Solutions for every business need
Growth comes in all shapes and sizes. Whether it’s smoother operations, sharper insights, higher revenue—or all of the above—we’ve got you covered
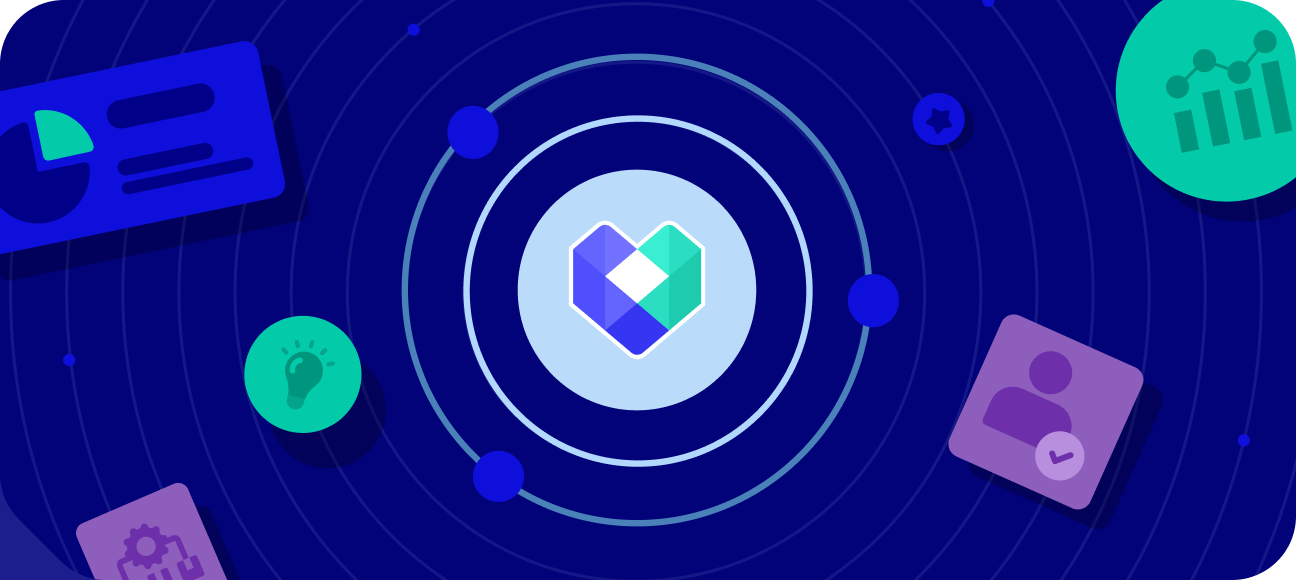
Warehouse management made simple
Gain full control over your inventory with smart automation, real-time tracking, and efficient workflows—ensuring your stock moves smoothly, every time
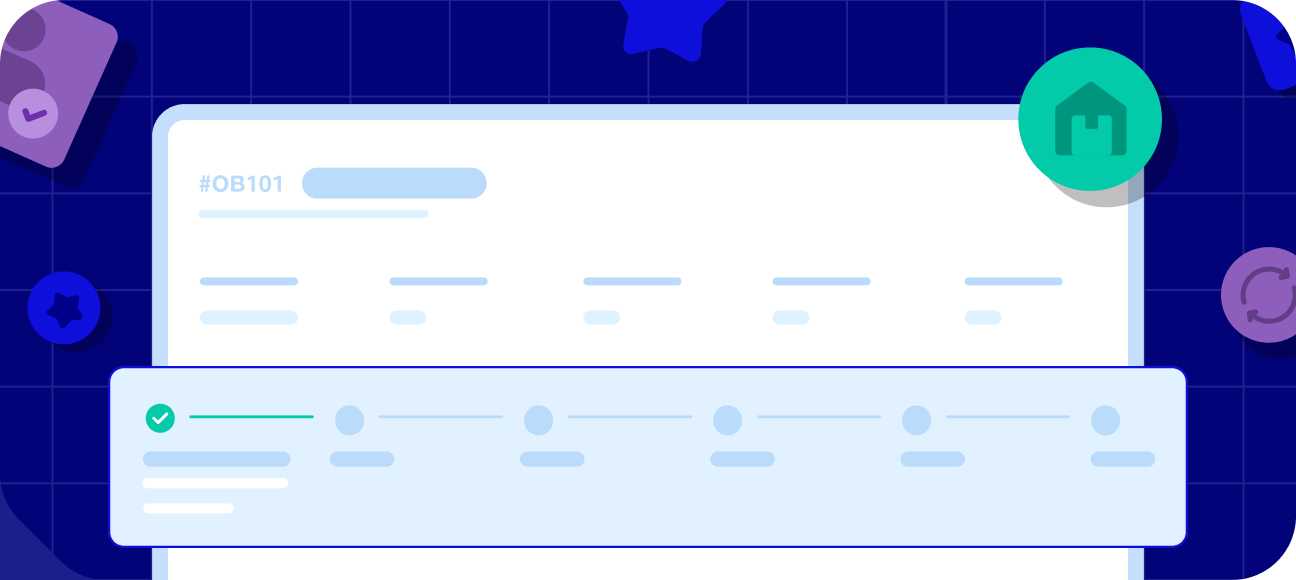
Launch hyperlocal commerce instantly
Set up and scale your hyper-local e-commerce with easy tools for web, orders, and delivery management—bringing you closer to customers, faster
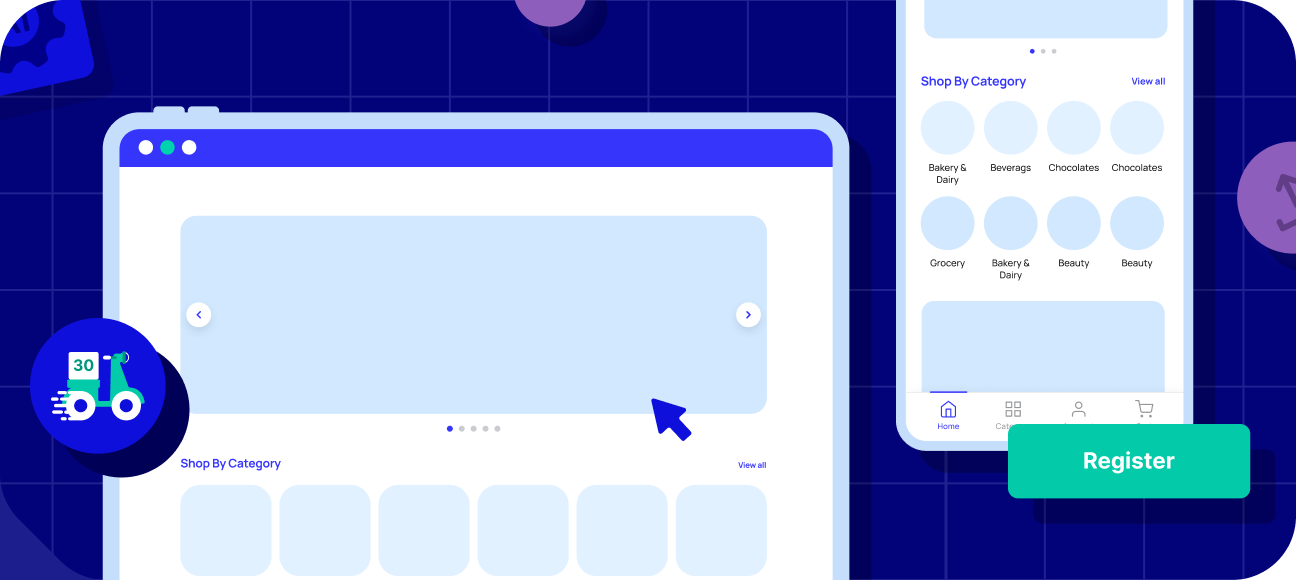
Delivery management made easy
Gain control over your deliveries with real-time visibility, smart automation, and seamless coordination—ensuring on-time arrivals, every time
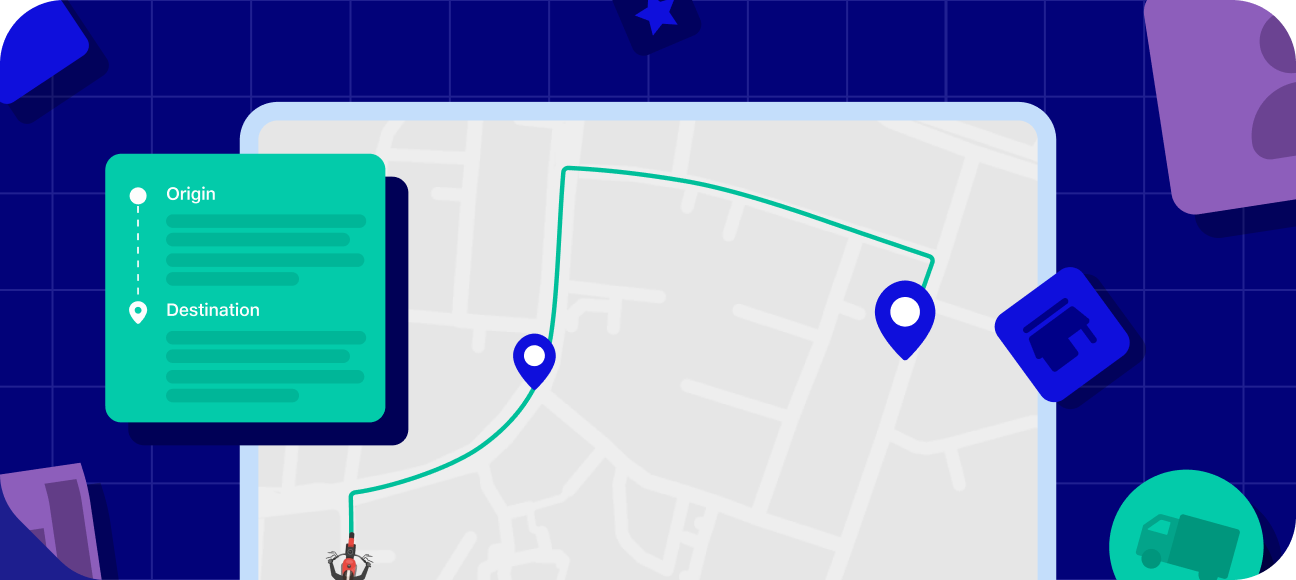
Order management made easy
Master every order with full visibility, smart automation, and effortless control—delivering the right outcomes, every time
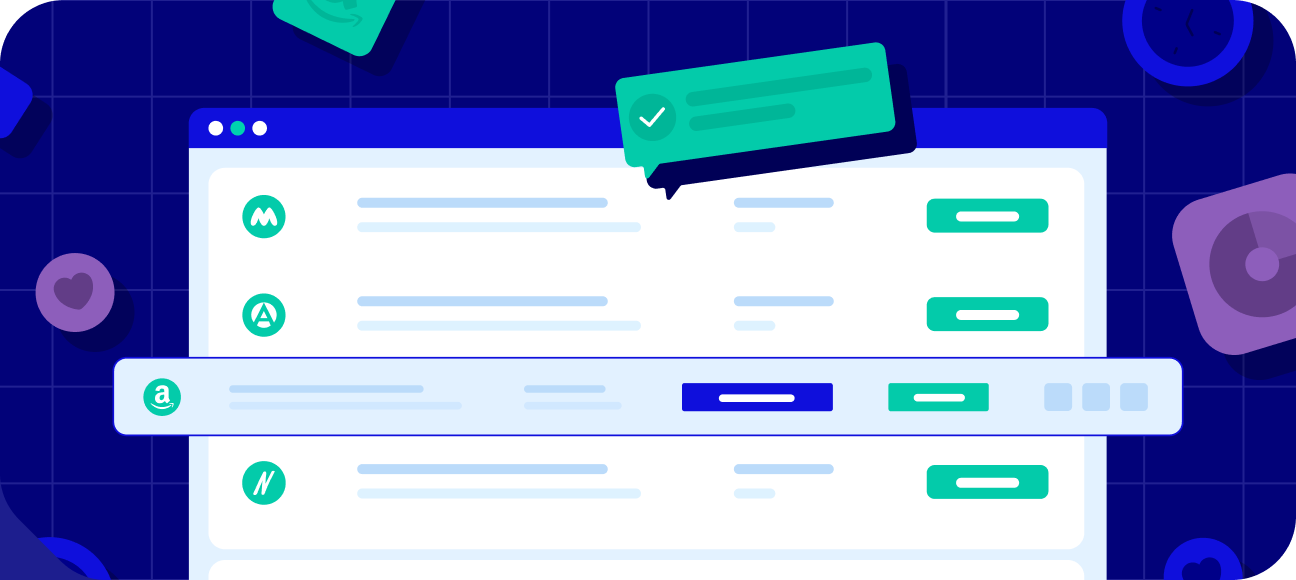
Speak to an expert
Explore how Fynd Commerce can improve every aspect of your business, from online to instore and beyond
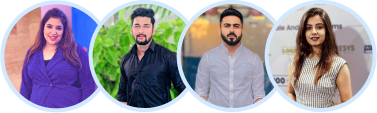
Speak to an expert
Explore how Fynd WMS powers operational excellence with our solution experts
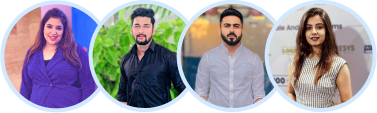
Speak to an expert
Explore how Fynd Quick powers hyperlocal businesses with our solution experts
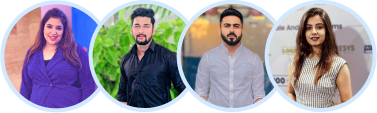
Speak to an expert
Explore how Fynd TMS powers better deliveries with our solution experts
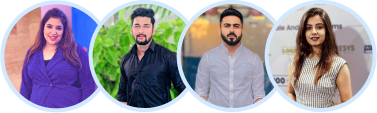
Speak to an expert
Explore how Fynd OMS powers seamless order management with our solution experts
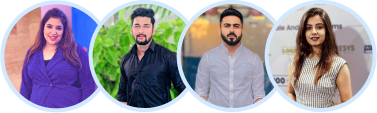
Featured Blog
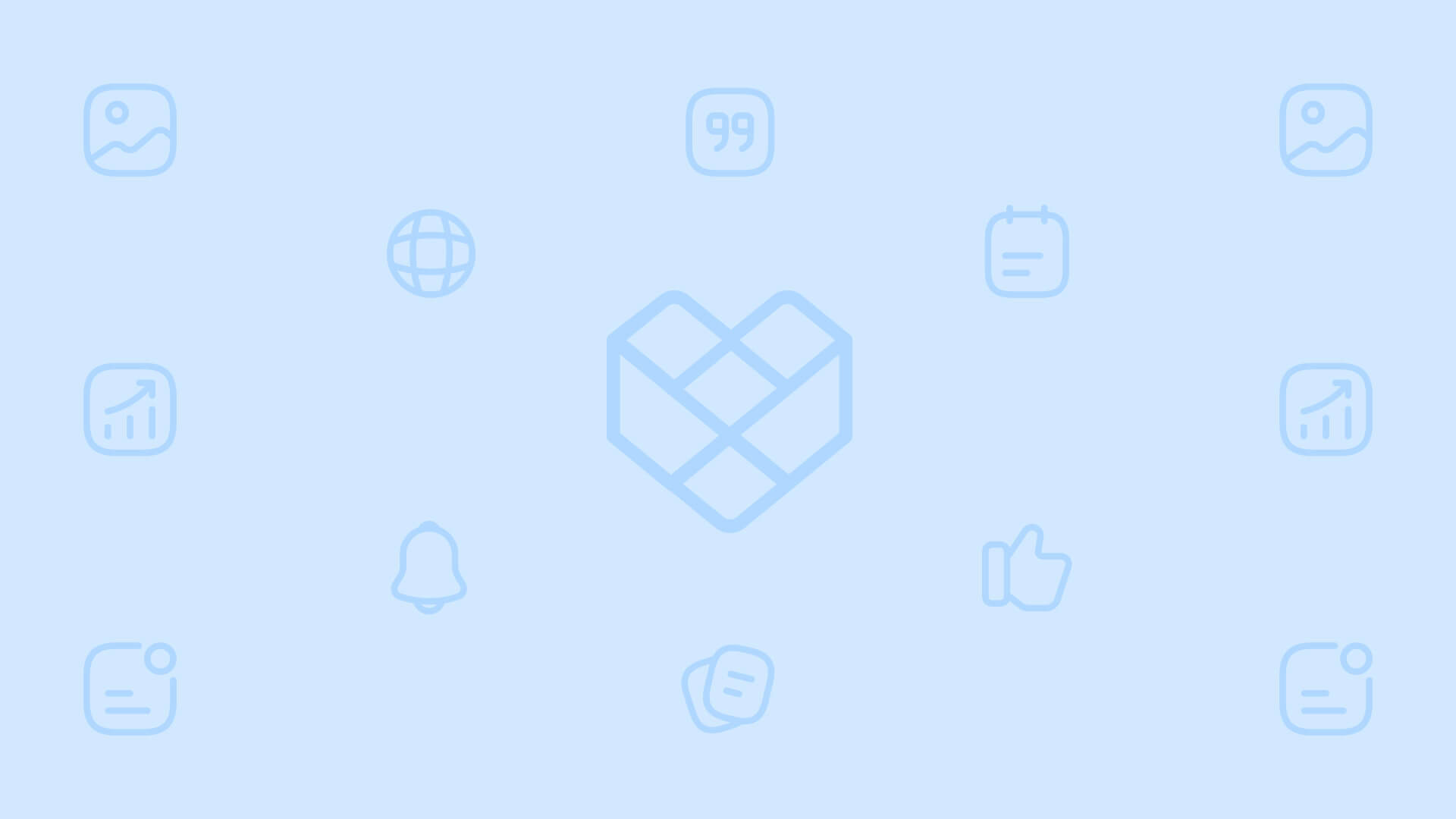
Empower your business, every step of the way
Simplify operations, scale smarter, and deliver better experiences with solutions designed to grow with your business
Take your warehouse management to the next level
Experience hassle-free inventory management with Fynd WMS, designed to keep your operations efficient and accurate. Book a demo to see how Fynd WMS can boost productivity and profits for your business!
Kickstart your quick delivery website
Experience seamless hyper-local commerce with Fynd Quick—engineered to keep things running smoothly and help you reach customers in record time. Book a demo and see how Fynd Quick can drive efficiency and growth for your business!
Level up your delivery management
See how you can manage deliveries with Fynd TMS, designed to streamline operations and keep your customers delighted. Book a demo with our team and find out how Fynd TMS can boost your efficiency and bottom line!
Take your order management to the next level
Discover how effortless order management can be with Fynd OMS, built to keep things running smoothly and make your customers happy. Book a demo with our team and see how Fynd OMS can help boost your efficiency and profits!
A Warehouse Management System (WMS) is a transformative software solution designed to optimize warehouse operations by managing inventory, tracking shipments, and improving order fulfillment. According to a report by Gartner, companies that implement a WMS can see up to a 20% reduction in inventory costs and a 30% increase in warehouse productivity. Key features include real-time inventory tracking, automated order processing, and advanced analytics. These capabilities ensure accurate inventory levels, faster order fulfillment, and streamlined warehouse operations, inspiring businesses to achieve new levels of efficiency.
Fynd WMS is a top choice for businesses seeking to enhance their warehouse operations. With our advanced WMS solution, you can experience a dramatic improvement in efficiency, accuracy, and customer satisfaction. Our system integrates with existing ERP and CRM tools, providing real-time insights and automation. This integration significantly reduces picking errors and order processing times, giving businesses the confidence that their operations will run smoothly with Fynd WMS.
This page addresses the common challenges businesses face in managing warehouse operations, such as high inventory costs and inefficiencies in order processing. By highlighting the features and benefits of a WMS, we aim to help companies understand how implementing this technology can significantly improve their supply chain management and overall efficiency, providing them with the support they need to overcome these challenges.
Features of a Warehouse Management System
Discover the key features of a Warehouse Management System (WMS) that make it an essential tool for modern businesses. From real-time inventory tracking to order management and warehouse automation, a WMS streamlines and automates warehouse operations, enhancing efficiency and reducing costs.
Inventory Tracking
Inventory tracking provides real-time visibility into stock levels, preventing stockouts and overstock issues. By maintaining up-to-date inventory data, businesses can manage replenishment efficiently and reduce holding costs. This leads to improved customer satisfaction, more efficient warehouse operations, and a smoother supply chain, ensuring that products are always available when needed without excess inventory.
Key features include:
- Real-time visibility
- Prevents stockouts and overstocking
- Manages replenishment efficiently
- Reduces holding costs
- Improves customer satisfaction
Order Management
Order management streamlines the order process from start to finish, automating picking, packing, and shipping. This enhances accuracy and reduces fulfillment times. A WMS ensures faster deliveries and improves the overall customer experience by prioritizing orders based on demand. It provides timely and accurate order fulfillment, which boosts efficiency and customer satisfaction.
WMS’s order management features offer:
- Automated order process
- Enhanced accuracy
- Reduced fulfillment times
- Improved customer experience
Warehouse Automation
Warehouse automation employs robotics, conveyors, and automated systems to streamline operations. This reduces manual labor, accelerates workflows, and improves accuracy in handling goods. With enhanced efficiency in managing inventory volumes and minimizing errors, automation leads to significant cost savings and helps warehouses meet increasing demand more effectively.
Use warehouse automation to:
- Reduces manual labor
- Accelerates workflows
- Improves accuracy
- Enhances efficiency
Task Scheduling
Task scheduling organizes warehouse activities and prioritizes tasks according to employee skills and availability. Automating task scheduling prevents bottlenecks and minimizes downtime, leading to streamlined workflows and increased productivity. Efficient scheduling ensures smooth warehouse operations, optimizes resources and enhances overall performance and operational success.
With task scheduling, you can:
- Organize activities and prioritize tasks
- Prevent bottlenecks
- Minimize downtime
- Streamline workflows
- Increase productivity
Barcoding and Scanning
Barcoding and scanning ensure accurate data entry throughout inventory management. This technology eliminates manual errors and enhances inventory accuracy by scanning barcodes at various stages. Rapid and precise inventory tracking improves order fulfillment, reduces mistakes, and boosts overall warehouse operational efficiency.
Use barcoding and scanning to:
- Ensure accurate data entry
- Eliminate manual errors
- Enhance inventory accuracy
- Improve order fulfillment
- Boost operational efficiency
Labour Management
Labor management features track employee performance, working hours, and task assignments. By analyzing this data, businesses can optimize labor allocation and improve efficiency. This reduces labor costs, minimizes downtime, and enhances warehouse operations by assigning tasks to the most effective workers.
Key features include:
- Tracks performance and hours
- Optimizes labor allocation
- Reduces labor costs
- Minimizes downtime
- Enhances efficiency
Analytics and Reporting
Analytics and reporting provide detailed insights into warehouse performance, such as order accuracy and fulfillment speed. This data enables businesses to make informed decisions, optimize operations, and identify cost-saving opportunities, driving continuous improvement and maximizing productivity.
WMS’s analytics and reporting offers:
- Provides performance insights
- Monitors accuracy and speed
- Informs decision-making
- Optimizes operations
- Identifies cost-saving opportunities
Integration with Other Systems
WMS integration with ERP, CRM, and other business systems ensures seamless data flow. This provides a unified view of inventory, sales, and supply chain operations, streamlining processes, enhancing communication, and improving overall efficiency by reducing manual errors.
Integration of WMS with other systems offers:
- Seamless data flow
- Unified view
- Streamlined processes
- Enhanced efficiency
Real-Time Reporting
Real-time reporting instantly updates inventory levels, order statuses, and operational performance. This feature allows businesses to make immediate decisions, address issues promptly, and adapt to changing conditions, enhancing responsiveness and operational efficiency.
Critical features of real-time reporting include:
- Provides instant updates
- Enables immediate decisions
- Addresses issues promptly
- Enhances responsiveness
- Improves efficiency
Return Management
Return management automates returns processing, including authorization, inspection, and restocking. This reduces the time and effort needed, minimizes errors, and ensures returned items are quickly reintegrated into inventory, improving customer satisfaction and inventory management.
With return management, you can:
- Automate return processing
- Reduce time and effort
- Minimize errors
- Improve inventory management
Multi-Location Support
Multi-location support manages operations across multiple warehouse sites. Centralizing data and synchronizing activities ensures consistent inventory management and efficient order fulfillment across locations, improving overall efficiency and streamlined logistics.
WMS’s multi-location support offers:
- Management of operations across sites
- Centralization of data
- Synchronization of activities
- Ensured consistent inventory management
- Improved efficiency
Demand Forecasting
Demand forecasting uses historical data to predict future inventory needs. This feature helps businesses adjust stock levels to match anticipated demand, reducing the risk of overstocking or stockouts and aligning inventory with actual demand.
Key features include:
- Predicts future inventory needs
- Uses historical data
- Adjusts stock levels
- Reduces overstocking and stockouts
- Aligns inventory with demand
Shipping Optimization
Shipping optimization selects the most cost-effective carriers and routes based on cost and delivery speed. This feature reduces transportation costs, improves delivery times, and enhances customer satisfaction by analyzing and choosing optimal shipping options.
Shipping optimization offers:
- Cost-effective carriers and routes
- Reduced transportation costs
- Improved delivery times
- Enhanced customer satisfaction
Cross-Docking
Cross-docking minimizes storage time by transferring goods directly from receiving to shipping. This reduces handling costs, speeds up order fulfillment, and is beneficial for high-velocity items, improving supply chain efficiency and turnover rates.
Critical features of cross-docking include:
- Minimized storage time
- Transfer of goods directly
- Reduced handling costs
- Improved supply chain efficiency
Customizable Dashboards
Customizable dashboards allow users to create tailored views of critical metrics and performance indicators. This feature provides relevant data for different roles, ensuring stakeholders have access to the necessary information for informed decision-making.
With customizable dashboards, you can:
- Utilize tailored views
- Display key metrics
- View role-specific data
- Ensure relevant information
- Support informed decision-making
Slotting Optimization
Slotting optimization assigns the most efficient storage locations based on item popularity and turnover rates. This reduces picking time, improves warehouse efficiency, and ensures that frequently picked items are easily accessible, enhancing overall space utilization.
Key features include:
- Assign efficient storage locations
- Reduces picking time
- Improves warehouse efficiency
- Ensures easy access to popular items
- Enhances space utilization
Quality Control
Quality control automates checks during receiving, storage, and picking to ensure products meet required standards. This feature maintains high product quality, reduces returns due to defects, and enhances customer satisfaction through consistent product standards.
WMS’s quality control offers:
- Automated quality checks
- Ensured product standards
- Reduced returns due to defects
- Enhanced customer satisfaction
Why is WMS Suitable for Every Business?
A Warehouse Management System (WMS) benefits businesses of all sizes, from small startups to large enterprises. It helps streamline operations, reduce costs, and improve inventory accuracy. Whether you’re a growing company or an established player, implementing a WMS can give you the competitive edge needed to scale efficiently and meet customer demands.
Here is why small, medium, and large businesses should consider using a warehouse management system (WMS):
- Small Businesses: A WMS automates inventory management for small businesses, improving stock control, reducing errors, and enhancing efficiency. This supports sustainable growth and a more organized supply chain.
- Medium-Sized Businesses: A WMS centralizes operations, optimizes space, and improves order fulfillment for medium-sized businesses, helping to reduce operational costs and meet growing customer demands.
- Large Enterprises: Large enterprises benefit from a WMS by automating logistics, ensuring faster and more accurate order processing, and streamlining complex operations for cost savings and better scalability.
Efficient Workflow of a Warehouse Management System (WMS)
The flow of a Warehouse Management System (WMS) encompasses several critical steps designed to streamline warehouse operations and enhance overall efficiency. It begins with the initial receiving of goods, where inventory is logged and tracked in real-time.
The system then moves through stages like inventory management, order picking, packing, and shipping. By automating and optimizing these processes, a WMS significantly improves accuracy, minimizes errors, and reduces operational costs. This comprehensive approach boosts efficiency and ensures smoother workflows and better performance across the supply chain.
- Receiving: Goods are checked and recorded into the system upon arrival. This step ensures accurate inventory counts and identifies any discrepancies or damage.
- Putaway: Products are allocated to specific storage locations based on the WMS's recommendations. This optimizes space and facilitates easier retrieval.
- Inventory Management: The WMS monitors stock levels and updates records in real time. This helps maintain accurate inventory counts and reduces the risk of stockouts or overstocking.
- Order Picking: The system generates picking lists and guides warehouse staff to the correct locations, speeding up the picking process and reducing errors.
- Shipping: Orders are packed and labeled according to the WMS's instructions. The system updates order status and generates shipping documents, ensuring accurate and timely deliveries.
Conclusion
A Warehouse Management System (WMS) is an invaluable asset for businesses of all sizes. It enhances efficiency and boosts customer satisfaction by improving inventory accuracy, optimizing warehouse operations, and allowing for scalable growth.
With a WMS, companies can streamline their processes and reduce costs significantly. Discover how Fynd WMS can revolutionize your warehouse management—reach out to our experts today to explore the benefits and see the transformation firsthand.
Frequently asked questions
A Warehouse Management System (WMS) is software designed to manage and control daily warehouse operations. It helps businesses track inventory, streamline order fulfillment, and optimize warehouse processes from receiving goods to shipping them out.
A WMS automates inventory management for small businesses, reducing manual errors and saving time. It improves stock accuracy and order fulfillment efficiency, allowing you to manage growth more effectively without significant increases in labor or resources.
Yes, most modern WMS solutions are designed to integrate seamlessly with other business systems, such as ERP and CRM platforms. This integration ensures smooth data flow across systems, enhancing overall operational efficiency and providing a unified view of your business processes.
Key features to consider include real-time inventory tracking, automated order processing, space optimization, and reporting capabilities. Look for a WMS that offers flexibility and scalability to adapt to your business needs and growth plans.
A WMS enhances order fulfillment by automating picking, packing, and shipping processes. It provides real-time visibility into inventory levels, enabling faster and more accurate order processing. This reduces lead times and improves overall customer satisfaction.
Absolutely. A WMS helps large enterprises manage complex warehouse operations and multiple distribution centers efficiently. It optimizes logistics, reduces operational costs, and improves inventory accuracy, making it a valuable investment for maintaining competitive advantage and scaling operations effectively.