytics and reporting capabilities. Organizations can leverage data insights to forecast demand, optimize inventory levels, and improve customer service. This empowerment in decision-making is a key benefit of WMS implementation.
What is a Warehouse Management System
A Warehouse Management System (WMS) is software designed to optimize warehouse operations by managing the movement and storage of goods. It provides real-time visibility into inventory, overseeing processes like receiving, inventory management, order fulfillment, and shipping.
With the growth of e-commerce and rising customer expectations for fast delivery, WMS has become essential for streamlining operations and reducing costs. Integrated with systems like ERP and TMS, a WMS automates key processes and offers analytics that enhance efficiency, improve supply chain management, and boost customer satisfaction. Its adaptability to different business sizes and needs makes it a popular choice among businesses seeking a modern and resilient WMS solution.
Types of Warehouse Management Systems
Warehouse Management Systems (WMS) come in various forms, each tailored to meet the unique needs of businesses. While the primary purpose of a WMS is to optimize warehouse operations, the specific features and functionalities can vary depending on the type of system.
Understanding the different types of WMS is crucial for businesses. It helps them select the most suitable solution that aligns with their operational requirements and goals. This section will explore the most common types of WMS, highlighting their key characteristics and benefits.
1. Standalone WMS
A standalone WMS is an independent software solution focused solely on warehouse operations, offering inventory tracking, order picking, packing, and shipping functionalities. It is an ideal choice for small to medium-sized businesses with limited budgets and resources, providing a cost-effective and straightforward implementation process.
2. Cloud-Based WMS
Cloud-based WMS is a web-based solution hosted on external servers, providing scalability, flexibility, and optimized processes for businesses of all sizes. It offers reduced implementation costs, increased accessibility, and real-time data visibility, making it a popular choice among businesses seeking a modern and adaptable WMS solution.
3. Integrated ERP WMS
An Integrated ERP WMS combines warehouse management functionalities with broader Enterprise Resource Planning (ERP) systems. This integration allows for seamless data sharing across various business functions, such as accounting and inventory management. It is particularly beneficial for larger organizations that require comprehensive oversight of their operations, enabling real-time visibility and improved coordination among different departments.
4. Industry-Specific WMS
Industry-specific WMS are tailored to meet the unique needs of particular sectors, such as food and beverage, pharmaceuticals, or retail. These systems incorporate specialized features and compliance requirements relevant to the industry, ensuring that businesses can manage their operations effectively while adhering to regulatory standards. This customization enhances efficiency and accuracy in warehouse processes unique to each sector.
Key Components of a Warehouse Management System
A Warehouse Management System (WMS) is essential for managing and optimizing warehouse operations. It encompasses various components that facilitate the efficient movement and storage of goods within a warehouse. These components work together to streamline processes such as receiving, inventory management, order fulfillment, and shipping.
By integrating these functionalities, a WMS enhances operational efficiency, reduces errors, and improves overall inventory accuracy. Understanding the key components of a WMS is crucial for businesses aiming to optimize their warehouse management practices and achieve better supply chain performance.
- Inventory Management: This component provides real-time visibility into stock levels, enabling businesses to track inventory across multiple locations and manage stock replenishment effectively.
- Receiving and Put-Away: This functionality streamlines the process of obtaining goods and determining optimal storage locations based on predefined rules, ensuring efficient space utilization.
- Order Picking: The order picking component automates the selection of items for shipment, utilizing methods such as batch picking or wave picking to enhance efficiency and accuracy.
- Packing: This feature ensures that items are correctly packed for shipment, optimizing packing processes to reduce shipping costs and minimize damage during transit.
- Shipping Management: This component manages the logistics of outbound shipments, including carrier selection and tracking, ensuring timely delivery of products to customers.
- Labor Management: Labor management tools help track employee performance and productivity in the warehouse, enabling better workforce planning and optimization.
- Reporting and Analytics: Advanced reporting tools provide insights into warehouse performance metrics, helping managers make informed decisions based on data-driven analysis.
Benefits of Implementing a WMS
A Warehouse Management System (WMS) is a sophisticated software solution specifically designed to enhance the efficiency and effectiveness of warehouse operations. In today’s fast-paced business environment, where customer expectations are constantly evolving, the need for a robust WMS has become increasingly critical.
By automating various processes within the warehouse, a WMS significantly improves inventory accuracy, ensuring that stock levels are correctly tracked and managed. This automation minimizes the likelihood of human errors, such as misspeaks or incorrect shipments, which can lead to costly returns and dissatisfied customers.
- Improved Operational Efficiency: A WMS automates warehouse processes from receiving to shipping, minimizing manual data entry and enabling efficient handling of higher volumes. It reduces errors, enhancing order accuracy and decreasing returns, which boosts customer satisfaction.
- Enhanced Labor Management: A WMS forecasts labor needs, optimizes task assignments and increases workforce productivity while ensuring a safer work environment.
- Cost Reduction: By optimizing space utilization and inventory management, a WMS significantly lowers warehousing costs related to excess stock and inefficient processes.
- Better Customer Satisfaction: Improved order accuracy and faster fulfillment times lead to enhanced service levels and increased customer loyalty.
- Data-Driven Decision Making: Advanced reporting and analytics enable businesses to analyze performance metrics, accurately forecast demand, and optimize warehouse operations.
Steps in Implementing a Warehouse Management System
Implementing a Warehouse Management System (WMS) is a critical endeavor that can transform warehouse operations and enhance overall efficiency. The process involves several key steps, each designed to ensure that the system meets the specific needs of the business while minimizing disruptions.
From initial planning and stakeholder engagement to system configuration and user training, each phase plays a vital role in the successful deployment of the WMS. By following a structured approach, organizations can effectively navigate the complexities of implementation and realize the full benefits of their new system.
Step 1: Define Project Scope and Goals
The first step is to define the scope and objectives of the WMS implementation clearly. This involves identifying specific business needs, desired outcomes, and key performance indicators (KPIs) that will measure success. A well-defined project scope ensures that all stakeholders are aligned and that the system will effectively address operational challenges.
Step 2: Assemble a Dedicated Implementation Team
Creating a dedicated implementation team is crucial for managing the project effectively. This team should include representatives from various departments—such as IT, operations, and logistics—who can provide valuable insights and expertise throughout the implementation process. Their diverse perspectives help ensure that the WMS meets the needs of all users and integrates seamlessly into existing workflows.
Step 3: Conduct a Thorough Business Process Analysis
Before implementing a WMS, it is essential to conduct a comprehensive analysis of existing business processes. This step involves mapping out current workflows, identifying inefficiencies, and determining how the WMS can improve operations. By understanding the strengths and weaknesses of current practices, businesses can tailor the WMS to address specific needs and enhance overall efficiency.
Step 4: Installation and Configuration
Once the analysis is complete, the next step is to install and configure the WMS software. This involves working closely with the WMS provider to set up the system according to the unique operational data of the warehouse. Proper configuration ensures that the system aligns with business processes and can effectively support day-to-day operations, including inventory management, order processing, and shipping logistics.
Step 5: Customization and Testing
After installation, businesses should customize the WMS to suit their specific operational requirements. This includes adjusting settings, features, and workflows to optimize performance. Following customization, rigorous testing is crucial to ensure that all functionalities work as intended. Testing various scenarios helps identify any potential issues before going live, allowing for adjustments to be made proactively.
Step 6: User Training and Adoption
Effective user training is vital for successful WMS implementation. This step involves developing a training program that covers all aspects of the system, from basic navigation to advanced functionalities. Training should be tailored to different user roles within the organization, ensuring that all employees are equipped to utilize the system effectively. Fostering user adoption through hands-on training sessions can significantly enhance overall productivity.
Step 7: Integration and Data Migration
Integrating the WMS with existing systems and migrating data from legacy systems is a critical step in the implementation process. This involves ensuring that all relevant data—such as inventory levels, customer information, and order history—is accurately transferred into the new system. Proper integration with other software solutions (e.g., ERP or CRM systems) enhances data flow and visibility across operations.
Step 8: Go-Live Planning
The final step in implementing a WMS is careful planning for the go-live phase. This includes preparing for potential challenges that may arise during the transition to the new system. Businesses should establish a timeline for going live, communicate this timeline with all stakeholders, and ensure that adequate support is available during the initial rollout period. Monitoring system performance closely after going live allows for quick resolution of any issues that may occur, ensuring a smooth transition into full-scale operation.
Challenges in WMS Implementation
Implementing a Warehouse Management System (WMS) is a complex process that requires careful planning and execution. Despite the many benefits a WMS can bring, such as improved efficiency, reduced costs, and better customer service, there are several challenges that organizations may face during implementation.
These challenges can range from selecting the right system and vendor to ensuring user adoption and managing change. Failing to address these challenges can lead to delays, cost overruns, and suboptimal performance of the WMS. Understanding and mitigating these challenges is crucial for a successful implementation.
- Selecting the Right System and Vendor: Choosing the appropriate WMS and vendor that aligns with the organization's specific needs and requirements is critical.
- Data Accuracy and Migration: Ensuring the accuracy and integrity of data during the migration process is a significant challenge.
- Integration with Existing Systems: Integrating the WMS with other systems, such as ERP, TMS, or CRM, can be complex and time-consuming.
- Change Management and User Adoption: Implementing a WMS often requires changes in processes and workflows, which can be met with resistance from employees.
- Customization and Configuration: Every organization has unique requirements and processes, which may necessitate customization and configuration of the WMS.
- Ongoing Support and Maintenance: After the initial implementation, providing ongoing support, maintenance, and optimization of the WMS is crucial.
Project Planning for WMS Implementation
Project planning for a Warehouse Management System (WMS) implementation is a crucial phase that establishes the groundwork for a successful deployment. This process involves defining clear objectives, assembling a dedicated team, and outlining the necessary steps to ensure that the WMS meets the specific needs of the organization.
Effective project planning helps mitigate risks, allocate resources efficiently, and establish a timeline for implementation. By carefully considering all aspects of the project, businesses can enhance their chances of achieving a smooth transition to the new system and realize the full benefits of improved warehouse operations.
- Understand Your Business Requirements: Clearly define what your business needs from the WMS.
- Identify Key Stakeholders: Engage key stakeholders early in the planning process to ensure their needs and expectations are considered.
- Establish the Implementation Team: Assemble a dedicated implementation team responsible for managing the project.
- Define Project Scope and Goals: This ensures that all stakeholders are aligned on what the project aims to achieve and helps set measurable success criteria.
- Conduct a Thorough Business Process Analysis: Analyze current warehouse processes to identify inefficiencies and areas for improvement.
- Create a Detailed Project Plan: Develop a comprehensive project plan that outlines timelines, milestones, responsibilities, and resource allocation. A well-structured plan minimizes risks and keeps the project on track.
- Allocate Resources Effectively: Determine the necessary resources—budget, personnel, and technology—for successful implementation. Proper resource allocation helps avoid delays and ensures that all aspects of the project are adequately supported.
- Plan for Training and Change Management: Develop a training program to ensure users are comfortable with the new system. Additionally, implement change management strategies to address potential resistance from employees during the transition process.
- Monitor Progress and Adjust as Needed: Regularly review project progress against established milestones. Be prepared to make adjustments based on feedback or unforeseen challenges to keep the implementation on track for success.
Conclusion
Implementing a Warehouse Management System (WMS) is a transformative process that can significantly enhance warehouse operations and supply chain performance. By automating processes, improving inventory accuracy, and optimizing labor management, a WMS delivers tangible benefits such as reduced costs, increased productivity, and better customer satisfaction. However, successful implementation requires careful planning, stakeholder engagement, and change management. By following a structured approach and addressing key challenges, businesses can navigate the complexities of WMS implementation and realize the full potential of their investment.
Frequently asked questions
A Warehouse Management System (WMS) is software designed to manage and optimize warehouse operations, including inventory tracking, order fulfillment, and shipping. It provides real-time visibility into inventory levels and locations, automating processes to enhance efficiency and accuracy. A WMS helps businesses streamline their operations, reduce costs, and improve customer satisfaction by ensuring that the right products are available at the right time.
Implementing a WMS offers numerous benefits, including improved operational efficiency, reduced errors, and enhanced inventory accuracy. It streamlines order fulfillment processes, optimizes labor management, and provides real-time visibility into stock levels. Additionally, a WMS can lead to lower operational costs and increased productivity while improving customer satisfaction through timely and accurate order deliveries. Overall, these advantages contribute to better supply chain performance.
Choosing the right WMS involves assessing your specific business needs and operational requirements. Consider factors such as system functionality, scalability, integration capabilities with existing software, and vendor support. Engage key stakeholders to gather insights on necessary features and evaluate potential solutions through demos or trials. Additionally, review customer testimonials and case studies to understand how the WMS has performed in similar industries.
Challenges during WMS implementation may include selecting the right system and vendor, ensuring data accuracy during migration, integrating with existing systems, and managing change among employees. Resistance to new processes can hinder user adoption if not addressed effectively. Additionally, customization needs may complicate implementation timelines. To mitigate these challenges, thorough planning, stakeholder engagement, and effective training are essential.
The timeline for implementing a WMS varies based on factors such as the complexity of operations, system customization needs, data migration requirements, and employee training. Typically, a WMS implementation can take anywhere from a few months to over a year. Proper project planning and resource allocation can help ensure that the implementation proceeds smoothly and stays within the established timeline.
Yes, ongoing support is crucial after implementing a WMS to ensure optimal performance and user satisfaction. Regular maintenance helps address any technical issues that arise and allows for updates or enhancements as business needs evolve. Additionally, continuous training for staff ensures they remain proficient in using the system effectively. Establishing a dedicated support team can help organizations adapt to changes in operations or technology over time.