Solutions for every business need
Growth comes in all shapes and sizes. Whether it’s smoother operations, sharper insights, higher revenue—or all of the above—we’ve got you covered
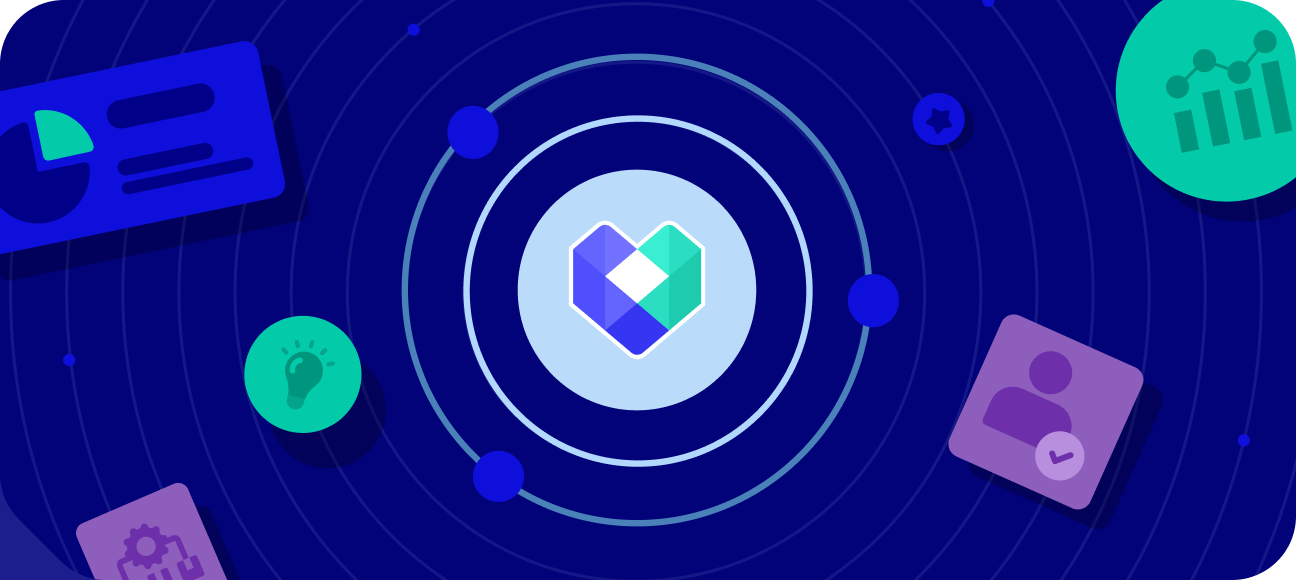
Warehouse management made simple
Gain full control over your inventory with smart automation, real-time tracking, and efficient workflows—ensuring your stock moves smoothly, every time
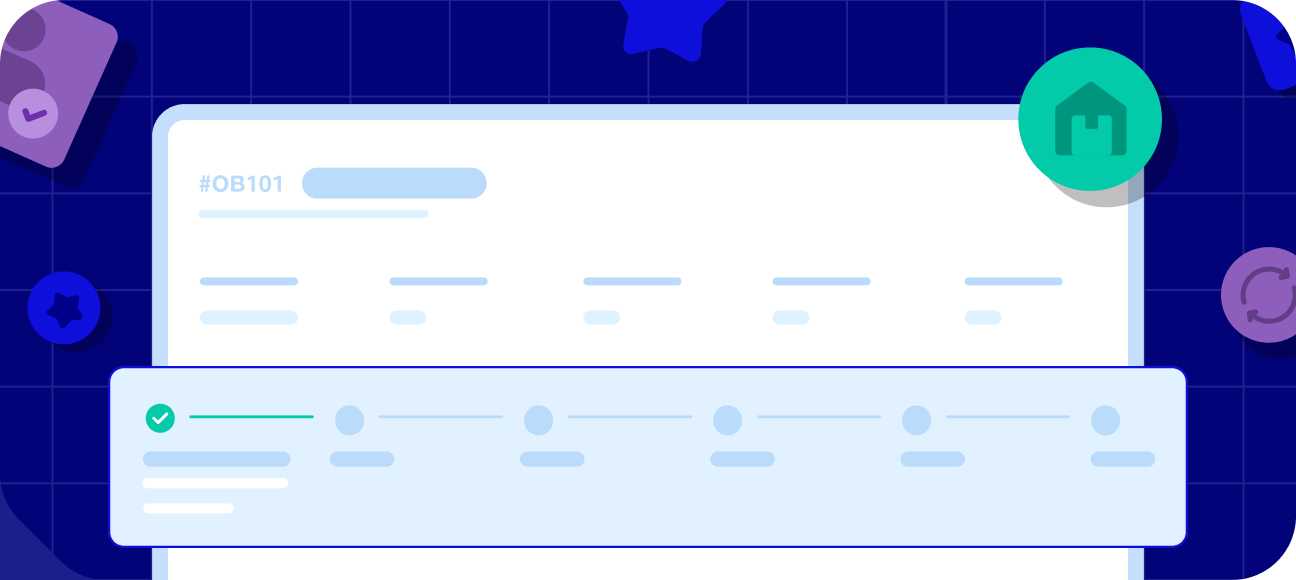
Launch hyperlocal commerce instantly
Set up and scale your hyper-local e-commerce with easy tools for web, orders, and delivery management—bringing you closer to customers, faster
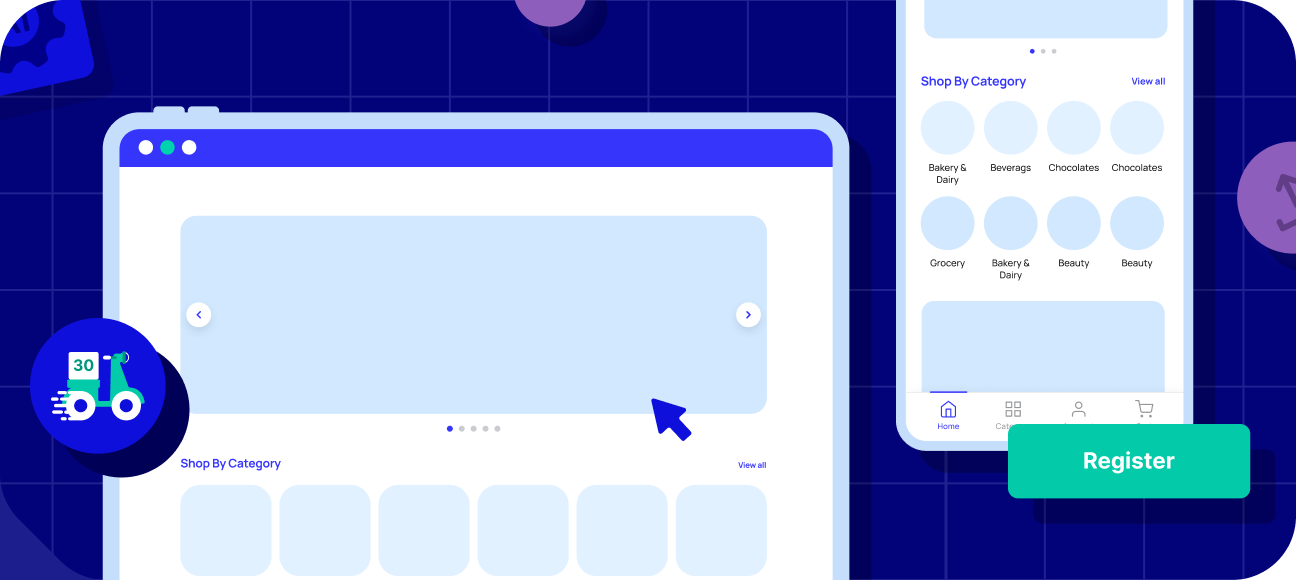
Delivery management made easy
Gain control over your deliveries with real-time visibility, smart automation, and seamless coordination—ensuring on-time arrivals, every time
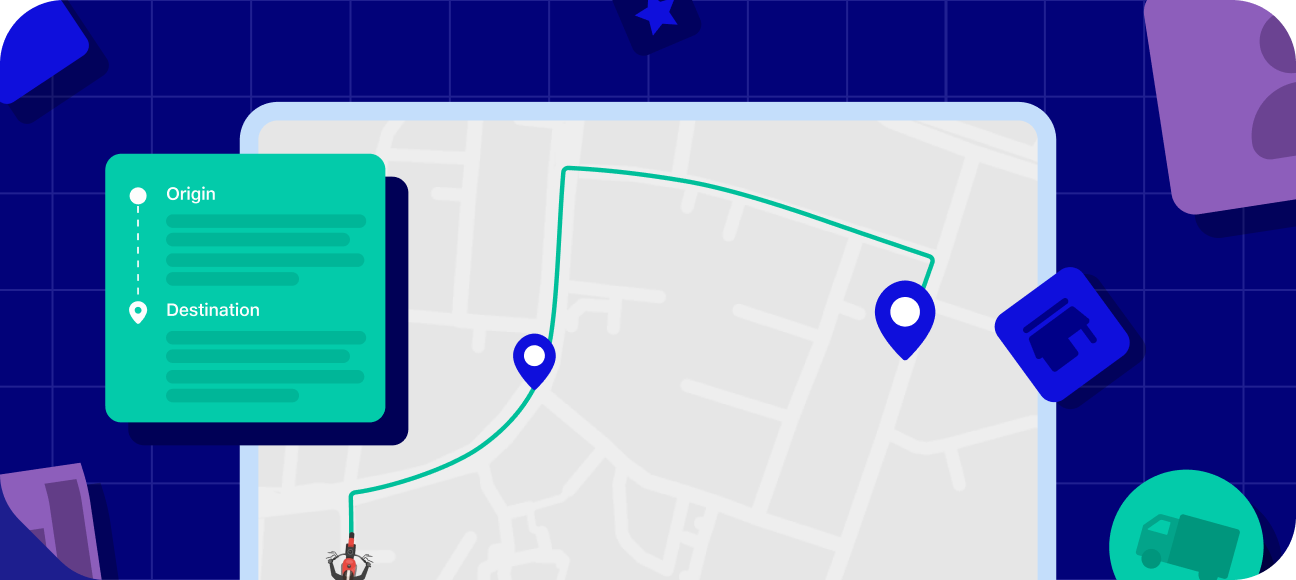
Order management made easy
Master every order with full visibility, smart automation, and effortless control—delivering the right outcomes, every time
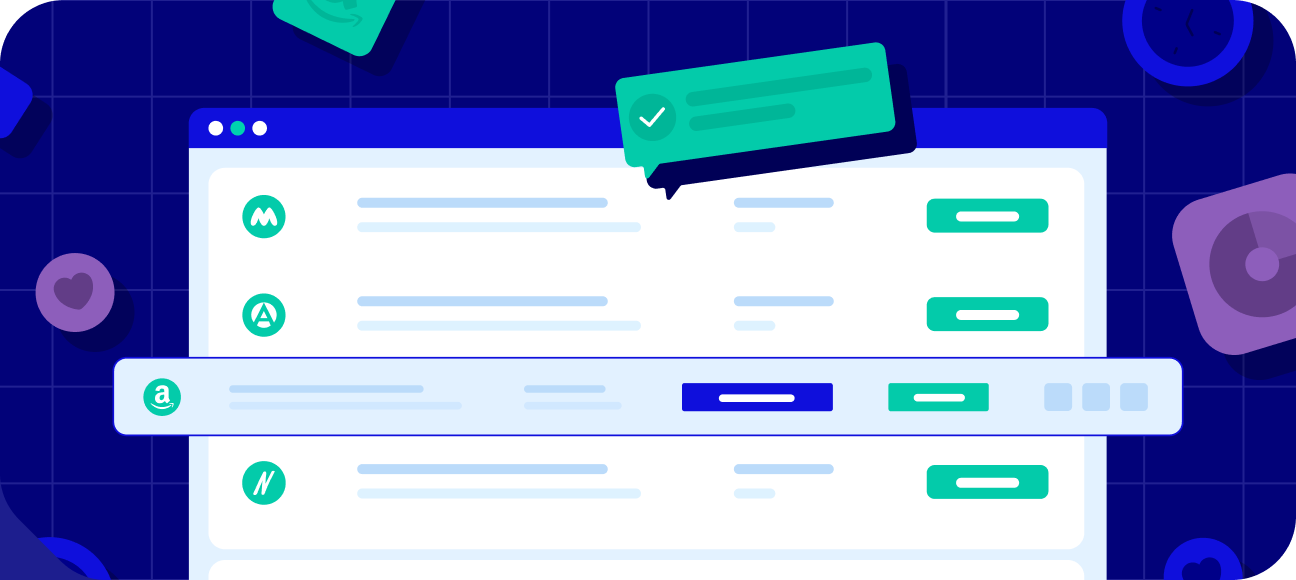
Speak to an expert
Explore how Fynd Commerce can improve every aspect of your business, from online to instore and beyond
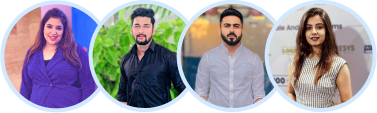
Speak to an expert
Explore how Fynd WMS powers operational excellence with our solution experts
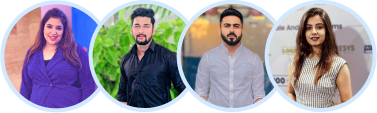
Speak to an expert
Explore how Fynd Quick powers hyperlocal businesses with our solution experts
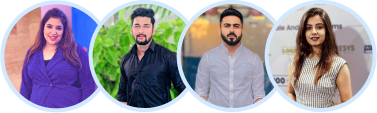
Speak to an expert
Explore how Fynd TMS powers better deliveries with our solution experts
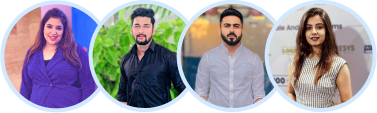
Speak to an expert
Explore how Fynd OMS powers seamless order management with our solution experts
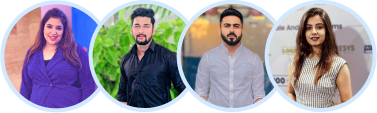
Featured Blog
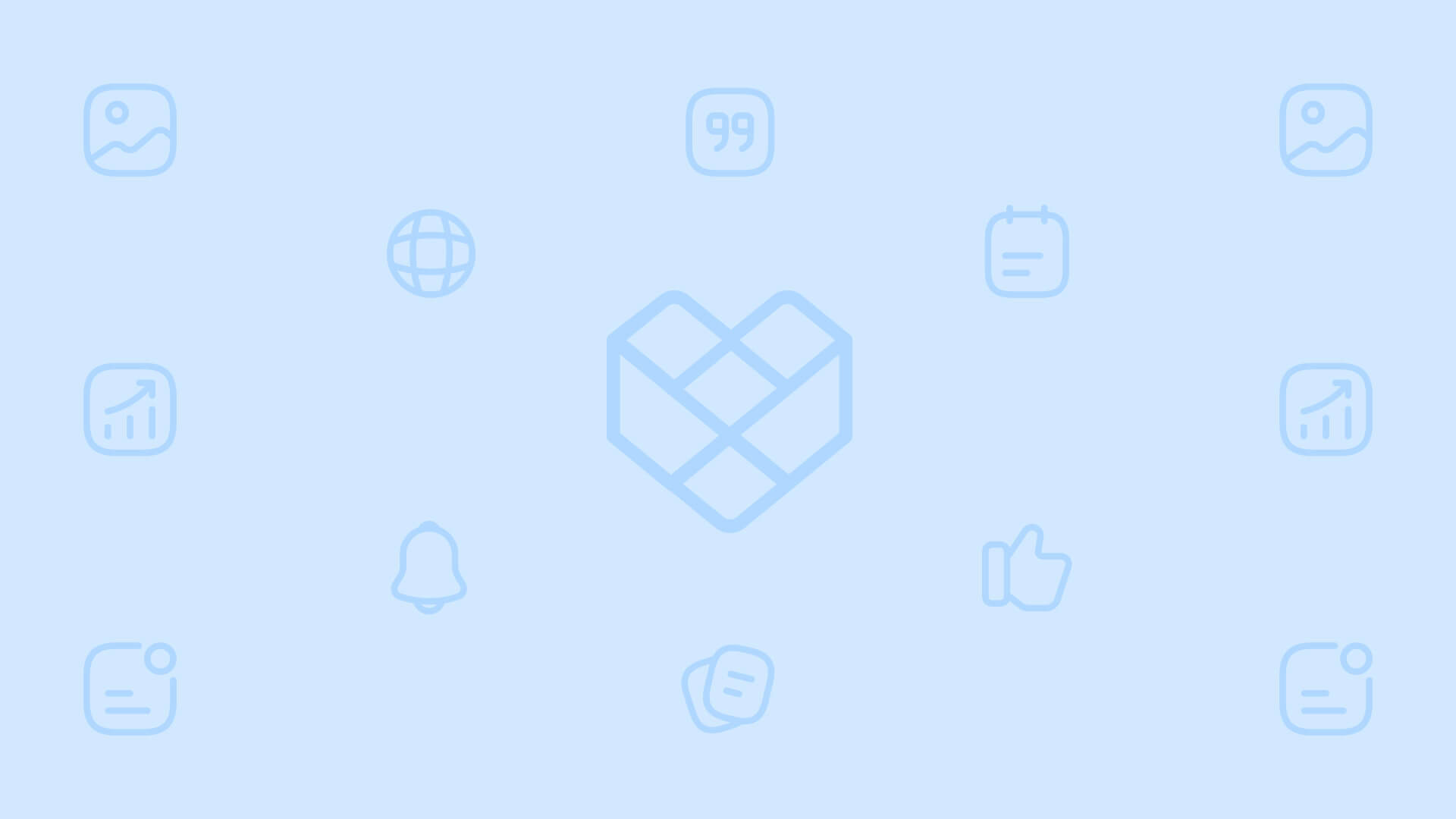
Empower your business, every step of the way
Simplify operations, scale smarter, and deliver better experiences with solutions designed to grow with your business
Take your warehouse management to the next level
Experience hassle-free inventory management with Fynd WMS, designed to keep your operations efficient and accurate. Book a demo to see how Fynd WMS can boost productivity and profits for your business!
Kickstart your quick delivery website
Experience seamless hyper-local commerce with Fynd Quick—engineered to keep things running smoothly and help you reach customers in record time. Book a demo and see how Fynd Quick can drive efficiency and growth for your business!
Level up your delivery management
See how you can manage deliveries with Fynd TMS, designed to streamline operations and keep your customers delighted. Book a demo with our team and find out how Fynd TMS can boost your efficiency and bottom line!
Take your order management to the next level
Discover how effortless order management can be with Fynd OMS, built to keep things running smoothly and make your customers happy. Book a demo with our team and see how Fynd OMS can help boost your efficiency and profits!
A Warehouse Management System (WMS) is a crucial software solution designed to optimize and manage warehouse operations effectively. It encompasses a range of processes, from the receipt of goods to their dispatch, ensuring that inventory is accurately tracked throughout its lifecycle. By providing real-time visibility into inventory levels, a WMS aids organizations in making informed decisions regarding stock management, thereby enhancing overall operational efficiency and reducing costs associated with inventory handling.
The primary functions of a WMS include inventory tracking, order fulfillment, picking, packing, and shipping. It utilizes technologies such as barcode scanning and RFID to automate data capture, which minimizes manual errors and accelerates processes. Furthermore, a WMS can integrate with other systems like Enterprise Resource Planning (ERP) and Transportation Management Systems (TMS), facilitating seamless communication across various supply chain components. This integration is vital for synchronizing inventory data and ensuring that warehouses operate in alignment with broader business objectives.
In today's fast-paced e-commerce environment, the demand for efficient warehouse management has surged. A well-implemented WMS not only streamlines operations but also enhances customer satisfaction by ensuring timely and accurate order fulfillment. As businesses continue to adapt to changing market dynamics, the role of WMS in supporting logistics and supply chain management becomes increasingly indispensable.
What is a Custom WMS?
A Custom Warehouse Management System (WMS) is a tailored software solution designed specifically to meet the unique operational needs of a warehouse. Unlike off-the-shelf systems, which offer generic functionalities, a custom WMS is developed to align with specific business processes, allowing for greater flexibility and efficiency in managing inventory, order fulfillment, and logistics.
The value of a custom WMS lies in its ability to integrate seamlessly with existing systems and adapt as the business evolves. It provides real-time visibility into inventory levels, automates routine tasks, and generates insightful reports that facilitate informed decision-making.
Steps to Building a Strong Business Case for a WMS
Building a strong business case for a Warehouse Management System (WMS) is essential for securing approval and funding for this critical investment. A well-structured business case clearly articulates the need for a WMS, outlines the expected benefits, and demonstrates how the system aligns with organizational goals.
It should encompass a thorough analysis of current operational challenges, projected cost savings, and potential improvements in efficiency and accuracy. Additionally, it should highlight how a WMS can enhance customer satisfaction through timely order fulfillment. By following a systematic approach, businesses can effectively communicate the value of implementing a WMS to stakeholders and decision-makers.
1. Define the Problem
Identifying the gaps in your current warehouse management is the first step in building a business case for a WMS. Detail the existing challenges—such as stock inaccuracies, inefficient picking processes, or slow order fulfillment—that necessitate a new system. By clearly articulating these issues, you establish a compelling rationale for change, helping stakeholders understand the urgency and importance of investing in a WMS to enhance operational efficiency.
2. Set Objectives and Goals
Establishing clear objectives that the WMS implementation aims to achieve is crucial. These goals include improving inventory accuracy, increasing order processing speeds, or reducing operational costs. By aligning these objectives with broader company goals, you not only reinforce the strategic importance of the WMS but also provide measurable targets for success. This clarity helps stakeholders visualize the potential impact of the new system on overall business performance.
3. Conduct a Cost-Benefit Analysis
A comprehensive cost-benefit analysis is essential for demonstrating the financial implications of implementing a WMS. This involves calculating the total costs associated with acquisition, installation, and ongoing maintenance while comparing these figures against projected savings from improved operational efficiencies, reduced labor costs, and enhanced customer satisfaction. By presenting a clear financial picture, you can effectively justify the investment and highlight the potential return on investment (ROI) to stakeholders.
4. Research and Select a WMS Solution
Thoroughly researching various WMS options available in the market is critical to finding the right fit for your organization. Evaluate different systems based on features, scalability, ease of integration with existing software, and user-friendliness. Engaging with vendors, seeking demos, and reading customer reviews can provide valuable insights. Selecting the most suitable WMS solution ensures that it meets your specific operational needs and supports long-term growth.
5. Develop a Project Plan
Creating a detailed project plan is vital for the successful implementation of a WMS. This plan should outline the timeline for each phase of the project, resource allocation, and the roles and responsibilities of team members. Additionally, it should identify potential risks and outline mitigation strategies. A well-structured project plan not only provides a roadmap for implementation but also helps keep stakeholders informed and engaged throughout the process.
6. Identify Stakeholders
Identifying key stakeholders who the WMS implementation will impact is crucial for gaining support and ensuring smooth adoption. Engage with various departments, such as operations, IT, and finance, to gather their insights and address any concerns early in the process. By involving stakeholders from the outset, you can foster collaboration, reduce resistance to change, and build a sense of ownership that enhances the likelihood of successful implementation.
7. Address Change Management
Implementing a new WMS involves significant changes in processes and workflows, making effective change management essential. Develop a comprehensive change management strategy that includes training programs for staff, resources for ongoing support, and communication plans to keep everyone informed. By preparing employees for the transition and addressing their concerns, you can minimize disruptions and ensure that they are equipped to utilize the new system effectively.
8. Monitor and Measure Success
Establishing metrics for evaluating the success of the WMS post-implementation is crucial for demonstrating its impact on warehouse operations. Define key performance indicators (KPIs) such as inventory accuracy, order fulfillment times, and labor efficiency. Regularly monitor these metrics to assess performance improvements and ensure that objectives are being met over time. This ongoing evaluation not only validates the investment but also provides insights for continuous improvement in warehouse operations.
Successful WMS Implementation Case Studies
Successful Warehouse Management System (WMS) implementations have proven to enhance operational efficiency and streamline processes across various industries significantly. Case studies illustrate how companies have leveraged WMS to address specific challenges, improve inventory accuracy, and optimize order fulfillment.
For instance, Nature’s Best transformed its distribution processes by integrating a Manhattan Associates WMS, resulting in reduced labor costs and improved efficiency. Similarly, Men’s Wearhouse consolidated operations through a new WMS, achieving better resource allocation and cost management. These examples highlight the tangible benefits of implementing a tailored WMS solution that aligns with organizational goals and enhances overall performance.
Nature’s Best
Nature’s Best, a leader in health and natural foods distribution, faced high labor costs and inefficiencies in its distribution processes. By implementing a WMS with enVista, the company optimized its operations, reducing the number of times products were handled during distribution. The new system streamlined workflows, resulting in significant cost savings and improved service levels, ultimately enhancing the company's ability to meet growing demand in the market.
Performance Bike
Performance Bike successfully upgraded its WMS with enVista, achieving remarkable results within a six-month timeframe. The implementation led to an increase in picking efficiency, with units picked per hour rising by 50 to 100. By profiling SKU movements and optimizing storage mediums, Performance Bike not only enhanced productivity but also ensured seamless integration with existing systems, demonstrating the effectiveness of a well-executed WMS implementation.
Men’s Wearhouse
Men’s Wearhouse replaced its legacy system with a new WMS and warehouse control system (WCS) to consolidate its operations. This implementation allowed for dynamic product flow management and improved resource allocation across its distribution centers. The new system facilitated cross-docking opportunities, resulting in reduced processing costs and enhanced overall efficiency. The successful integration of WMS enabled the company to respond effectively to seasonal workload increases while maintaining high service levels.
Dale Farm
Dale Farm, a major player in the dairy industry, sought to improve picking rates and traceability in its central distribution center. Implementing ProWMS Warehouse Management Software with voice middleware enabled seamless integration with its ERP system. This enhanced real-time inventory visibility and accuracy, allowing for more efficient operations. The successful deployment of the WMS resulted in improved order processing times and better overall management of dairy product distribution across its multiple sites.
Claire’s Logistics
Claire’s Logistics achieved remarkable operational improvements by implementing a robust Warehouse Management System (WMS) that provided real-time visibility into inventory levels. This capability allowed the company to streamline workflows, significantly enhancing order fulfillment speed. With enhanced tracking capabilities, Claire’s Logistics could efficiently manage inventory movements and optimize warehouse space utilization.
Christmas Tradition
Christmas Tradition faced significant challenges with inventory accuracy and order fulfillment during peak seasons. By implementing ProVision WMS, they tailored the system to their unique operational needs, enhancing inventory management and streamlining workflows. The new system provided real-time visibility into stock levels, allowing for proactive decision-making. As a result, Christmas Tradition improved order processing times and overall efficiency, successfully managing increased demand during the holiday rush while maintaining high service standards.
Bradshaw International
Bradshaw International faced challenges with high shipping volumes and inefficient processes due to an outdated WMS. Collaborating with enVista, they integrated a new WMS that streamlined operations and improved inventory management. The system allowed for better SKU profiling and optimized pick/pack operations, resulting in increased shipping capacity without additional labor costs.
Somcan
Somcan, a distributor of consumer products, struggled with outdated processes that hindered efficiency and accuracy. By implementing ProVision WMS, they integrated their warehouse operations with their ERP system, enabling real-time tracking of inventory movements. The new system utilized handheld scanners to streamline order picking and packing processes. As a result, Somcan experienced a significant reduction in order processing time and improved inventory accuracy, leading to increased customer satisfaction and operational efficiency.
Key Benefits of Implementing a WMS
Implementing a Warehouse Management System (WMS) offers numerous advantages that can significantly enhance operational efficiency and reduce costs across the supply chain. A WMS automates and optimizes various warehouse processes, such as inventory tracking, order picking, and shipping, which leads to improved inventory accuracy and reduced errors. By streamlining order fulfillment, businesses can respond more quickly to customer demands, enhancing overall satisfaction.
Additionally, a WMS provides valuable data insights for better decision-making and resource allocation. Ultimately, these improvements not only lower operational costs but also contribute to a more agile and responsive warehouse environment, positioning companies for long-term success in a competitive market.
Here are some key benefits of implementing a WMS:
- Real-Time Inventory Tracking: WMS provides real-time visibility into inventory levels, allowing businesses to monitor stock movements accurately and reduce the risk of stockouts or overstock situations.
- Labor Cost Reduction: By automating manual tasks such as picking and packing, WMS reduces the need for labor-intensive processes, leading to substantial savings in labor costs.
- Improved Order Accuracy: WMS minimizes errors during order fulfillment by ensuring accurate picking and packing, which decreases costs associated with returns and customer dissatisfaction.
- Enhanced Space Utilization: Optimizing storage locations and inventory placement maximizes warehouse space, reducing the need for additional storage facilities and lowering operational costs.
- Reduced Inventory Holding Costs: Better inventory control and demand forecasting enable businesses to maintain optimal stock levels, minimizing excess inventory and associated holding costs.
- Lower Shipping Costs: WMS optimizes shipping processes by consolidating orders and selecting cost-effective carriers, resulting in reduced shipping expenses and improved delivery times.
- Advanced Analytics and Reporting: WMS generates valuable data insights that help businesses make informed decisions about inventory management, labor allocation, and overall operational efficiency.
- Improved Customer Satisfaction: Faster order processing and accurate deliveries lead to higher customer satisfaction rates, fostering loyalty and repeat business.
Conclusion
Implementing a Warehouse Management System (WMS) is a strategic investment that can transform warehouse operations and drive significant business benefits. By automating processes and providing real-time visibility into inventory, a WMS enhances efficiency, accuracy, and customer satisfaction.
The ability to optimize resources and streamline workflows positions organizations to respond effectively to market demands while reducing costs. As businesses continue to evolve, leveraging a WMS will be crucial for maintaining a competitive edge and achieving sustainable growth in an increasingly complex supply chain landscape.
Frequently asked questions
A Warehouse Management System (WMS) is software that automates and optimizes warehouse operations, including inventory tracking, order fulfillment, and shipping, enhancing efficiency and accuracy in logistics management.
Key benefits include improved inventory accuracy, streamlined order fulfillment, reduced labor costs, enhanced space utilization, lower shipping expenses, and increased customer satisfaction through faster and more accurate deliveries.
A WMS provides real-time visibility into inventory levels, automates stock tracking, and optimizes storage locations, reducing errors and ensuring that the right products are available when needed.
Yes, most modern WMS solutions can integrate seamlessly with existing systems such as ERP and TMS, allowing for improved data synchronization and enhanced overall operational efficiency across the supply chain.
Various industries benefit from a WMS, including retail, manufacturing, e-commerce, food and beverage, pharmaceuticals, and logistics. Any business with complex warehousing needs can gain from implementing a WMS.
When choosing a WMS, consider factors such as scalability, ease of integration with existing systems, user-friendliness, feature set tailored to specific needs, vendor support, and total cost of ownership.