Solutions for every business need
Growth comes in all shapes and sizes. Whether it’s smoother operations, sharper insights, higher revenue—or all of the above—we’ve got you covered
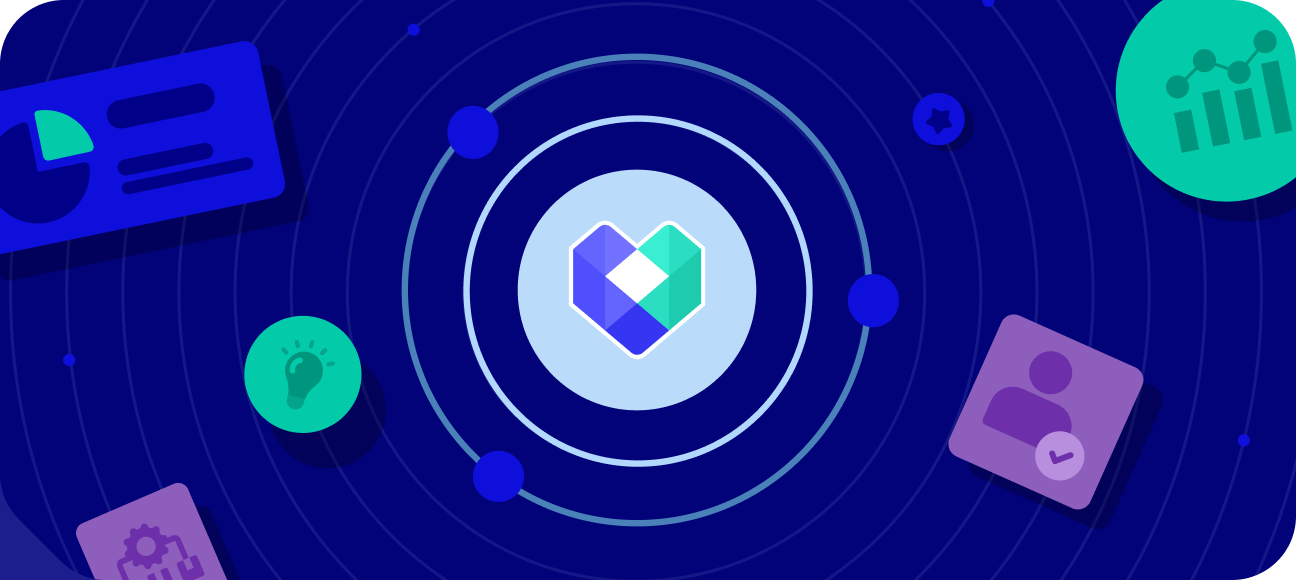
Warehouse management made simple
Gain full control over your inventory with smart automation, real-time tracking, and efficient workflows—ensuring your stock moves smoothly, every time
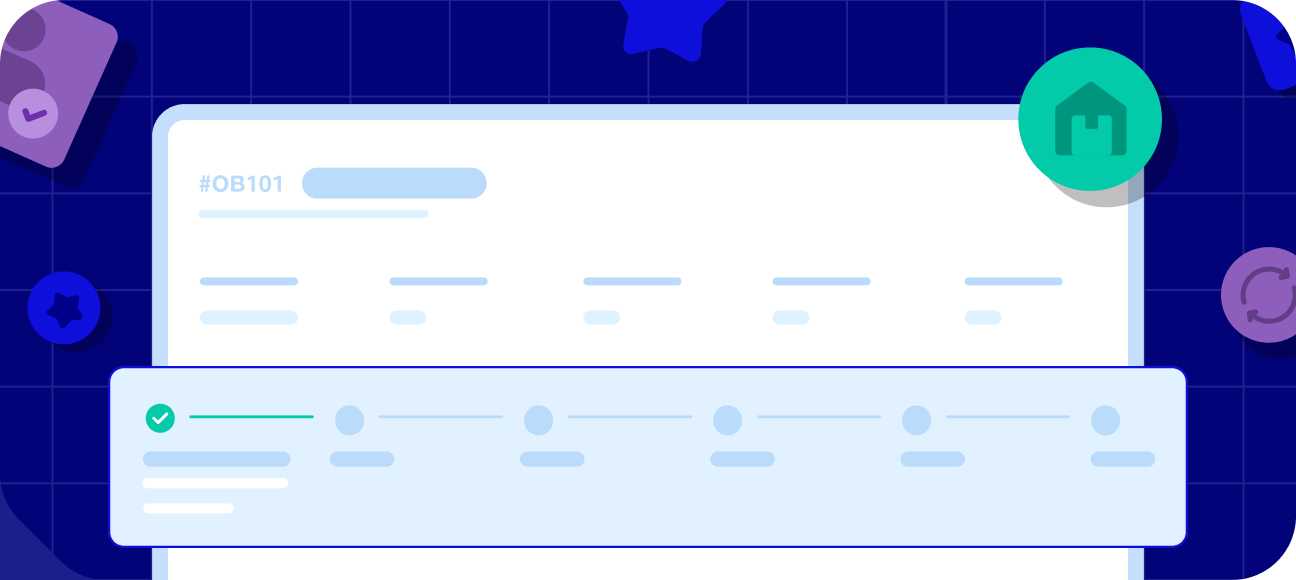
Launch hyperlocal commerce instantly
Set up and scale your hyper-local e-commerce with easy tools for web, orders, and delivery management—bringing you closer to customers, faster
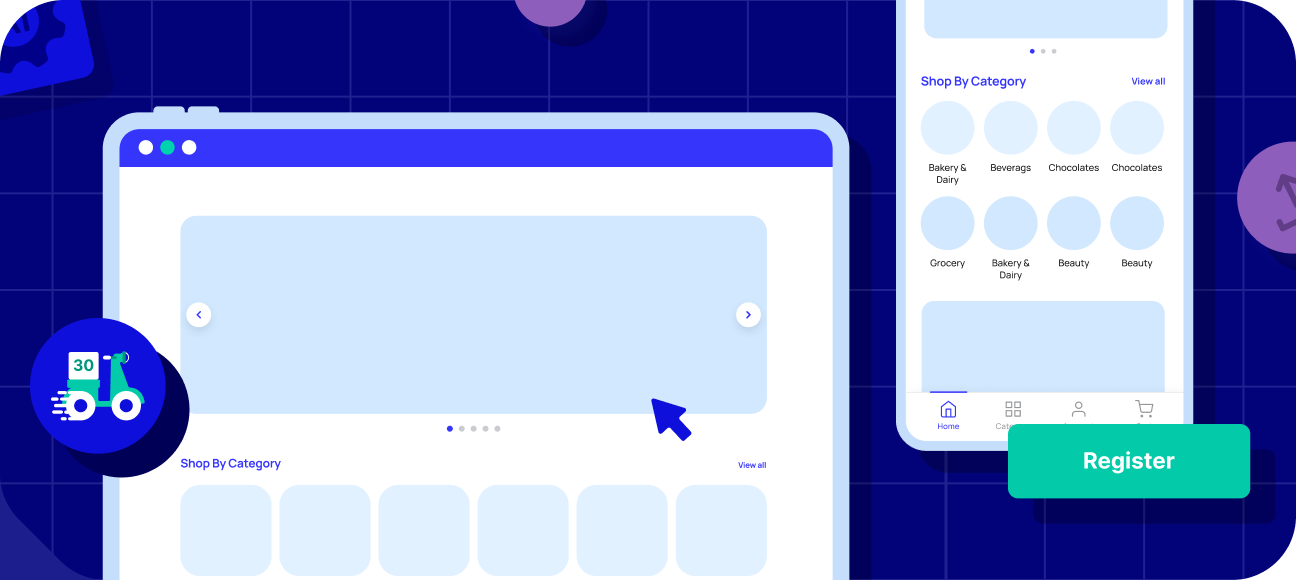
Delivery management made easy
Gain control over your deliveries with real-time visibility, smart automation, and seamless coordination—ensuring on-time arrivals, every time
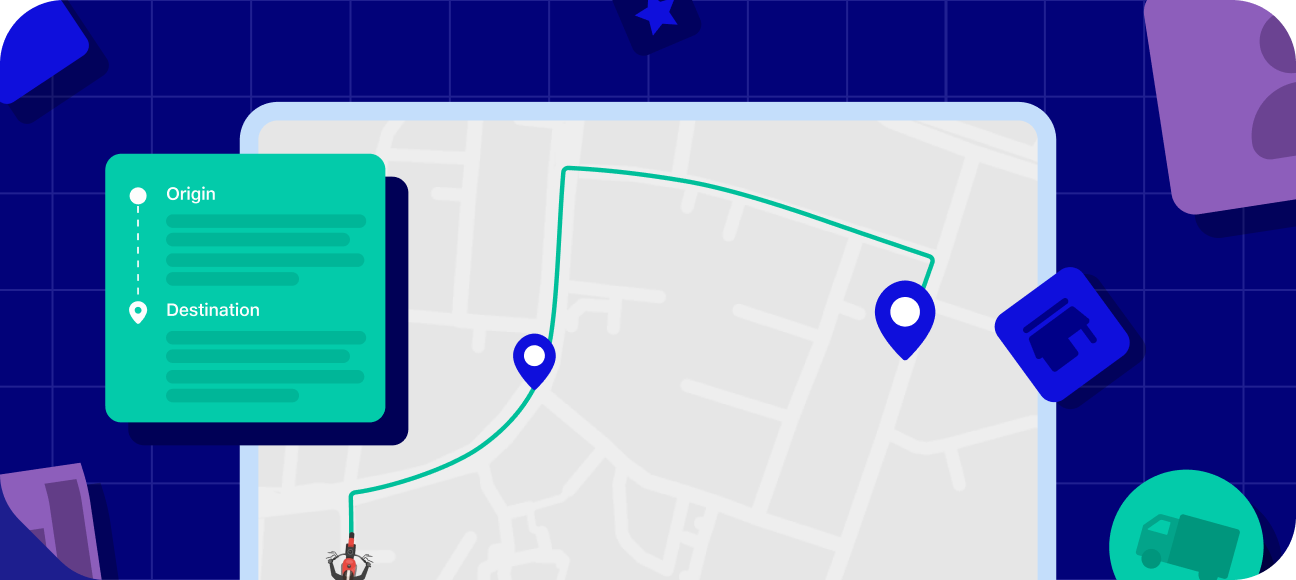
Order management made easy
Master every order with full visibility, smart automation, and effortless control—delivering the right outcomes, every time
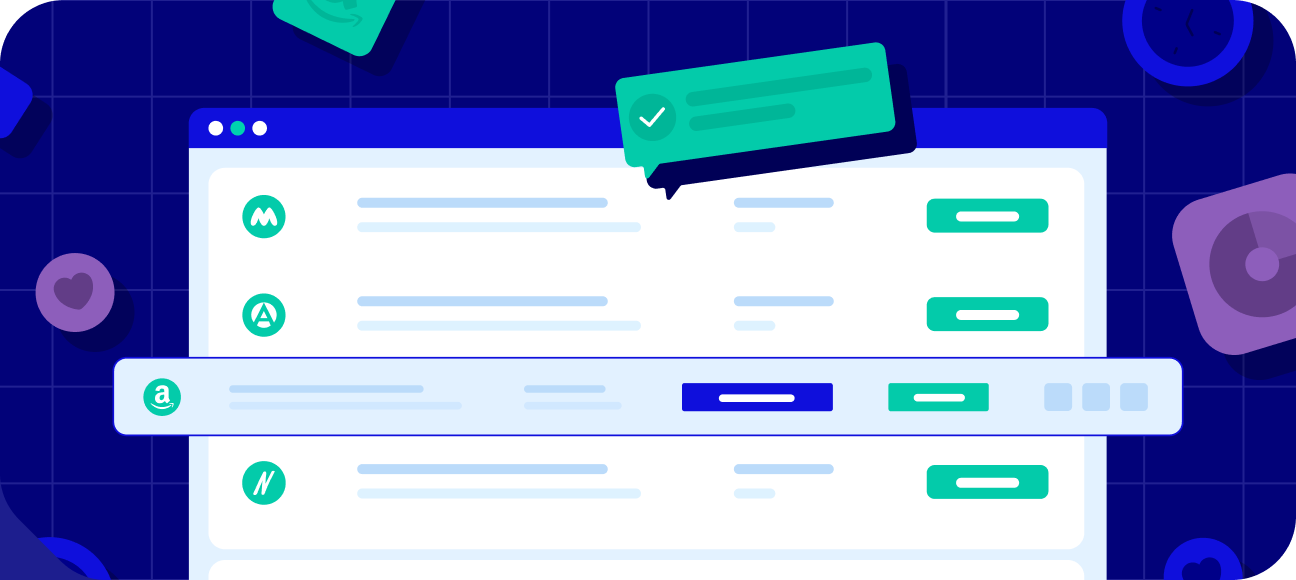
Speak to an expert
Explore how Fynd Commerce can improve every aspect of your business, from online to instore and beyond
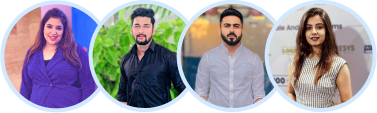
Speak to an expert
Explore how Fynd WMS powers operational excellence with our solution experts
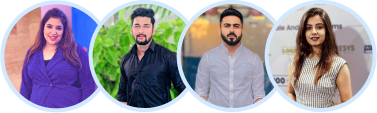
Speak to an expert
Explore how Fynd Quick powers hyperlocal businesses with our solution experts
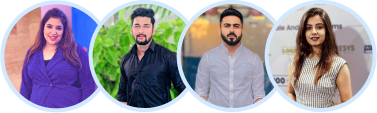
Speak to an expert
Explore how Fynd TMS powers better deliveries with our solution experts
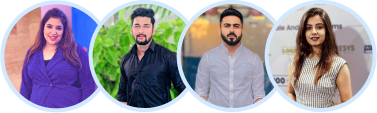
Speak to an expert
Explore how Fynd OMS powers seamless order management with our solution experts
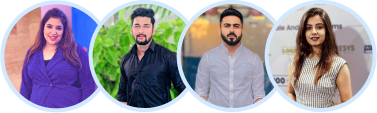
Featured Blog
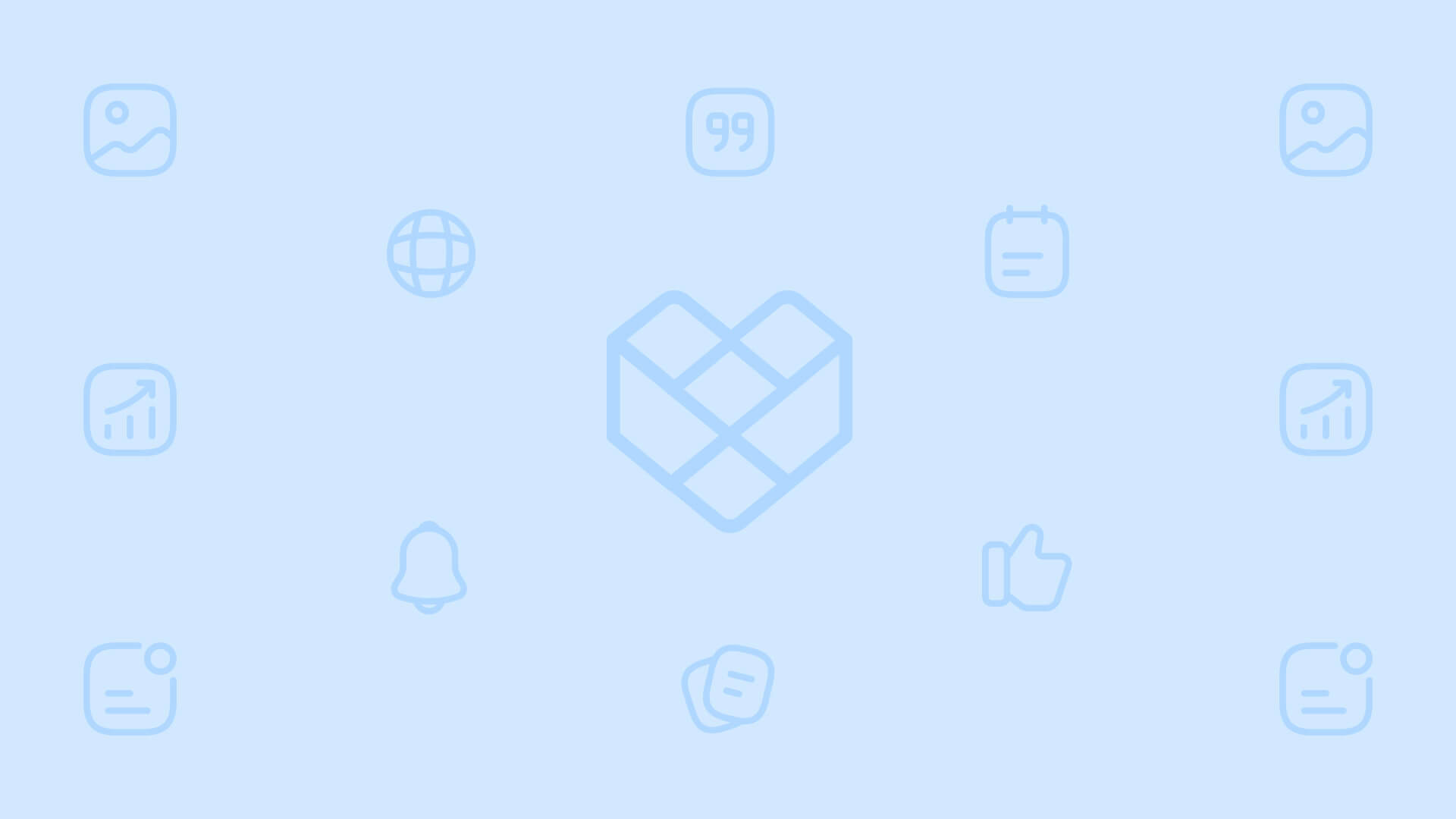
Empower your business, every step of the way
Simplify operations, scale smarter, and deliver better experiences with solutions designed to grow with your business
Take your warehouse management to the next level
Experience hassle-free inventory management with Fynd WMS, designed to keep your operations efficient and accurate. Book a demo to see how Fynd WMS can boost productivity and profits for your business!
Kickstart your quick delivery website
Experience seamless hyper-local commerce with Fynd Quick—engineered to keep things running smoothly and help you reach customers in record time. Book a demo and see how Fynd Quick can drive efficiency and growth for your business!
Level up your delivery management
See how you can manage deliveries with Fynd TMS, designed to streamline operations and keep your customers delighted. Book a demo with our team and find out how Fynd TMS can boost your efficiency and bottom line!
Take your order management to the next level
Discover how effortless order management can be with Fynd OMS, built to keep things running smoothly and make your customers happy. Book a demo with our team and see how Fynd OMS can help boost your efficiency and profits!
Warehouse Management Systems (WMS) are essential software applications that facilitate the efficient management of warehouse operations. They oversee processes from the moment goods arrive at a distribution center until they are dispatched. A WMS provides real-time visibility into inventory levels, enabling organizations to optimize storage, track inventory, and streamline order fulfillment.
The functionality of a WMS encompasses several key operations: receiving, put-away, picking, packing, and shipping. Each of these processes is designed to maximize efficiency and minimize errors. For instance, during the receiving phase, a WMS can automatically validate and reconcile incoming goods against purchase orders using scanning technologies. This automation not only speeds up the process but also ensures that inventory records are accurate from the outset. Furthermore, the system aids in optimizing picking routes and packing strategies to enhance overall productivity.
In addition to operational efficiency, a WMS supports strategic decision-making through data analytics. Businesses can proactively adjust their stock levels by providing insights into inventory turnover rates and demand forecasting. This capability is vital for maintaining customer satisfaction by ensuring that products are available when needed. The role of WMS in supporting agile and responsive warehouse operations becomes increasingly significant.
What is warehouse management?
Warehouse management refers to the systematic control and oversight of various operations within a warehouse. This includes managing inventory, storage, picking, packing, and shipping processes. The primary objective is to ensure that products are stored efficiently and can be retrieved quickly, thereby minimizing costs and maximizing operational efficiency throughout the supply chain.
Key functions of warehouse management encompass several critical processes. The workflow typically begins with receiving goods, followed by their storage in designated locations. Once orders are placed, the picking process retrieves items from storage, which are then packed for shipment. Each step must be optimized to reduce time and labor costs while ensuring accuracy in inventory records. Effective warehouse management relies on technology and best practices to streamline these operations.
What is a warehouse management system?
A Warehouse Management System (WMS) is a software application designed to support and optimize warehouse operations. It manages the movement and storage of inventory, ensuring that products are efficiently tracked from the moment they enter a warehouse until they are shipped out. A WMS can operate as standalone software or be integrated into broader enterprise resource planning (ERP) systems to provide a comprehensive solution for managing supply chain activities.
The core functions of a WMS include inventory management, order processing, picking, packing, and shipping. By utilizing technologies such as barcode scanning and RFID, a WMS offers real-time visibility into inventory levels, enabling businesses to streamline their processes and reduce errors.
Inventory Management vs Warehouse Management
Inventory management and warehouse management are crucial components of supply chain operations, each serving distinct yet interconnected purposes. Inventory management focuses on overseeing the quantity, location, and movement of goods throughout the entire supply chain, ensuring that stock levels meet customer demand efficiently while minimizing costs. In contrast, warehouse management is concerned with the physical storage, organization, and handling of inventory within a warehouse facility, facilitating streamlined operations for picking, packing, and shipping.
The key differences between the two lie in their focus and scope. Inventory management provides a high-level overview of stock levels across all locations, including forecasting demand and managing reorder points. It involves tracking overall inventory status to optimize stock levels for fulfilling customer orders.
Key Components of a Warehouse Management System
A Warehouse Management System (WMS) consists of several key components that work together to streamline warehouse operations. Inventory management is a core feature, providing real-time tracking of inventory levels and locations within the warehouse. This component ensures accurate stock management by logging the movement of goods, enabling organizations to maintain optimal inventory levels and reduce stock discrepancies.
Another essential component is order management, which allows warehouses to manage orders efficiently from various sources, such as online platforms and manual inputs. A WMS automates the order processing workflow, from order entry to fulfillment, ensuring that orders are accurately tracked and managed throughout their lifecycle. This centralization enhances operational efficiency and improves customer service by providing timely updates on order statuses.
The Process Flow in Warehouse Management
The process flow in warehouse management is essential for ensuring that goods are handled efficiently from arrival to dispatch. This flow encompasses several key stages, including receiving, put-away, inventory management, order fulfillment, and shipping. Each stage contributes significantly to the overall effectiveness of warehouse operations.
Understanding and optimizing this flow allows organizations to streamline processes, reduce operational costs, and enhance customer satisfaction. By focusing on each stage—such as inspecting incoming goods during receiving, efficiently storing items during put-away, and accurately fulfilling orders—businesses can manage inventory effectively and respond quickly to customer demands.
1. Receiving
The receiving process is the first step in warehouse management, where incoming goods are checked against purchase orders. This stage involves inspecting items for quality and quantity while documenting any discrepancies. Accurate receiving is vital as it sets the foundation for inventory accuracy and ensures that products are correctly logged into the system, preventing future issues in stock management.
2. Put-away
Once items are received, they move to the put-away process, where they are stored in designated locations within the warehouse. This stage focuses on optimizing storage space and organizing products for easy access. Efficient put-away practices help minimize retrieval times during order fulfillment, ensuring that items are stored logically based on demand and frequency of use.
3. Order Fulfillment
Order fulfillment encompasses picking and packing processes essential for preparing goods for shipment. In this stage, items are selected based on customer orders and packed securely for delivery. Accuracy is critical during picking to prevent errors that can lead to customer dissatisfaction. Streamlined order fulfillment processes ensure timely deliveries while maintaining high accuracy levels, ultimately enhancing customer service and operational efficiency.
Benefits of Implementing a WMS
Implementing a Warehouse Management System (WMS) can significantly enhance operational efficiency and accuracy within a warehouse. By automating various processes and providing real-time visibility into inventory levels, WMS solutions streamline operations from receiving to shipping. This leads to faster order fulfillment, reduced costs, and improved customer satisfaction.
As businesses increasingly rely on efficient logistics to stay competitive, understanding the benefits of WMS becomes crucial for optimizing warehouse management. With the right WMS in place, companies can transform their warehouse operations, adapting to market demands while maintaining high service levels.
1. Improved Inventory Accuracy
A WMS enhances inventory accuracy by automating tracking and management processes. Real-time updates on stock levels help prevent overstocking or stockouts, ensuring that businesses maintain optimal inventory levels. This accuracy minimizes errors in order fulfillment, leading to higher customer satisfaction as products are delivered correctly and on time.
2. Increased Operational Efficiency
By automating routine tasks such as order processing and picking, a WMS significantly boosts operational efficiency. Employees can focus on more value-added activities instead of manual data entry or inventory checks. Streamlined workflows reduce the time required for each task, enabling warehouses to operate at a faster pace while maintaining high standards of accuracy.
3. Enhanced Order Fulfillment Speed
WMS solutions optimize picking routes and streamline packing processes, resulting in faster order fulfillment. By analyzing data on product locations and order patterns, the system can guide workers efficiently through the warehouse. This speed not only improves operational throughput but also enhances customer satisfaction by ensuring timely deliveries.
4. Cost Reduction
Implementing a WMS can lead to substantial cost savings for businesses. By reducing manual labor through automation and minimizing errors that require costly corrections, companies can lower their operational expenses. Additionally, better inventory management reduces excess stock and storage costs, further enhancing profitability.
5. Better Data-Driven Decision Making
A WMS provides robust reporting and analytics capabilities that enable informed decision-making. Businesses can track key performance indicators (KPIs) such as order accuracy and lead times, allowing them to identify areas for improvement. This data-driven approach helps managers optimize operations continuously and adapt strategies to meet changing market demands effectively.
Challenges in Warehouse Management Systems Implementation
Implementing a Warehouse Management System (WMS) presents several challenges that organizations must navigate to ensure a successful transition. One of the foremost challenges is selecting the right system and vendor. With numerous WMS options available, businesses must identify a solution that aligns with their unique operational requirements. This process can be complicated, as it involves evaluating features, costs, and vendor reliability, which can lead to misalignment between expectations and actual capabilities.
Data accuracy and processing are also significant hurdles during WMS implementation. A modern WMS requires accurate data to function effectively; any discrepancies can lead to operational inefficiencies.
Tips for improving your warehouse management
Effective warehouse management is crucial for optimizing operations, reducing costs, and enhancing customer satisfaction. With the growing demands of e-commerce and supply chain complexities, improving warehouse management practices can lead to significant gains in efficiency and productivity.
By implementing strategic changes and leveraging technology, businesses can streamline their processes and create a more organized and responsive warehouse environment. Here are some practical tips for improving your warehouse management:
- Implement a Warehouse Management System (WMS): A robust WMS automates inventory tracking and order processing, providing real-time visibility into stock levels.
- Optimize Warehouse Layout: Strategically planning your warehouse layout can significantly enhance efficiency.
- Invest in Automation Technologies: Incorporating automation tools such as conveyor systems, robotic pickers, and automated storage solutions and increase accuracy.
- Train Employees Regularly: Ongoing training is essential for ensuring that staff are familiar with the latest technologies and best practices.
- Conduct Regular Audits: Regular audits help identify inefficiencies within your warehouse operations.
Conclusion
Implementing a Warehouse Management System (WMS) offers numerous advantages that significantly enhance operational efficiency and accuracy. A well-executed WMS streamlines various processes, from inventory management to order fulfillment, ultimately leading to faster turnaround times and reduced errors. By automating tasks and providing real-time visibility into inventory levels, businesses can make informed decisions that drive productivity and improve customer satisfaction.
Frequently asked questions
A WMS is software designed to optimize warehouse operations by managing inventory, tracking stock, and streamlining order fulfillment. It automates processes like receiving, picking, packing, and shipping, improving accuracy, efficiency, and customer satisfaction through timely deliveries.
WMS provides real-time tracking using barcode scanning and RFID, minimizing human errors. This allows businesses to maintain accurate stock levels, quickly spot discrepancies, and reliably fulfill orders.
Look for order management, reporting tools, integration, scalability, and user-friendly interfaces. Automated picking, real-time analytics, and customizable workflows also improve efficiency.
WMS automates picking and packing, optimizing routes and processes to reduce time, increase accuracy, and speed up delivery, resulting in higher customer satisfaction.
Challenges include data migration, employee resistance, and training needs. Proper planning, testing, and support can ensure a smooth transition and successful adoption.
Yes, many WMS solutions are scalable and affordable, offering small businesses improved inventory management, order accuracy, and productivity, helping them compete effectively.