Solutions for every business need
Growth comes in all shapes and sizes. Whether it’s smoother operations, sharper insights, higher revenue—or all of the above—we’ve got you covered
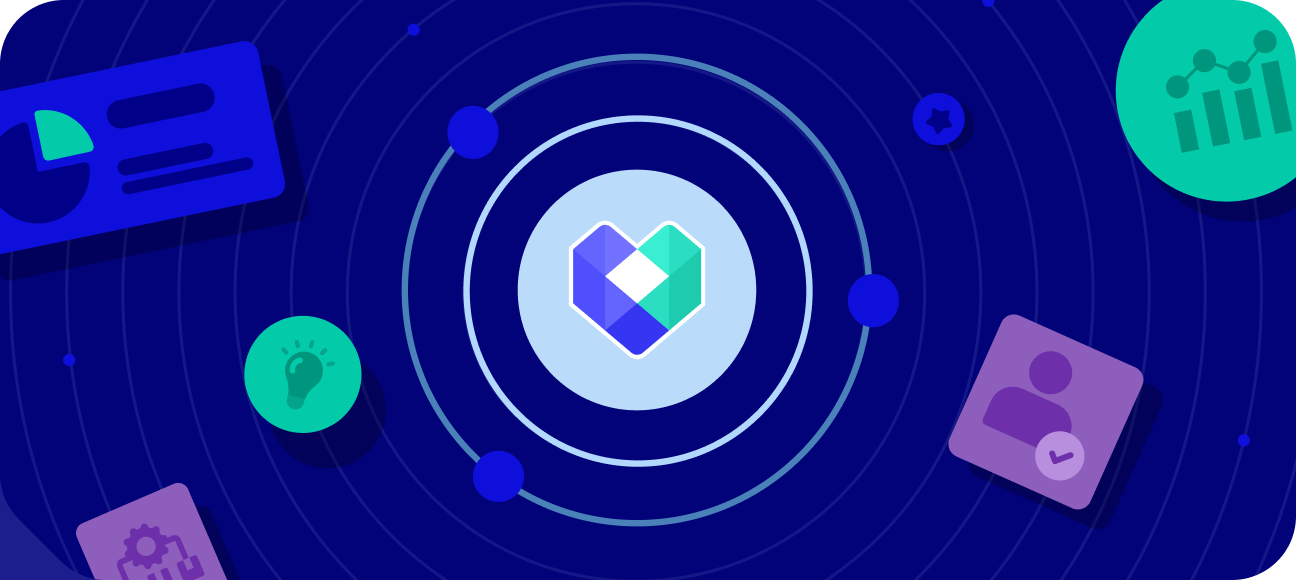
Warehouse management made simple
Gain full control over your inventory with smart automation, real-time tracking, and efficient workflows—ensuring your stock moves smoothly, every time
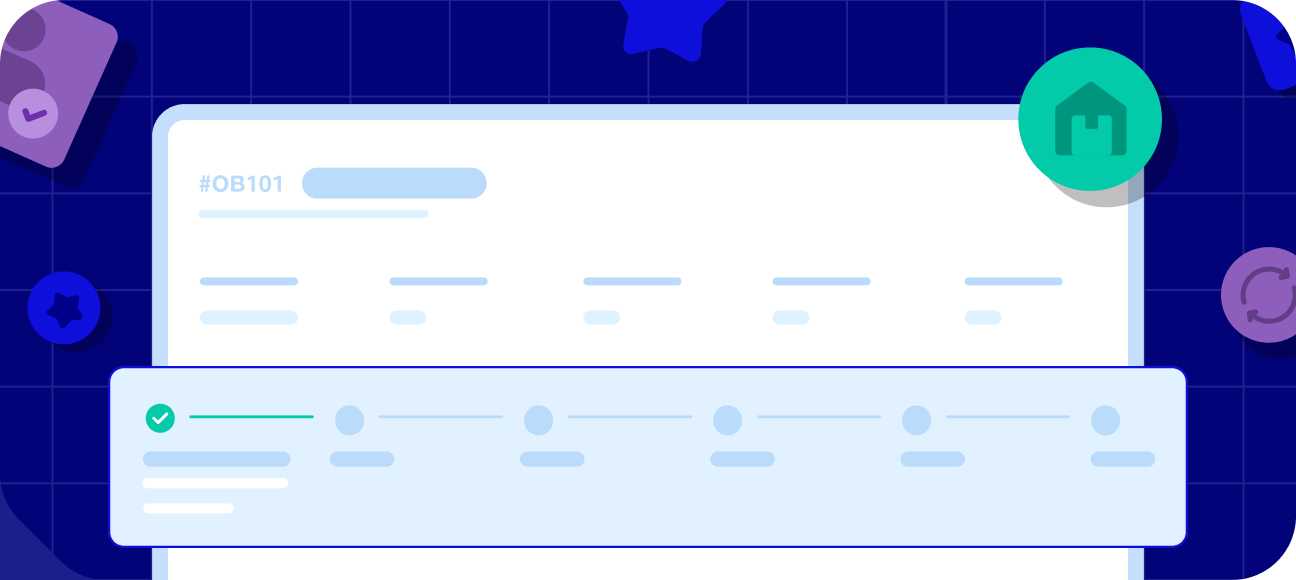
Launch hyperlocal commerce instantly
Set up and scale your hyper-local e-commerce with easy tools for web, orders, and delivery management—bringing you closer to customers, faster
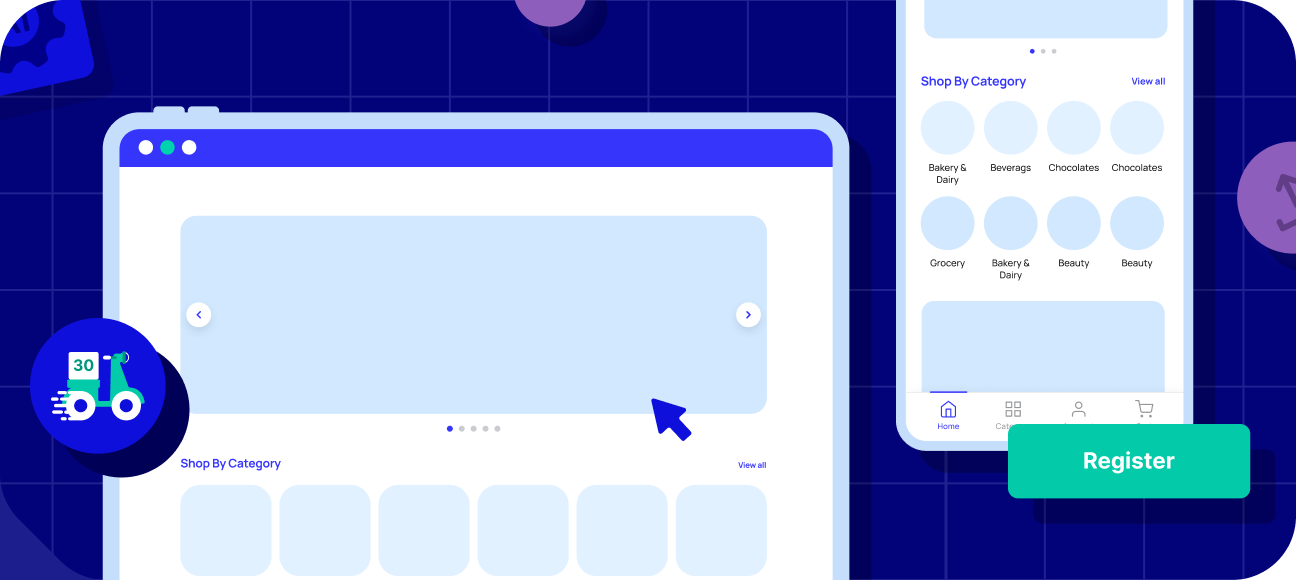
Delivery management made easy
Gain control over your deliveries with real-time visibility, smart automation, and seamless coordination—ensuring on-time arrivals, every time
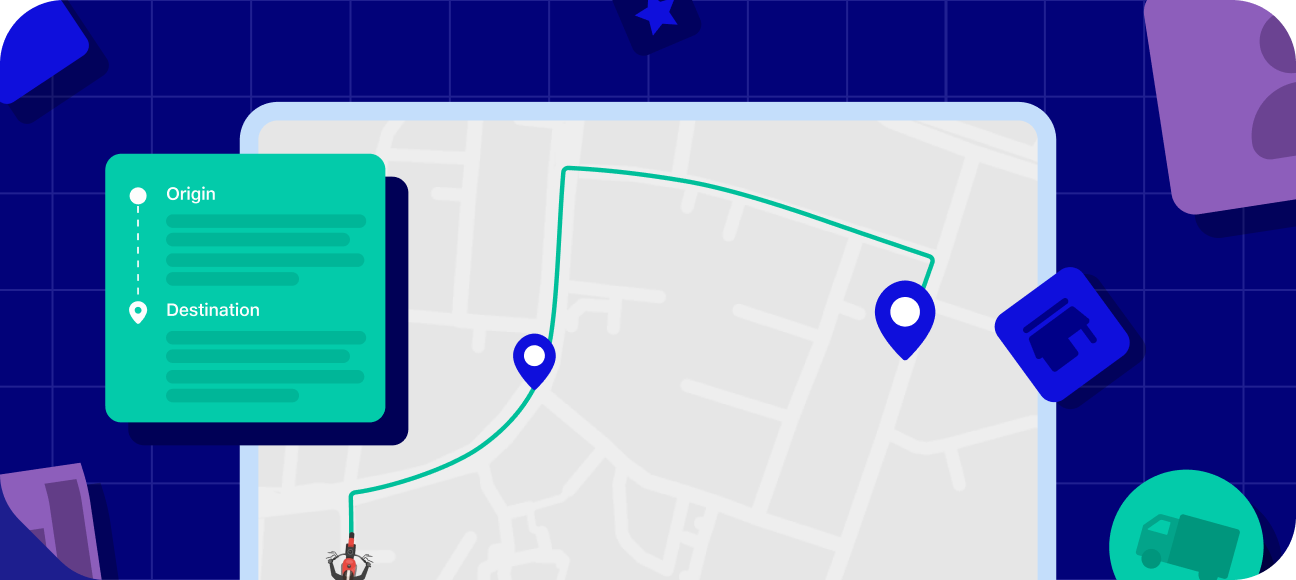
Order management made easy
Master every order with full visibility, smart automation, and effortless control—delivering the right outcomes, every time
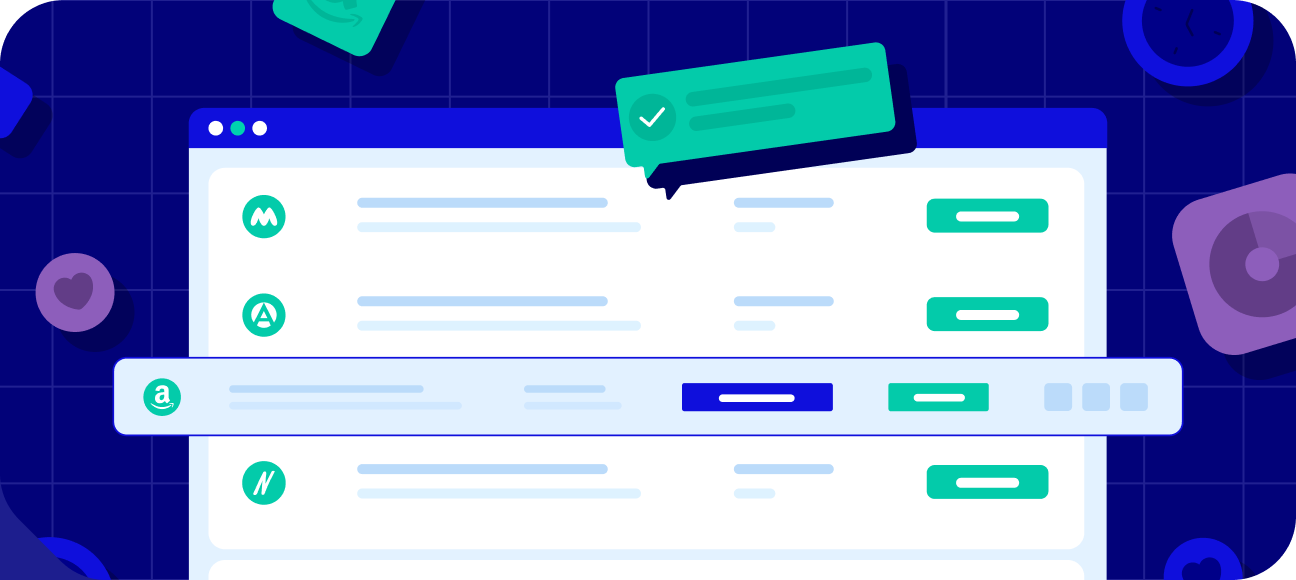
Speak to an expert
Explore how Fynd Commerce can improve every aspect of your business, from online to instore and beyond
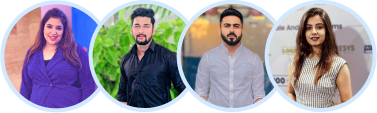
Speak to an expert
Explore how Fynd WMS powers operational excellence with our solution experts
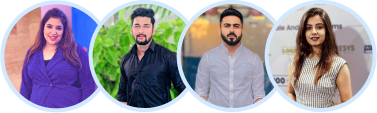
Speak to an expert
Explore how Fynd Quick powers hyperlocal businesses with our solution experts
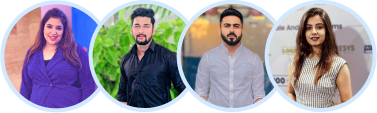
Speak to an expert
Explore how Fynd TMS powers better deliveries with our solution experts
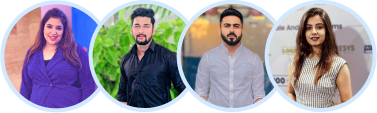
Speak to an expert
Explore how Fynd OMS powers seamless order management with our solution experts
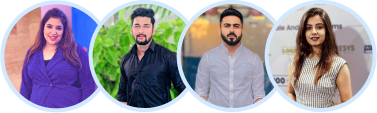
Featured Blog
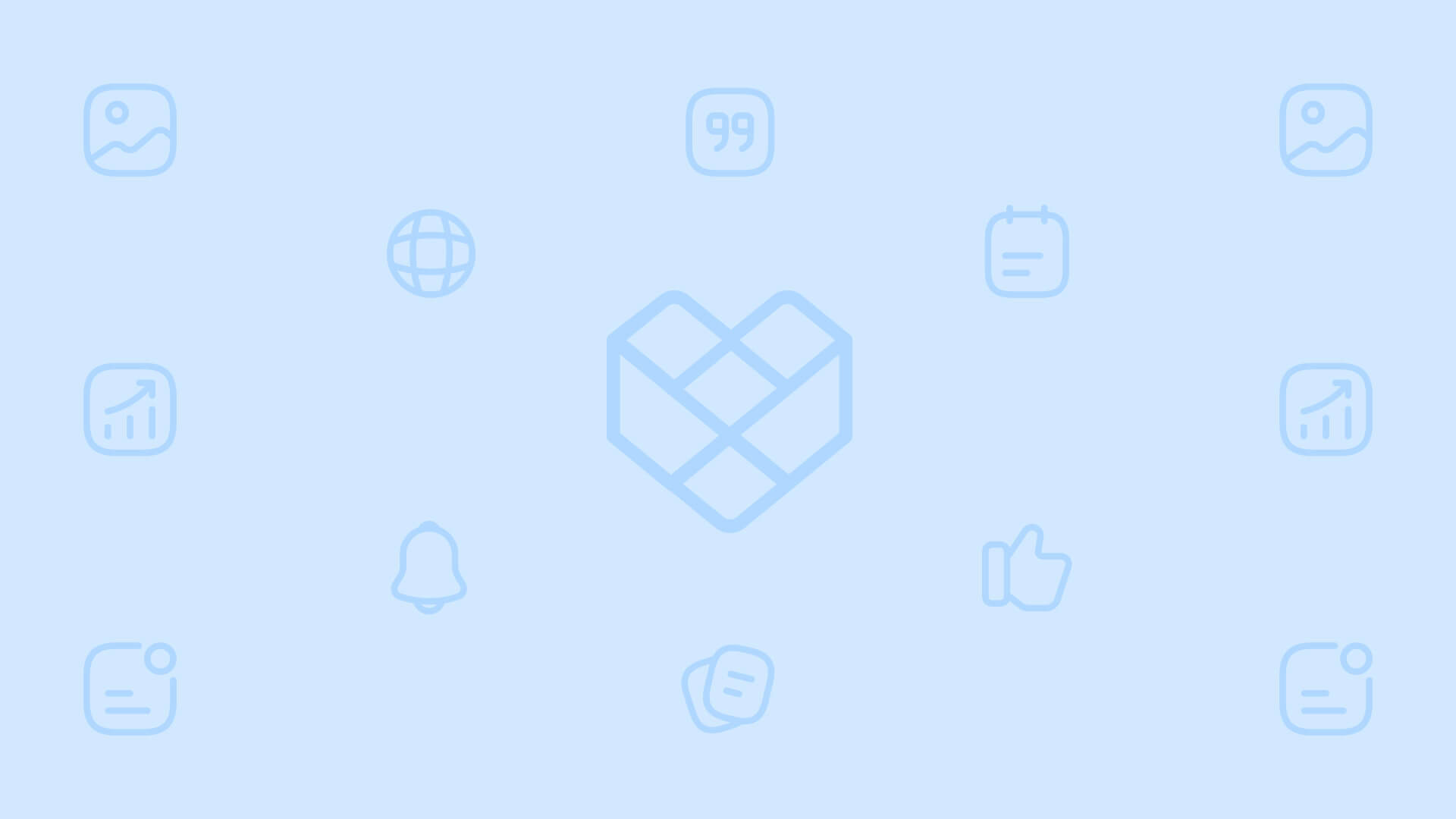
Empower your business, every step of the way
Simplify operations, scale smarter, and deliver better experiences with solutions designed to grow with your business
Take your warehouse management to the next level
Experience hassle-free inventory management with Fynd WMS, designed to keep your operations efficient and accurate. Book a demo to see how Fynd WMS can boost productivity and profits for your business!
Kickstart your quick delivery website
Experience seamless hyper-local commerce with Fynd Quick—engineered to keep things running smoothly and help you reach customers in record time. Book a demo and see how Fynd Quick can drive efficiency and growth for your business!
Level up your delivery management
See how you can manage deliveries with Fynd TMS, designed to streamline operations and keep your customers delighted. Book a demo with our team and find out how Fynd TMS can boost your efficiency and bottom line!
Take your order management to the next level
Discover how effortless order management can be with Fynd OMS, built to keep things running smoothly and make your customers happy. Book a demo with our team and see how Fynd OMS can help boost your efficiency and profits!
A Warehouse Management System (WMS) is a software designed to optimize and control warehouse operations from the moment goods arrive until they are shipped out. It plays a key role in supply chain management by giving real-time visibility into inventory levels. This helps improve efficiency in tracking stock, fulfilling orders, and managing logistics. WMS is essential for ensuring smooth warehouse operations and reducing mistakes.
WMS systems make processes like receiving, storing, picking, packing, and shipping more efficient by automating tasks. This reduces manual errors and boosts productivity. Technologies like barcode scanning and RFID make it easy to track inventory accurately. By automating these tasks, WMS saves time and improves overall warehouse performance, ensuring that products are always available when needed.
Moreover, WMS solutions can work together with other systems like Enterprise Resource Planning (ERP) and Transportation Management Systems (TMS). This integration helps businesses coordinate their logistics better, ensuring that inventory data is always up to date. As e-commerce grows, having an effective WMS is crucial for meeting customer expectations for quick and accurate order deliveries, all while keeping operational costs under control.
Benefits of Warehouse Management System
A Warehouse Management System (WMS) is an advanced software solution designed to streamline and enhance the overall efficiency of warehouse operations. By automating essential tasks such as inventory management, order processing, and labor allocation, WMS enables businesses to optimize their supply chain management.
This automation not only improves accuracy but also speeds up operations, leading to significant cost reductions. Furthermore, WMS facilitates better resource utilization, minimizes human error, and enhances customer satisfaction through faster, more accurate order fulfillment, ultimately improving overall operational performance and competitiveness in the market.
- Improved Inventory Visibility: Provides real-time insights into stock levels, reducing errors and ensuring optimal inventory management.
- Enhanced Customer Service: Facilitates accurate order fulfillment and timely deliveries, leading to increased customer satisfaction and loyalty.
- Optimized Space Utilization: Helps organize inventory efficiently, maximizing warehouse space and minimizing unnecessary storage costs.
- Increased Labor Productivity: Automates manual tasks, streamlining operations and allowing workers to focus on higher-value activities, thereby boosting productivity.
- Effective Labor Management: Enables better allocation of labor resources based on real-time demand, improving workforce efficiency and reducing operational costs.
Key Functions of Warehouse Management Systems
A Warehouse Management System (WMS) is critical for modern supply chain operations, offering powerful tools to manage and optimize various warehouse processes efficiently. By automating tasks such as inventory tracking, order fulfillment, and shipping, a WMS significantly enhances operational efficiency, accuracy, and productivity.
With real-time data access and seamless workflow integration, it enables businesses to streamline their operations, reduce labor and inventory costs, and improve decision-making. Additionally, WMS ensures faster, more accurate order processing, leading to improved customer satisfaction and better adaptability in an increasingly competitive marketplace.
1. Receiving and Put-Away Process
The WMS facilitates the efficient receiving of goods by automating the process of checking incoming items against purchase orders. It directs where items should be stored based on predefined business rules, ensuring optimal space utilization. This automation reduces manual errors and speeds up the put-away process, allowing for quicker inventory turnover and improved operational efficiency.
2. Inventory Management
A core function of WMS is real-time inventory management, which provides visibility into stock levels across various locations. Utilizing technologies like barcode scanning and RFID, the system tracks inventory movements accurately. This capability helps prevent stockouts and overstock situations, ensuring that businesses can meet customer demands without incurring unnecessary costs.
3. Order Fulfillment
WMS streamlines the order fulfillment process by automating picking, packing, and shipping tasks. It employs various picking methods, such as batch or zone picking, to enhance efficiency and reduce errors. By optimizing these processes, businesses can significantly improve their order processing times, leading to faster deliveries and increased customer satisfaction.
4. Real-Time Tracking
Real-time tracking is a critical feature of WMS that provides up-to-the-minute information on inventory levels and order statuses. This transparency allows warehouse managers to make informed decisions quickly, improving responsiveness to changing demands. For instance, real-time data can help identify bottlenecks in the supply chain and facilitate proactive problem-solving to maintain operational flow.
5. Shipping Management
The WMS streamlines the shipping process by automating the creation of shipping labels and documentation. It integrates with carriers to provide real-time shipping rates, ensuring that businesses can choose the most cost-effective options. By managing shipment scheduling and tracking, the system enhances visibility into delivery timelines, reducing delays and improving customer satisfaction. This function also helps ensure compliance with shipping regulations and reduces the risk of errors in documentation.
6. Labor Management
Labor management within a WMS optimizes workforce allocation by tracking employee performance and productivity in real time. The system can analyze labor data to identify trends, enabling managers to allocate resources more effectively based on demand fluctuations. By automating labor scheduling and task assignments, WMS helps minimize downtime and ensures that the right number of workers are available for peak periods, ultimately enhancing overall operational efficiency.
7. Returns Management
WMS simplifies the returns process by automating the handling of returned goods. It allows for quick assessment of returned items and facilitates their reintegration into inventory or proper disposal. By streamlining returns processing, businesses can reduce turnaround times and improve customer satisfaction. Additionally, effective returns management provides valuable insights into product quality and customer preferences, helping organizations make informed decisions regarding inventory and product offerings.
8. Reporting and Analytics
A robust WMS offers comprehensive reporting and analytics capabilities that provide insights into warehouse performance metrics. Users can generate reports on inventory turnover, order accuracy, labor efficiency, and more. This data-driven approach enables managers to identify trends, monitor KPIs, and make informed decisions for continuous improvement. By leveraging analytics, businesses can optimize their operations, reduce costs, and enhance overall supply chain performance.
9. Slotting Optimization
Slotting optimization is a WMS function that determines the optimal placement of items within the warehouse based on factors such as demand, size, weight, and velocity. By strategically locating frequently picked items closer to packing stations and grouping complementary products, the system enhances picking efficiency and reduces travel time for warehouse workers.
10. Yard Management
Yard management is a specialized function within WMS that oversees the movement and staging of trailers and containers in the warehouse yard. It tracks the arrival and departure of vehicles, manages dock door assignments, and coordinates the loading and unloading of goods. By optimizing yard operations, businesses can reduce congestion, minimize wait times, and ensure the efficient flow of materials in and out of the warehouse.
11. Warehouse Automation Integration
Many WMS solutions integrate with various warehouse automation technologies, such as conveyor systems, automated storage and retrieval systems (AS/RS), and robotic picking solutions. By seamlessly integrating with these systems, WMS can orchestrate and optimize their operations, ensuring smooth workflow and maximizing productivity. This integration also provides real-time data on the performance of automated systems, enabling managers to identify areas for improvement and make data-driven decisions regarding future investments in automation.
12. Workforce Management
Workforce management within a WMS encompasses tools for managing employee schedules, time and attendance, and training. By automating these processes, the system helps ensure that the right number of trained workers are available to handle warehouse tasks efficiently. It also provides insights into employee productivity and identifies areas where additional training or resources may be needed.
13. Demand Forecasting
Demand forecasting is a WMS function that uses historical data and predictive analytics to estimate future inventory requirements. By analyzing factors such as sales trends, seasonality, and market conditions, the system helps businesses anticipate demand fluctuations and proactively adjust inventory levels. This capability enables organizations to minimize stockouts, reduce excess inventory, and optimize inventory investment.
14. Inventory Cycle Counting
Cycle counting is a process within WMS that involves regularly counting a subset of inventory items to verify accuracy. This function helps identify and correct discrepancies between the system's records and actual stock levels. By conducting cycle counts on a scheduled basis, businesses can maintain a high level of inventory accuracy without disrupting daily operations. Cycle counting also helps pinpoint areas where inventory management processes may need improvement, such as in receiving, put-away, or picking.
15. Warehouse Layout Optimization
Warehouse layout optimization is a WMS function that helps businesses design and configure their warehouse space for maximum efficiency. By analyzing factors such as product characteristics, storage requirements, and workflow patterns, the system can recommend optimal layouts for storage areas, picking zones, and packing stations. This optimization process aims to minimize travel distances for warehouse workers, reduce congestion, and improve overall operational flow.
16. Collaboration and Integration
WMS solutions often include collaboration and integration capabilities that enable seamless communication and data exchange with other supply chain partners and systems. This includes integrating with Enterprise Resource Planning (ERP) systems to share inventory data, purchase orders, and customer information. WMS can also integrate with Transportation Management Systems (TMS) to coordinate logistics and optimize shipping decisions.
Challenges Addressed by WMS
A Warehouse Management System (WMS) is designed to tackle the challenges commonly faced in warehouse operations, such as inventory inaccuracies, slow order fulfillment, and poor space utilization. By automating essential processes and providing real-time data insights, WMS enhances operational efficiency and accuracy across the entire supply chain. It enables businesses to streamline workflows, optimize inventory management, and reduce human errors, resulting in faster order processing and better space utilization.
Moreover, the system supports more informed decision-making, leading to improved customer satisfaction, reduced operational costs, and a more agile response to market demands and changes.
- Inventory Inaccuracy: WMS provides real-time tracking and automated updates, significantly reducing discrepancies between actual stock levels and recorded data.
- Inefficient Space Utilization: By analyzing warehouse layouts and optimizing storage locations, WMS maximizes available space.
- Slow Order Fulfillment: WMS automates the picking, packing, and shipping processes, speeding up order fulfillment.
- Lack of Real-Time Data: WMS offers comprehensive real-time data visibility, allowing managers to monitor inventory levels, order statuses, and other critical metrics.
Conclusion
A Warehouse Management System (WMS) plays a vital role in optimizing warehouse operations. By automating processes such as inventory control, order fulfillment, and space utilization, it enhances efficiency, accuracy, and decision-making. A WMS ultimately reduces costs, improves customer satisfaction, and ensures smoother, more effective management of the entire supply chain.
Frequently asked questions
A WMS is software that automates warehouse operations, such as inventory tracking, order fulfillment, and shipping. It improves efficiency, reduces costs, enhances customer satisfaction, and streamlines supply chain management.
WMS uses real-time tracking with barcode scanning and RFID to minimize human errors. It automates updates, provides visibility into stock levels, and issues alerts for discrepancies, ensuring accurate inventory management.
Yes, WMS integrates with ERP and TMS systems, allowing seamless data sharing. This improves supply chain coordination, decision-making, and operational efficiency.
WMS speeds up order fulfillment, improves inventory management, prevents stockouts, and offers demand forecasting through real-time analytics, enhancing customer satisfaction.
WMS automates tasks like picking and packing, optimizes workflows, and provides performance metrics, boosting efficiency and reducing downtime.
WMS resolves issues like inventory inaccuracies, slow fulfillment, poor space utilization, and lack of real-time data, improving overall operational efficiency and customer satisfaction.