Solutions for every business need
Growth comes in all shapes and sizes. Whether it’s smoother operations, sharper insights, higher revenue—or all of the above—we’ve got you covered
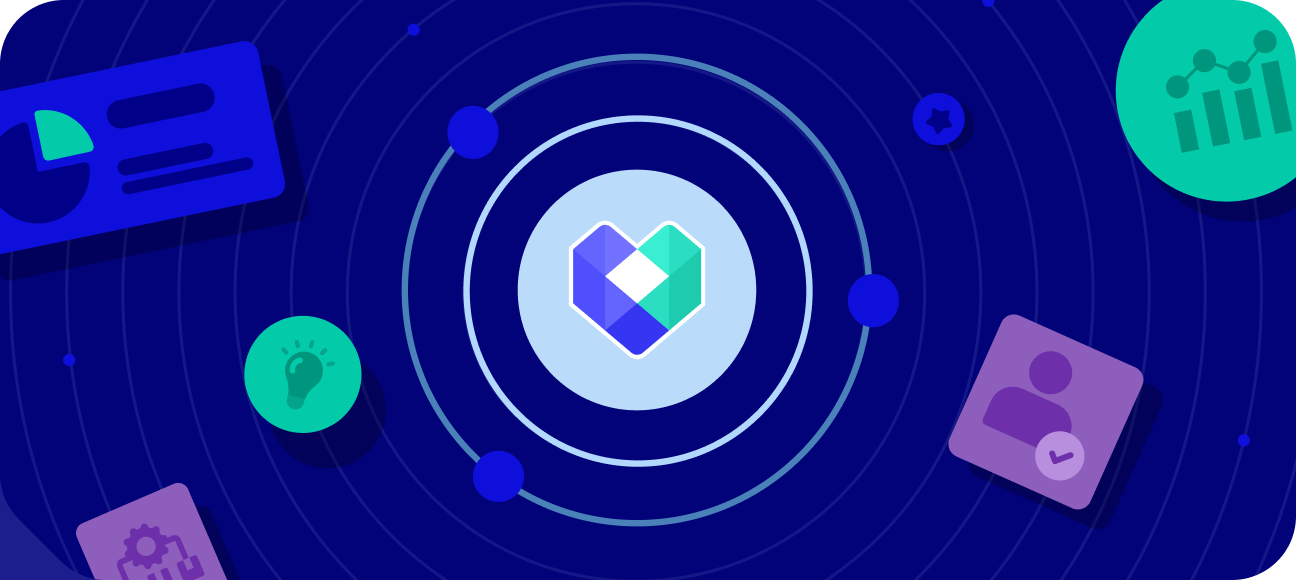
Warehouse management made simple
Gain full control over your inventory with smart automation, real-time tracking, and efficient workflows—ensuring your stock moves smoothly, every time
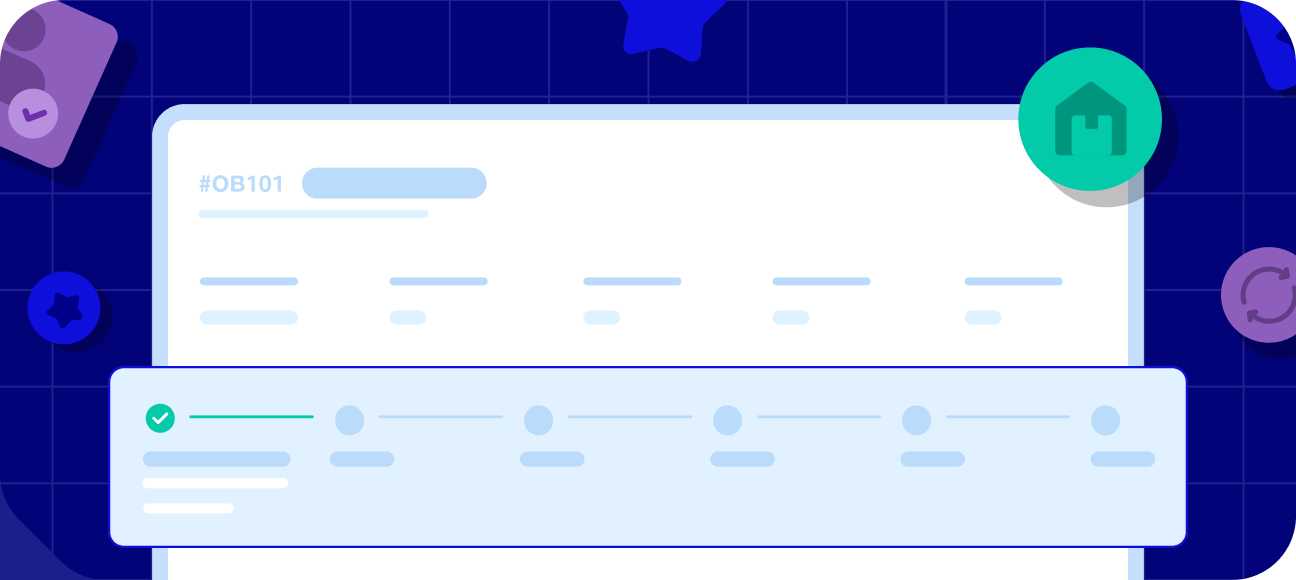
Launch hyperlocal commerce instantly
Set up and scale your hyper-local e-commerce with easy tools for web, orders, and delivery management—bringing you closer to customers, faster
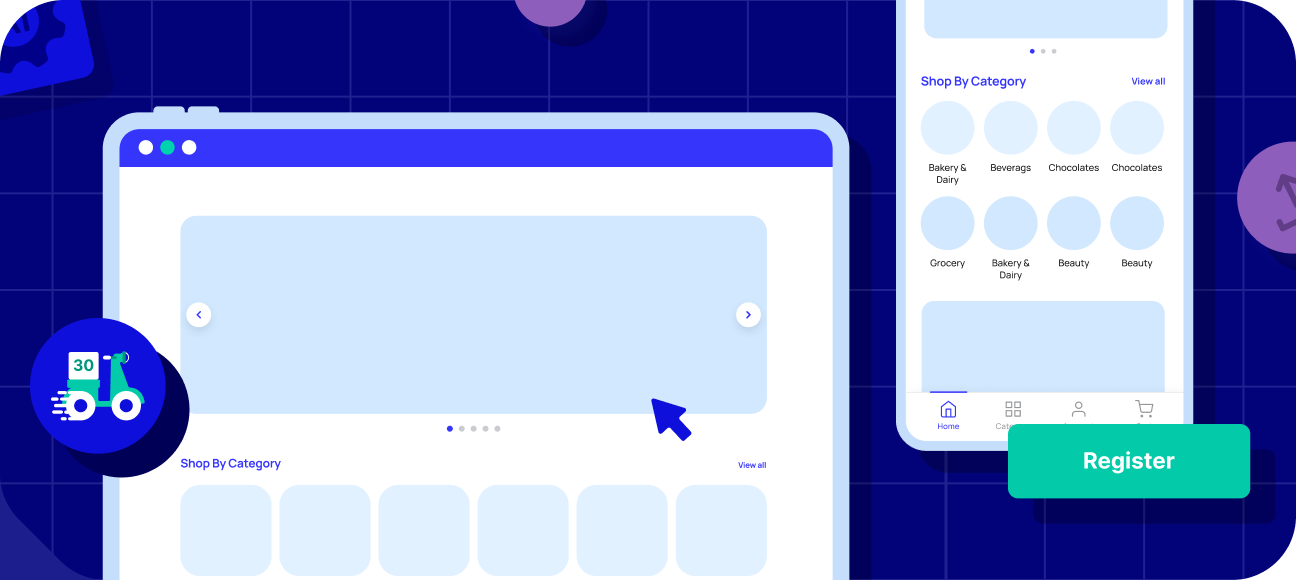
Delivery management made easy
Gain control over your deliveries with real-time visibility, smart automation, and seamless coordination—ensuring on-time arrivals, every time
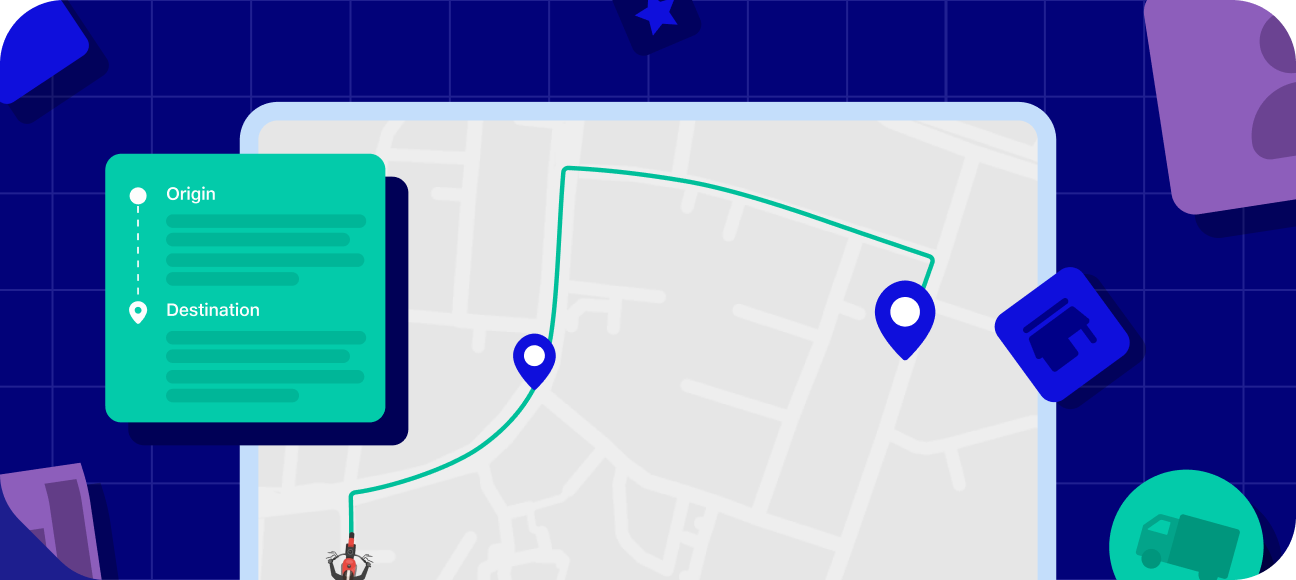
Order management made easy
Master every order with full visibility, smart automation, and effortless control—delivering the right outcomes, every time
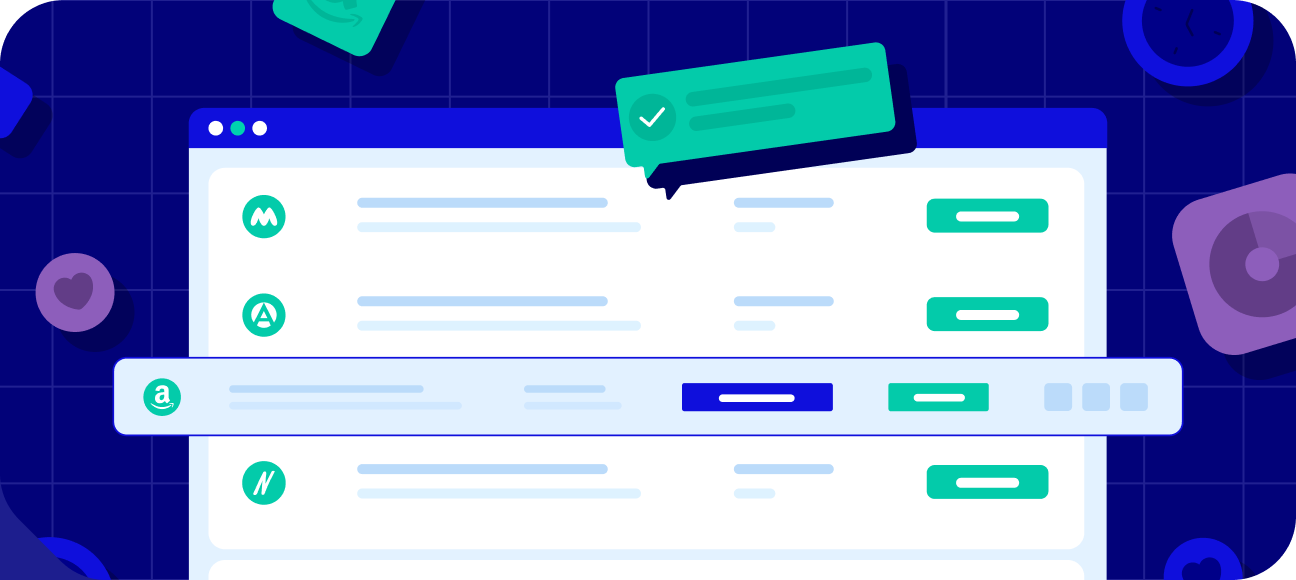
Speak to an expert
Explore how Fynd Commerce can improve every aspect of your business, from online to instore and beyond
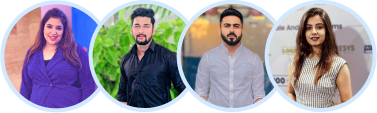
Speak to an expert
Explore how Fynd WMS powers operational excellence with our solution experts
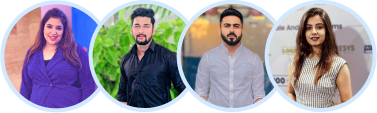
Speak to an expert
Explore how Fynd Quick powers hyperlocal businesses with our solution experts
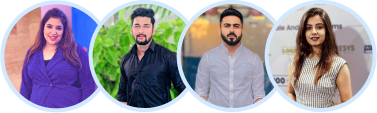
Speak to an expert
Explore how Fynd TMS powers better deliveries with our solution experts
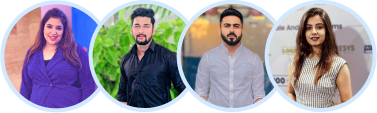
Speak to an expert
Explore how Fynd OMS powers seamless order management with our solution experts
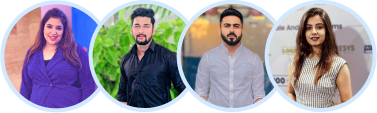
Featured Blog
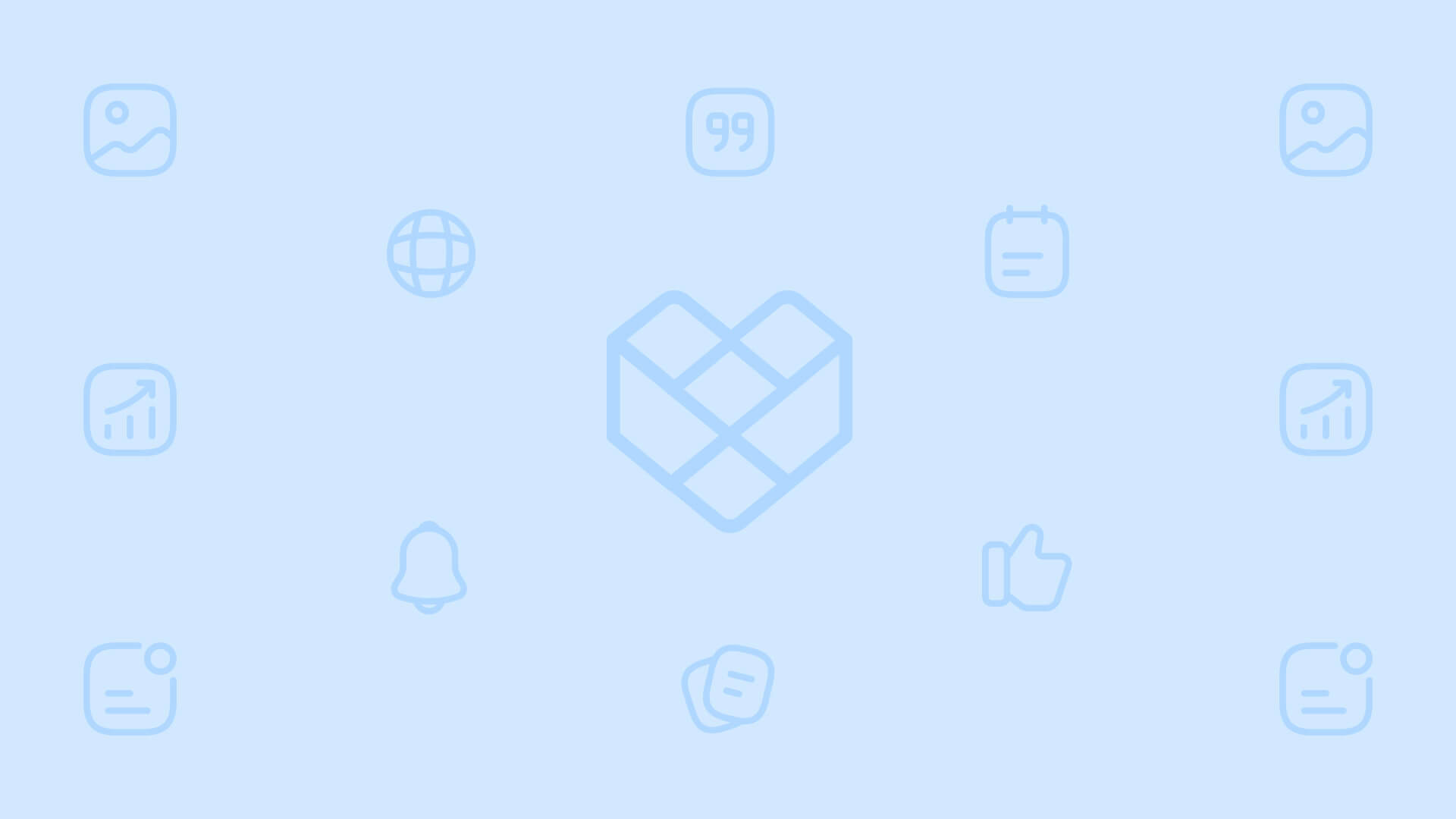
Empower your business, every step of the way
Simplify operations, scale smarter, and deliver better experiences with solutions designed to grow with your business
Take your warehouse management to the next level
Experience hassle-free inventory management with Fynd WMS, designed to keep your operations efficient and accurate. Book a demo to see how Fynd WMS can boost productivity and profits for your business!
Kickstart your quick delivery website
Experience seamless hyper-local commerce with Fynd Quick—engineered to keep things running smoothly and help you reach customers in record time. Book a demo and see how Fynd Quick can drive efficiency and growth for your business!
Level up your delivery management
See how you can manage deliveries with Fynd TMS, designed to streamline operations and keep your customers delighted. Book a demo with our team and find out how Fynd TMS can boost your efficiency and bottom line!
Take your order management to the next level
Discover how effortless order management can be with Fynd OMS, built to keep things running smoothly and make your customers happy. Book a demo with our team and see how Fynd OMS can help boost your efficiency and profits!
Warehouse Management Systems (WMS) are essential tools for optimizing warehouse operations, but understanding their costs is crucial for effective budgeting. The pricing of WMS software varies significantly based on several factors, including the deployment model (cloud vs. on-premise), the size of the business, and specific feature requirements. Generally, cloud-based solutions range from $100 to $500 per user per month, while on-premise systems can incur costs from $2,500 to $200,000 depending on the facility's needs and complexity.
The total cost of ownership for a WMS includes not only the initial purchase or subscription fees but also ongoing expenses such as implementation, training, and maintenance. Initial setup costs can vary widely; for example, an implementation may cost between $3,500 and $40,000, influenced by integration needs and customization. Additionally, businesses should account for hidden costs like staff training and potential upgrades to existing infrastructure to support the new system effectively.
Finally, businesses must evaluate the return on investment (ROI) associated with implementing a WMS. While upfront costs may seem high, a well-implemented WMS can lead to significant savings by improving operational efficiency and reducing errors in inventory management. Thus, careful consideration of both direct and indirect costs is essential for maximizing the benefits of a WMS investment.
What is WMS Software?
A Warehouse Management System (WMS) is specialized software designed to oversee and optimize warehouse operations. It manages the flow of goods from the moment they enter a warehouse until they are shipped out, providing real-time visibility into inventory levels and locations. WMS software enhances efficiency by automating processes such as receiving, storage, picking, packing, and shipping, ultimately streamlining operations across the supply chain.
There are various types of WMS solutions, including standalone systems, integrated modules within Enterprise Resource Planning (ERP) systems, and cloud-based options. Each type caters to different business needs and scales, ensuring that companies can effectively manage their inventory and fulfill orders efficiently while minimizing costs and errors.
Two Types of WMS Software Platforms
Warehouse Management System (WMS) software is essential for improving warehouse operations by automating inventory management, order fulfillment, and logistics. There are two primary types of WMS platforms: cloud-based and on-premises. Cloud-based WMS offers flexibility, reduced upfront costs, and easy scalability, making it ideal for businesses seeking quick deployment. In contrast, on-premises WMS provides greater control and customization, suitable for larger enterprises with specific needs.
Each type presents unique advantages and considerations that can significantly impact operational efficiency and overall cost-effectiveness, helping businesses make informed decisions about their warehouse management solutions.
1. Cloud-Based WMS
Cloud-based WMS solutions utilize Software as a Service (SaaS) models, allowing users to access the system over the Internet. This platform eliminates the need for local hardware and IT management, reducing upfront costs and enabling quick scalability. Businesses benefit from automatic updates, remote access, and easier integration with other systems. However, long-term subscription costs may accumulate, making it essential to evaluate overall expenses against operational benefits.
2. On-Premises WMS
On-premises WMS involves hosting the software and hardware on-site, giving organizations complete control over their systems. This type is often preferred by larger enterprises needing highly customized solutions tailored to specific industry requirements. While it allows for greater data security and compliance, it typically incurs higher initial costs for installation and maintenance. Additionally, ongoing IT support is necessary for updates and troubleshooting, which can strain resources in smaller organizations.
What Features are Included in the Cost of a WMS?
The cost of a Warehouse Management System (WMS) typically encompasses various essential features that significantly enhance operational efficiency. These features are crucial for effectively managing inventory, streamlining processes, and improving overall productivity within the warehouse. A comprehensive WMS not only automates routine tasks but also provides real-time data visibility, which is vital for informed decision-making.
Understanding what is included in the cost—such as inventory tracking, order fulfillment, and reporting capabilities—can help businesses assess their specific needs and budget accordingly. This knowledge empowers organizations to select a WMS that aligns with their operational goals and maximizes return on investment.
- Inventory Tracking and Control: Real-time visibility of stock levels and locations ensures accurate inventory management and minimizes discrepancies.
- Order Fulfillment: Manages the entire order process from receipt to shipment, enhancing accuracy and speed in fulfilling customer orders.
- Receiving and Put-Away: Streamlines the intake of goods, directing items to optimal storage locations based on predefined rules.
- Labor Management: Monitors workforce performance, schedules tasks, and optimizes employee utilization to improve productivity.
- Reporting and Analytics: Generate insights into warehouse performance through various reports, aiding in strategic decision-making.
- Barcode and RFID Integration: Facilitates precise inventory tracking and data capture, improving efficiency in warehouse operations.
- Multi-Warehouse Management: Enables centralized control over multiple locations, optimizing inventory levels across all warehouses.
Calculating WMS installation costs
Calculating the installation costs for a Warehouse Management System (WMS) requires careful consideration of several factors that can greatly impact overall expenses. Businesses must evaluate the type of deployment—whether on-premise or cloud-based—alongside additional costs related to customization, training, and ongoing support. Each of these elements plays a vital role in determining the total investment needed.
A thorough understanding of these components is essential for effective budgeting, ensuring that the selected WMS aligns with operational requirements while remaining within financial limits. This approach helps organizations maximize their return on investment and streamline warehouse operations efficiently.
1. Initial Setup Costs
Initial setup costs encompass the expenses incurred during the installation of a WMS. For on-premise systems, businesses can expect to pay between $2,000 and $10,000 for installation and customization, depending on the system's complexity and features. Cloud-based solutions typically have lower initial costs, averaging around $1,000 to $7,000 for setup and configuration.
2. Licensing Fees
Licensing fees represent a significant portion of WMS costs. On-premise licenses start at approximately $2,500 per facility, while enterprise-level systems can exceed $200,000. In contrast, cloud-based subscriptions generally range from $100 to $500 per user per month, with total costs influenced by the number of users and required features.
3. Training Expenses
Training is essential for successful WMS implementation. Companies should budget for training costs that can vary widely based on the system's complexity and the number of employees involved. Initial training sessions may cost anywhere from $1,000 to $5,000, ensuring staff are adequately prepared to utilize the new system effectively.
4. Ongoing Support and Maintenance
Ongoing support and maintenance are critical for sustaining WMS functionality. Annual maintenance fees typically range from 10% to 20% of the initial license cost for on-premise systems. For cloud-based solutions, support is often included in subscription fees, but businesses should still anticipate additional costs for upgrades and technical assistance over time.
5. Hardware Requirements
Hardware requirements are a critical aspect of WMS installation costs. On-premise systems often necessitate significant investment in servers, networking equipment, and other infrastructure, which can range from $5,000 to $50,000 depending on the scale of operations. For cloud-based solutions, hardware costs are typically lower since the service provider manages the infrastructure. However, businesses may still need to invest in devices like barcode scanners and mobile computers, which can add $1,000 to $10,000 to the overall budget.
6. Customization Costs
Customization costs can vary widely based on the specific needs of a business. Many WMS solutions offer standard features, but tailoring the system to fit unique workflows may require additional investment. Customization can range from $5,000 to over $50,000, depending on complexity and vendor pricing. It's essential for businesses to clearly define their requirements upfront to avoid unexpected expenses during implementation.
7. Integration Expenses
Integration expenses involve connecting the WMS with existing systems such as ERP or inventory management software. This process is crucial for ensuring seamless data flow and operational efficiency. Integration costs can range from $3,000 to $30,000 based on the number of systems involved and the complexity of the integration. Proper planning and collaboration with IT teams can help mitigate these costs and streamline the integration process.
Hidden Costs To Plan For In Your Budget
Calculating hidden costs in your budget is essential for effective financial planning, especially when implementing a new system like a Warehouse Management System (WMS). Often, businesses focus on visible expenses but overlook additional costs that can accumulate over time. Understanding these hidden costs helps prevent budget overruns and ensures that the total investment aligns with operational goals. By planning for these expenses, organizations can maintain financial stability and make informed decisions regarding their WMS implementation. Here are the pointers:
1. Hidden Licensing Fees
Hidden licensing fees can significantly impact your budget. These fees often arise from additional users, devices, or modules not included in the initial contract. Businesses should thoroughly review the licensing structure to identify any potential extra charges. Failing to account for these fees can lead to unexpected financial strain as the system scales or additional functionality is required.
2. Consultancy and Advisory Costs
Consultancy and advisory costs are another hidden expense that can catch businesses off guard. Engaging external consultants for optimization or troubleshooting can add significant costs to the budget. While these services may be necessary for effective implementation, estimating their total cost upfront can be challenging. Organizations should factor in potential consultancy fees when planning their WMS budget to avoid surprises.
3. Hidden Infrastructure Costs
Hidden infrastructure costs often arise during WMS implementation, particularly for on-premise systems. Upgrading servers, networking equipment, or other hardware may be necessary to support the new system. These costs can accumulate quickly and should be carefully assessed during the budgeting process. Businesses must evaluate their existing infrastructure to determine if upgrades are needed and how much they will contribute to overall expenses.
4. Training and Change Management Costs
Training and change management costs are often underestimated in WMS budgets. While initial training sessions may be included in the software package, ongoing training for new employees or system updates can incur additional expenses. Moreover, change management initiatives to facilitate smooth transitions and minimize resistance may require extra resources. Organizations should allocate a budget for continuous training and support to ensure long-term success with the WMS.
5. Data Migration Expenses
Data migration expenses can be a hidden cost when implementing a WMS. Transferring existing data from legacy systems to the new platform often requires specialized tools or services, which can add up quickly. The complexity of the data being migrated also influences costs, as more intricate datasets may necessitate additional time and expertise. Businesses should plan for these expenses to ensure a smooth transition without data loss.
6. Ongoing Maintenance and Support Fees
Ongoing maintenance and support fees are crucial hidden costs that can impact long-term budgeting. While initial setup costs may seem manageable, annual maintenance fees typically range from 10% to 20% of the total software cost. Additionally, businesses might incur charges for technical support, software updates, and troubleshooting services. It’s essential to factor these recurring expenses into the overall budget for sustainable operations.
7. Opportunity Costs
Opportunity costs represent a less tangible but significant hidden expense associated with WMS implementation. These costs arise from potential revenue lost during the transition period when operations may be disrupted or slowed down due to training and system adjustments. Businesses should consider the impact on productivity and customer service during implementation, as these factors can affect overall profitability in the long run.
Reasons Why Companies Use WMS Systems
Companies utilize Warehouse Management Systems (WMS) to enhance operational efficiency and improve inventory management. By automating warehouse processes, WMS reduces errors in picking and shipping, streamlining operations from receiving to delivery. This leads to faster turnaround times and better resource allocation, ultimately increasing productivity.
WMS systems automate and streamline warehouse processes, leading to smoother operations and the ability to handle higher volumes of inventory. These systems provide real-time insights into inventory levels, allowing businesses to make informed decisions regarding stock management and demand forecasting. With accurate order fulfillment and timely deliveries, WMS improves customer satisfaction and loyalty, positively impacting the company's reputation and bottom line.
Bringing your WMS Budget Together
Bringing your Warehouse Management System (WMS) budget together necessitates a thorough examination of various cost components to create a comprehensive financial plan. Businesses must assess both upfront and ongoing expenses tied to WMS implementation, which can vary widely based on deployment type, features, and operational scale.
By gaining a clear understanding of these costs, organizations can make informed decisions that align with their budgetary constraints and operational requirements. This strategic approach ultimately paves the way for a successful WMS deployment, ensuring that the system effectively meets the needs of the business while optimizing efficiency and productivity.
1. Subscription Fees
Subscription fees are a primary component of WMS budgets, particularly for cloud-based solutions. These fees typically range from $100 to $500 per user per month, depending on the complexity of the system and the number of users. Organizations should assess their anticipated usage and select a subscription model that aligns with their operational requirements while considering potential scalability as their business grows.
2. Software Licensing Fees
For on-premise WMS solutions, software licensing fees represent a significant upfront cost. These fees can range from $2,500 to over $200,000 per facility based on the system's capabilities and the size of the organization. Businesses must evaluate their specific needs and budget accordingly to avoid unexpected expenses during implementation.
3. Implementation Costs
Implementation costs encompass setup, installation, configuration, and initial training for the WMS. These costs can vary widely, typically ranging from $1,000 to $10,000 for cloud-based systems and $3,500 to $40,000 for on-premise solutions. Proper budgeting for these expenses is essential to ensure a smooth transition to the new system and minimize operational disruptions.
4. Ongoing Maintenance and Support Fees
Ongoing maintenance and support fees are crucial for sustaining WMS functionality over time. For cloud-based systems, these costs are often included in the subscription fee; however, businesses should anticipate additional charges for premium support. For on-premise solutions, annual maintenance typically ranges from 10% to 20% of the initial license cost. Planning for these recurring expenses is vital for long-term budgeting.
Conclusion
Understanding the costs associated with a Warehouse Management System (WMS) is essential for effective financial planning and ensuring a successful implementation. The expenses typically include initial setup fees, which cover software licensing, hardware, and employee training. Ongoing maintenance costs also play a significant role, encompassing software updates, technical support, and system enhancements. Moreover, hidden expenses, such as integration with existing systems and potential downtime during deployment, can add to the overall cost. By thoroughly evaluating these aspects, organizations can create a realistic budget that aligns with their operational goals and ensures long-term efficiency in warehouse management.
Frequently asked questions
A Warehouse Management System (WMS) is software designed to optimize warehouse operations by managing inventory, tracking stock levels, and streamlining processes such as receiving, picking, and shipping.
The cost of a Warehouse Management System can vary widely based on factors such as deployment type (cloud vs. on-premise), features, and the size of the organization. On-premise systems may range from $2,500 to over $200,000 in licensing fees, while cloud-based solutions typically charge between $100 to $500 per user per month.
Using a WMS offers numerous benefits, including improved inventory accuracy, enhanced operational efficiency, and better order fulfillment. It provides real-time visibility into stock levels, enabling informed decision-making and reducing excess inventory.
The time required to implement a Warehouse Management System varies based on factors such as system complexity, organizational size, and the level of customization needed. Generally, implementation can take anywhere from a few weeks to several months.
When selecting a WMS, consider factors such as your specific operational needs, budget constraints, scalability, and integration capabilities with existing systems. Evaluate the features offered by different solutions—such as real-time inventory tracking, reporting tools, and user-friendliness.
Yes, most modern Warehouse Management Systems are designed to integrate seamlessly with other business systems, such as Enterprise Resource Planning (ERP), Transportation Management Systems (TMS), and e-commerce platforms.