Solutions for every business need
Growth comes in all shapes and sizes. Whether it’s smoother operations, sharper insights, higher revenue—or all of the above—we’ve got you covered
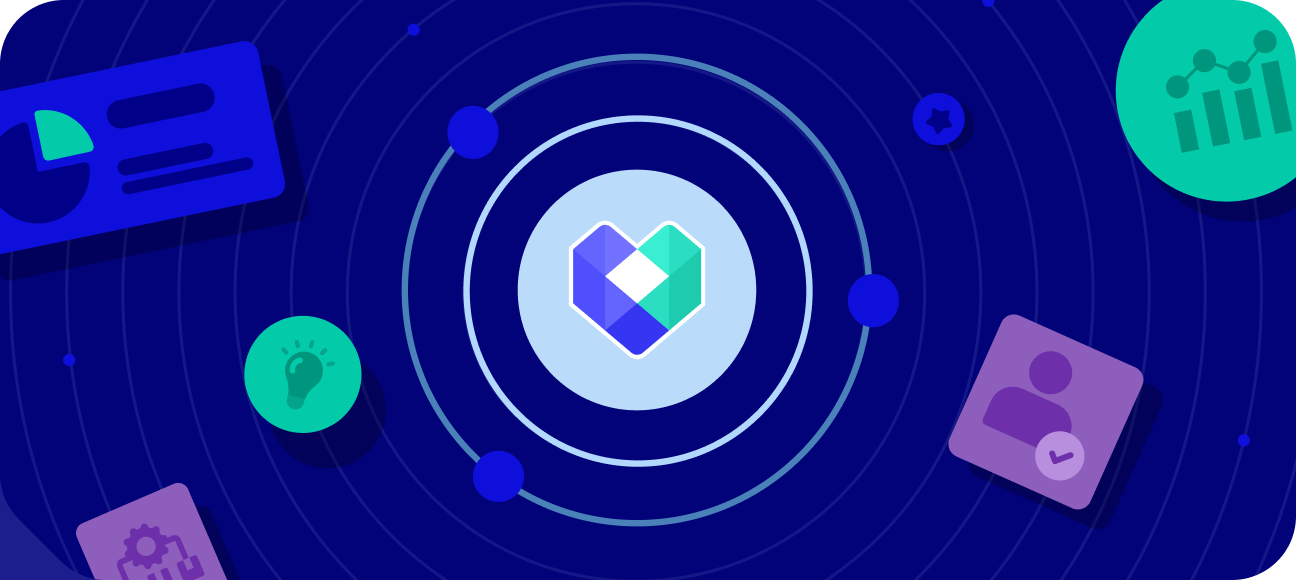
Warehouse management made simple
Gain full control over your inventory with smart automation, real-time tracking, and efficient workflows—ensuring your stock moves smoothly, every time
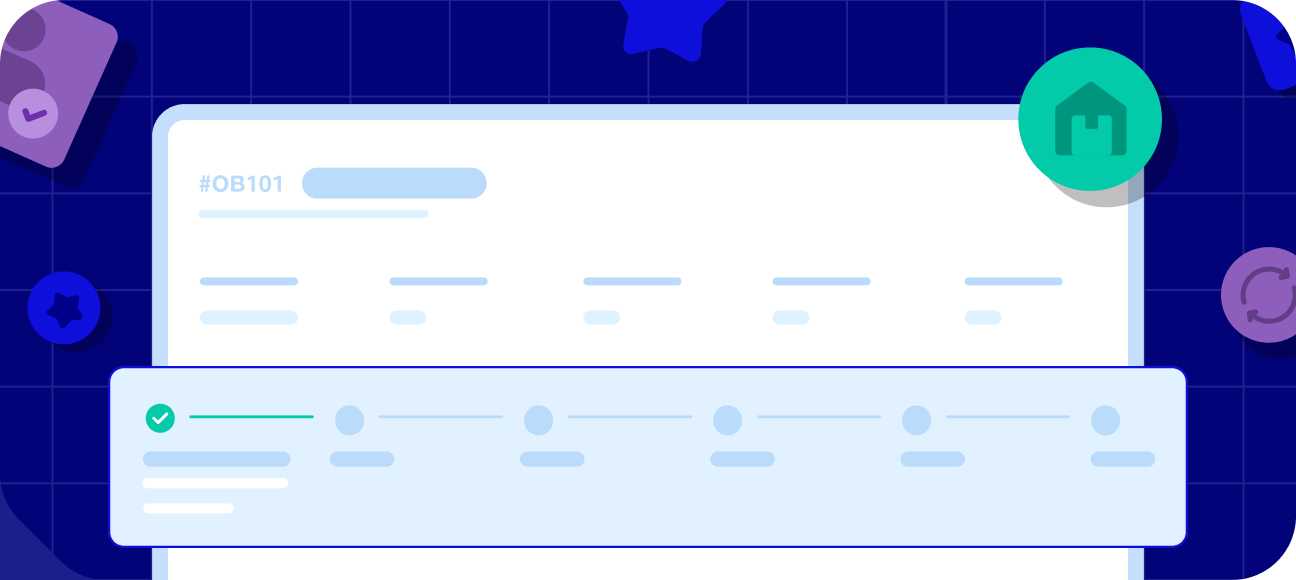
Launch hyperlocal commerce instantly
Set up and scale your hyper-local e-commerce with easy tools for web, orders, and delivery management—bringing you closer to customers, faster
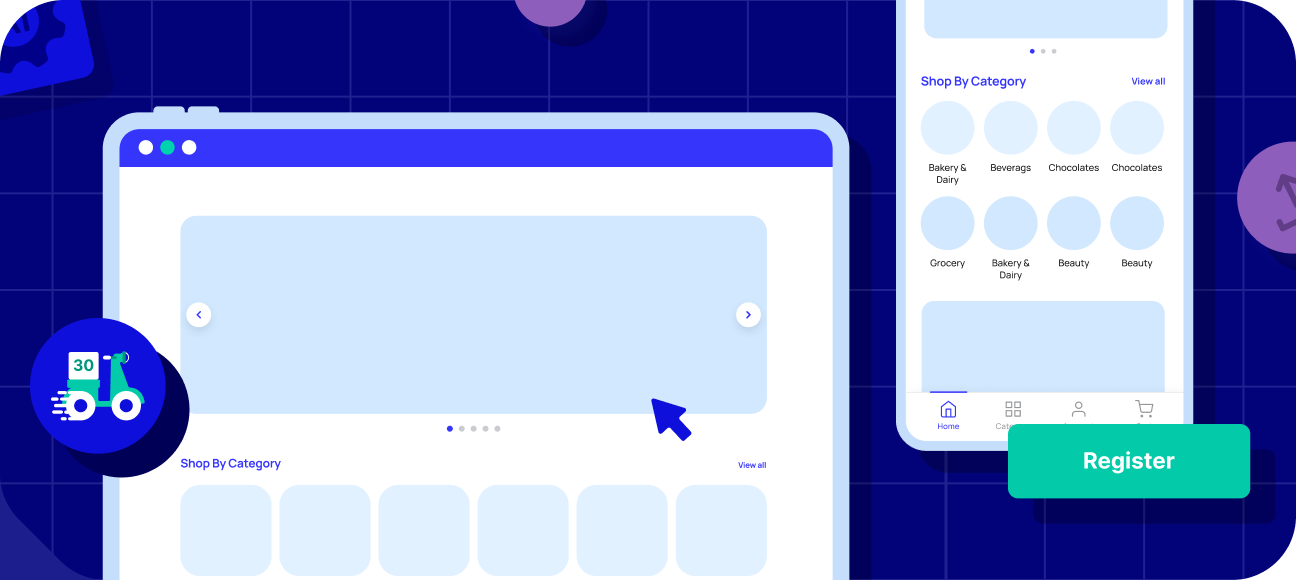
Delivery management made easy
Gain control over your deliveries with real-time visibility, smart automation, and seamless coordination—ensuring on-time arrivals, every time
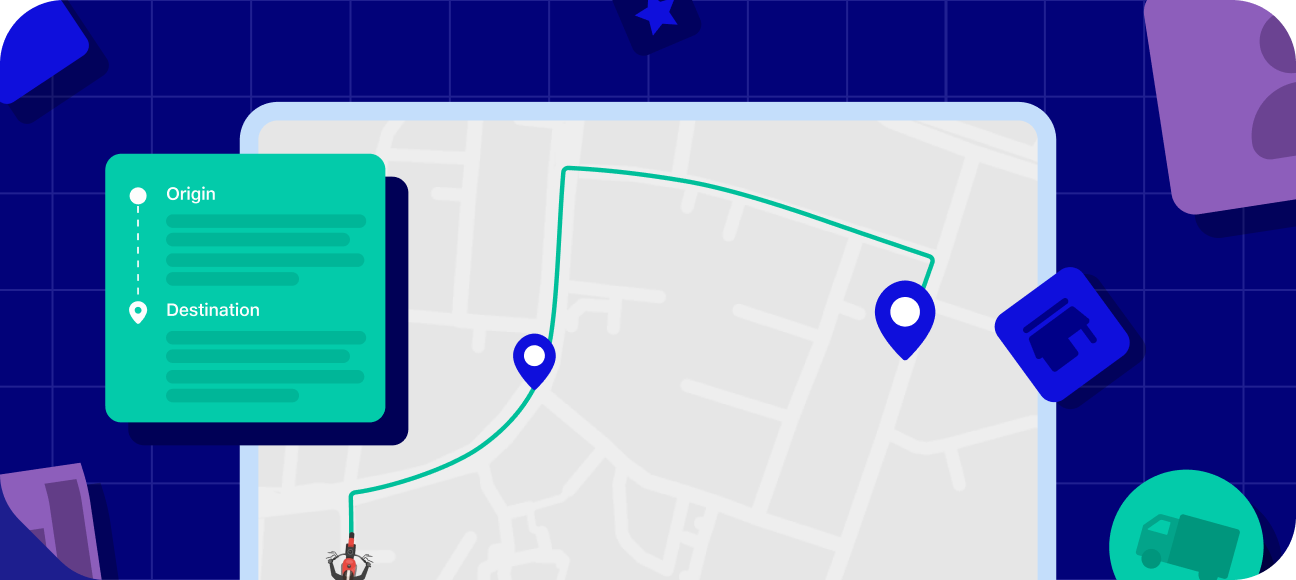
Order management made easy
Master every order with full visibility, smart automation, and effortless control—delivering the right outcomes, every time
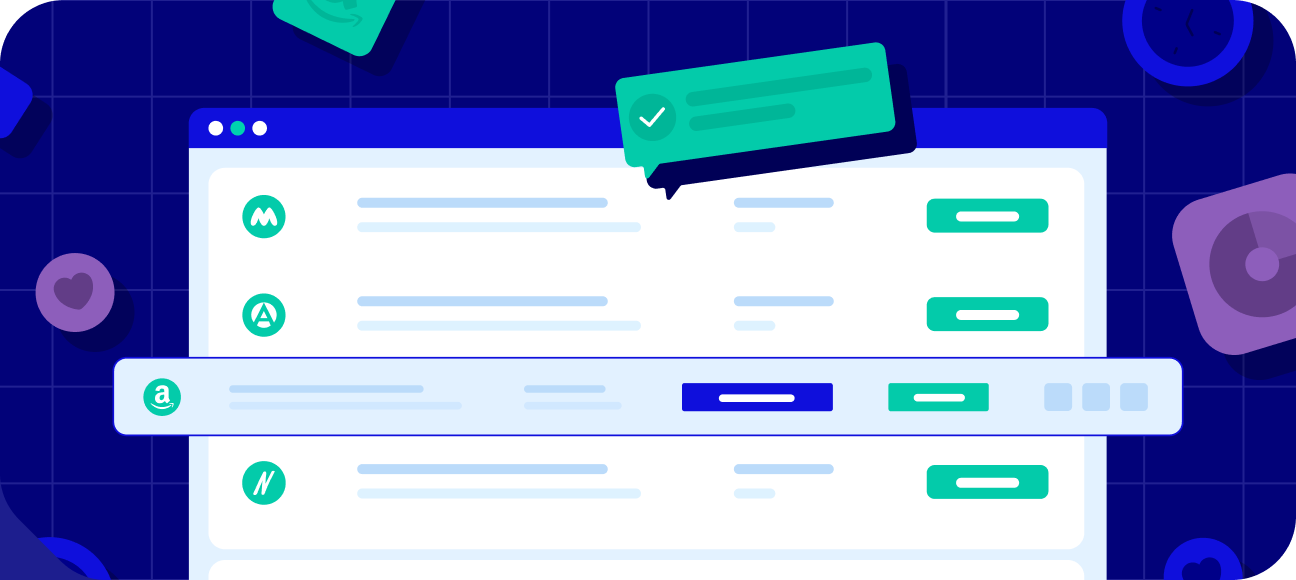
Speak to an expert
Explore how Fynd Commerce can improve every aspect of your business, from online to instore and beyond
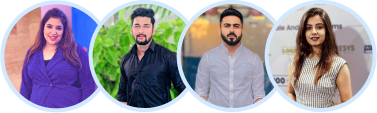
Speak to an expert
Explore how Fynd WMS powers operational excellence with our solution experts
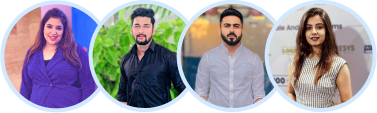
Speak to an expert
Explore how Fynd Quick powers hyperlocal businesses with our solution experts
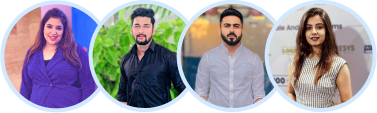
Speak to an expert
Explore how Fynd TMS powers better deliveries with our solution experts
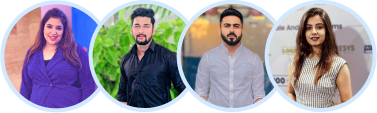
Speak to an expert
Explore how Fynd OMS powers seamless order management with our solution experts
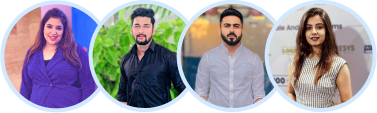
Featured Blog
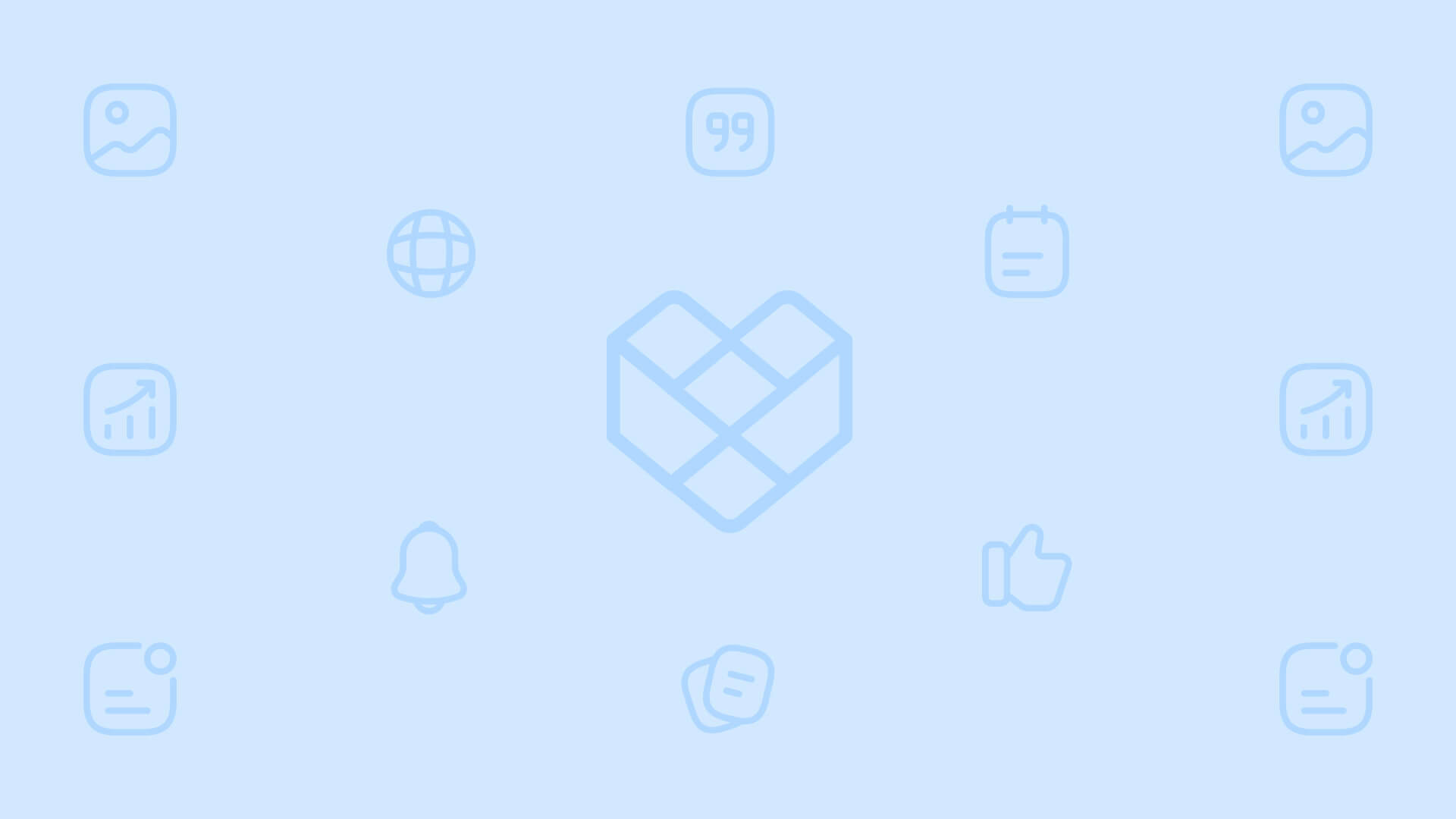
Empower your business, every step of the way
Simplify operations, scale smarter, and deliver better experiences with solutions designed to grow with your business
Take your warehouse management to the next level
Experience hassle-free inventory management with Fynd WMS, designed to keep your operations efficient and accurate. Book a demo to see how Fynd WMS can boost productivity and profits for your business!
Kickstart your quick delivery website
Experience seamless hyper-local commerce with Fynd Quick—engineered to keep things running smoothly and help you reach customers in record time. Book a demo and see how Fynd Quick can drive efficiency and growth for your business!
Level up your delivery management
See how you can manage deliveries with Fynd TMS, designed to streamline operations and keep your customers delighted. Book a demo with our team and find out how Fynd TMS can boost your efficiency and bottom line!
Take your order management to the next level
Discover how effortless order management can be with Fynd OMS, built to keep things running smoothly and make your customers happy. Book a demo with our team and see how Fynd OMS can help boost your efficiency and profits!
In the rapidly evolving world of e-commerce, efficient warehouse management has become a crucial factor in determining the success of online retailers. As fast and reliable shipping demand grows, e-commerce businesses are under increasing pressure to optimize their warehouse operations to meet customer expectations. A well-designed e-commerce warehouse management system (WMS) is essential for streamlining inventory management, order fulfillment, and shipping processes. It allows businesses to improve efficiency, accuracy, and customer satisfaction.
A comprehensive e-commerce WMS integrates various functions, including inventory tracking, order management, picking and packing, shipping, and returns management. By automating these processes, businesses can reduce manual errors, increase productivity, and gain real-time visibility into their warehouse operations. Moreover, an e-commerce WMS can help companies scale their operations to meet growing demand, expand their product offerings, and enter new markets while maintaining high customer service and satisfaction levels.
This article will explore the key features and benefits of e-commerce warehouse management systems (WMS), including their role in improving inventory management, streamlining order fulfillment, and enhancing customer satisfaction. We will also discuss the latest trends and technologies in WMS, such as artificial intelligence, machine learning, and the Internet of Things (IoT). We will also provide insights into how businesses can select and implement the right WMS solution to meet their unique needs and goals.
What is an E-commerce Warehouse Management System
An E-commerce Warehouse Management System (eWMS) is software designed to streamline and optimize warehouse operations for online retailers. It enhances inventory management, order picking, packing, and shipping processes, ensuring efficient storage and precise order fulfillment. By automating tasks like barcode scanning and inventory tracking, an eWMS minimizes errors and speeds up order processing. It integrates seamlessly with e-commerce platforms, offering real-time inventory updates to prevent overselling and maintain accurate stock levels. This integration facilitates faster order fulfillment, boosts customer satisfaction, and supports handling high order volumes. An eWMS is crucial for e-commerce businesses aiming to improve operational efficiency and scalability while meeting customer demands effectively.
Key Functionalities of a WMS
A Warehouse Management System (WMS) provides key functionalities like inventory management, order picking, and stock replenishment. It tracks inventory in real-time, allowing for precise stock control and reducing the risk of stockouts or overstocking. The system streamlines the picking and packing process by suggesting the most efficient routes and methods, improving accuracy, and reducing fulfillment times.
Additionally, a WMS offers shipping and receiving management, coordinating inbound and outbound logistics. It integrates with carrier systems to automate shipping labels and documentation, ensuring smooth order dispatch. The system can also provide reporting and analytics, offering insights into warehouse performance, inventory levels, and operational efficiency, which supports better decision-making and continuous improvement.
- Inventory Management: Accurate tracking of stock levels, locations, and expiration dates.
- Order Fulfillment: Efficiently process and fulfill customer orders, including picking, packing, and shipping.
- Labour Management: Optimizing workforce utilization and assigning tasks based on skills and availability.
- Receiving and Put-away: Managing the incoming flow of goods, including inspection and storage.
- Putaway Optimization: Determining the best product storage locations based on popularity, size, and weight.
- Cycle Counting: Regularly verifying inventory accuracy to prevent stock discrepancies.
- Reporting and Analytics: Generating insights into warehouse performance and identifying areas for improvement.
Key Benefits of Using a WMS
Using a Warehouse Management System (WMS) offers significant benefits, including enhanced inventory accuracy and reduced operational costs. A WMS minimizes errors like overstocking or stockouts by providing real-time tracking and precise inventory management. This leads to more efficient use of warehouse space and resources, reducing waste and lowering overall storage costs.
A WMS also improves order fulfillment speed and accuracy. It optimizes picking, packing, and shipping processes, ensuring orders are processed faster and with fewer mistakes. This efficiency enhances customer satisfaction by providing timely and accurate deliveries. Additionally, a WMS offers valuable insights through analytics and reporting, enabling better decision-making and continuous improvement in warehouse operations.
1. Enhanced Inventory Accuracy
Real-time tracking and precise inventory management provided by a WMS significantly reduce common errors like overstocking and stockouts. By continuously monitoring inventory levels and movements, businesses ensure that stock levels are accurate and aligned with actual demand, preventing costly discrepancies.
- Minimized Errors: Reduces the likelihood of overstocking and stockouts.
- Precise Management: Provides accurate inventory tracking and updates.
2. Reduced Operational Costs
A WMS enhances the efficient use of warehouse space and resources, which helps lower overall storage costs. By optimizing inventory management and streamlining processes, businesses can reduce waste and improve cost efficiency in their operations.
- Efficient Space Utilization: Maximizes warehouse space and reduces waste.
- Lower Costs: Decreases overall storage and operational costs.
3. Improved Order Fulfillment
A WMS optimizes picking, packing, and shipping processes for incredible speed and accuracy. This leads to quicker order processing and fewer mistakes, ensuring that orders are fulfilled more efficiently and accurately.
- Faster Processing: Accelerates picking, packing, and shipping.
- Increased Accuracy: Reduces errors in order fulfillment.
4. Increased Customer Satisfaction
A WMS facilitates Timely and accurate deliveries through improved order fulfillment processes. This enhances customer satisfaction by meeting or exceeding delivery expectations and providing reliable service.
- Timely Deliveries: Ensures prompt order fulfillment.
- Enhanced Service: Boosts customer satisfaction through reliable performance.
5. Valuable Insights
A WMS provides valuable insights through analytics and reporting, which support better decision-making. By analyzing inventory and operational data, businesses can identify trends, make informed decisions, and drive continuous improvement in warehouse operations.
- Data-Driven Decisions: Offers insights for better decision-making.
- Continuous Improvement: Facilitates ongoing enhancements in operations.
Warehouse Operations Optimization
Warehouse operations optimization maximizes efficiency and productivity by streamlining processes like inventory management, order picking, and shipping. Implementing automated systems, such as a Warehouse Management System (WMS), helps reduce manual errors, speeds up order processing, and enhances inventory accuracy. This allows for faster fulfillment and minimizes delays, directly improving customer satisfaction.
Efficient layout design and workflow processes are crucial for optimization. Organizing the warehouse for optimal product placement and easy access minimizes travel time during picking and packing. Utilizing data analytics also helps identify bottlenecks and improve resource allocation. These strategies lead to a more efficient warehouse, reduced operational costs, and increased productivity.
Some important points to consider:
- Place high-demand items in easy-to-reach locations.
- Use advanced inventory systems to track stock accurately.
- Plan efficient picking routes and ergonomic workstations.
- Integrate technology like WMS and RFID for better operations.
- Continuously improve by using data analysis and lean principles to cut waste.
Inventory Management Strategies
Inventory management strategies are crucial for balancing supply and demand, ensuring that stock levels meet customer needs without overstocking. One practical approach is demand forecasting, which uses historical data and market trends to predict future sales. This helps maintain optimal inventory levels, reducing the risk of stockouts and excess inventory. Just-in-time (JIT) inventory is another strategy that minimizes holding costs by ordering stock only when needed.
Safety stock is also essential in managing unexpected demand fluctuations or supply chain delays, providing a buffer to maintain service levels. Additionally, inventory turnover analysis helps identify slow-moving items, allowing for adjustments in purchasing and promotions. These strategies improve cash flow, reduce storage costs, and enhance customer satisfaction.
1. Demand Forecasting
Demand forecasting involves predicting future customer demand using historical data, market trends, and analytical tools. It helps businesses anticipate sales, plan inventory levels, and make informed purchasing decisions. Accurate forecasting ensures that stock levels align with customer needs, reducing the risk of stockouts or overstocking and ultimately improving operational efficiency and customer satisfaction.
- Historical Data Analysis: Use past sales data to predict future demand patterns.
- Market Trends: Consider external factors like economic conditions, seasonal variations, and competitive activity.
- Customer Behavior: Analyze customer preferences, buying habits, and purchasing cycles.
2. Economic Order Quantity (EOQ)
Economic Order Quantity (EOQ) is a formula used to determine the optimal order size that minimizes total inventory costs, including ordering and holding costs. By calculating the ideal order quantity, businesses can reduce excess inventory, lower storage expenses, and ensure that stock levels meet demand efficiently, leading to cost savings and improved inventory management.
- Optimal Order Size: Determine the ideal quantity to order each time to minimize total inventory costs (ordering and holding costs).
- Factors Considered: Demand rate, ordering cost, and holding cost per unit.
3. Just-in-Time (JIT) Inventory
Just-in-Time (JIT) inventory is a strategy that aims to reduce inventory holding costs by ordering and receiving stock only as it is needed for production or sales. This approach minimizes excess inventory and storage expenses, improves cash flow, and reduces waste, though it requires precise coordination with suppliers and accurate demand forecasting to avoid stockouts.
- Minimal Inventory: Aim to have only the necessary inventory to meet immediate demand.
- Supplier Partnerships: Develop strong relationships with suppliers to ensure timely deliveries.
- Lean Manufacturing: Implement lean principles to reduce waste and improve efficiency.
4. Safety Stock
Safety stock is a buffer of extra inventory to mitigate the risk of stockouts caused by demand fluctuations or supply chain disruptions. By maintaining this reserve, businesses can continue to meet customer demand during unexpected delays or surges, ensuring consistent service levels and reducing the likelihood of lost sales and customer dissatisfaction.
- Buffer Against Uncertainty: Maintain a reserve of inventory to protect against unexpected demand fluctuations or supply disruptions.
- Risk Assessment: Consider factors like lead times, demand variability, and the cost of stockouts.
5. ABC Analysis
ABC Analysis is an inventory management technique that categorizes items into three groups based on their importance and value. "A" items are high-value, low-quantity, requiring tight control; "B" items are moderate in both value and quantity; and "C" items are low-value, high-quantity. This prioritization helps allocate resources effectively and manage inventory efficiently.
- Prioritization: Categorize inventory items based on their value and usage to focus management efforts on the most critical items.
- Selective Control: Implement different inventory control methods for other categories (e.g., tighter control for A items, looser control for C items).
6. Vendor Managed Inventory (VMI)
Vendor-managed inventory (VMI) is a supply chain strategy in which the supplier manages and replenishes inventory at the customer's location. The supplier monitors inventory levels and ensures timely restocking, improving supply chain efficiency, reducing stockouts, and minimizing customer carrying costs. This leads to a more collaborative and streamlined process.
- Supplier Responsibility: Transfer inventory management responsibilities to suppliers.
- Data Sharing: Share demand forecasts and inventory levels with suppliers.
- Efficient Replenishment: Suppliers manage replenishment based on agreed-upon policies.
7. Inventory Turnover
Inventory turnover measures how often inventory is sold and replaced over a period. A higher turnover ratio indicates efficient inventory management and strong sales performance as products move quickly through the supply chain. This metric helps businesses assess how well they manage stock levels and can inform decisions on ordering and pricing strategies.
- Measure Efficiency: Calculate inventory turnover to assess how efficiently inventory is used.
- Optimise Performance: Strive for a healthy inventory turnover ratio to avoid excess stock and minimize holding costs.
8. Technology Solutions
Technology solutions in inventory management involve software and automation tools to streamline processes like tracking, forecasting, and replenishment. Solutions such as Warehouse Management Systems (WMS), barcode scanning, and real-time analytics enhance accuracy, reduce manual errors, and improve efficiency. These technologies enable better decision-making and optimize inventory control across the supply chain.
- Warehouse Management Systems (WMS): Track inventory levels, manage storage locations, and optimize order fulfillment.
- Radio Frequency Identification (RFID): Improve inventory accuracy and visibility.
- Demand Planning Software: Use advanced analytics to forecast demand and optimize inventory levels.
Order Fulfillment Process
The order fulfillment process begins when a customer places an order, which is then received and processed by the warehouse management system. The order is verified for inventory availability, and a picking list is generated. Warehouse staff then locate and pick the items from inventory and pack them securely for shipment. This stage ensures that the order is accurate and ready for delivery.
Once packed, the order is handed off to a shipping carrier for delivery. The system updates the order status and tracking information, which is communicated to the customer. Efficient management of this process ensures timely delivery and enhances customer satisfaction by providing transparency and reliable service.
Order fulfillment covers processing, picking, packing, and shipping to ensure timely and accurate delivery.
- Ensure accurate picking and packing of orders.
- Speed up processing to meet customer deadlines.
- Control shipping costs and manage inventory smartly.
- Provide vital customer service throughout.
- Use technology like WMS to improve operations.
Warehouse Automation and Technology: Driving Efficiency and Productivity
Warehouse automation and technology are critical drivers of efficiency and productivity in modern supply chains. Automated systems like robotic picking, conveyor belts, and automated guided vehicles (AGVs) reduce human error and increase order accuracy, leading to faster fulfillment. These technologies also optimize space utilization and streamline inventory management.
Implementing advanced software solutions, such as warehouse management systems (WMS) and artificial intelligence (AI), further enhances operations. WMS offers real-time inventory tracking and order processing, while AI analyzes data to predict demand and optimize workflow. Together, these technologies significantly improve overall warehouse performance, reducing costs and increasing customer satisfaction.
Benefits of Warehouse Automation
Warehouse automation offers significant benefits, including increased efficiency and reduced operational costs. Automated systems like robotic picking and conveyor belts speed up order fulfillment, minimize human error, and improve accuracy, leading to faster processing times and higher customer satisfaction. Additionally, automation optimizes space utilization and inventory management. Advanced software solutions like warehouse management systems (WMS) provide real-time tracking, ensuring accurate stock levels and reducing the risk of overstocking or stockouts. These benefits collectively enhance productivity, lower labor costs, and enable businesses to handle higher volumes without compromising quality.
- Increased Efficiency: Automated systems speed up order fulfillment and reduce processing times.
- Reduced Operational Costs: Lower labor costs and minimized human error contribute to cost savings.
- Enhanced Accuracy: Improved accuracy in picking, packing, and shipping.
- Optimized Space Utilization: Better use of warehouse space through automation.
- Improved Inventory Management: Real-time tracking helps avoid overstocking and stockouts.
Warehouse Management System (WMS) Software Options
Warehouse Management System (WMS) software has various options for business needs. Some popular WMS software includes SAP Extended Warehouse Management, Oracle WMS, and Manhattan Associates. These systems offer comprehensive features like real-time inventory tracking, order processing, and advanced analytics to optimize warehouse operations. They are suitable for large enterprises requiring integration with other business systems.
For small to medium-sized businesses, options like Fishbowl, Zoho Inventory, and ShipBob provide essential WMS functionalities at a lower cost. They offer inventory management, order fulfillment, and shipping integration, making them accessible for businesses with more straightforward needs while improving warehouse operations' efficiency and accuracy.
Here are some popular WMS software options:
1. Cloud-Based WMS
Cloud-based WMS offers flexibility and scalability by providing real-time access to warehouse data from any location. It reduces the need for on-premises infrastructure, lowering costs and simplifying system updates. Features like inventory tracking, order management, and reporting are easily accessible, making it an ideal solution for businesses looking to streamline operations efficiently.
- SAP EWM: A comprehensive WMS solution from SAP, offering advanced features like slotting optimization and automated guided vehicle (AGV) integration.
- Manhattan Associates provides warehouse management solutions, including a Warehouse Management System (WMS) and a Labor Management System (LMS).
- Oracle Warehouse Management: A cloud-based WMS solution from Oracle offering features like demand forecasting, labor management, and mobile picking.
- Infor WMS: A scalable WMS solution that can be customized to meet specific business needs.
2. On-Premises WMS
On-premises WMS provides robust control and customization, installed directly on a company’s local servers. This option allows for greater data security and system customization to fit specific operational needs. While offering reliable performance, it requires a higher upfront investment and ongoing maintenance, making it suitable for businesses with complex or highly specialized warehouse operations.
- RedPrairie WMS: A popular on-premises WMS solution focusing on supply chain visibility and performance.
- JDA Warehouse Management: A comprehensive WMS solution from JDA Software, offering features like demand sensing, labor optimization, and transportation management.
- Intactix WMS: An on-premises WMS solution focusing on flexibility and scalability.
3. Open-Source WMS
Open-source WMS provides a budget-friendly and customizable option for managing warehouse operations. With access to the source code, businesses can tailor the system to meet their specific requirements without the constraints of licensing fees. This flexibility allows for modifications and enhancements, but it typically requires in-house technical expertise for setup, customization, and maintenance, making it ideal for companies with specific operational needs and IT resources.
- OpenWMS: A free and open-source WMS platform that can be customized to meet specific requirements.
- Odoo Warehouse Management: A module within the Odoo ERP suite offering WMS functionality as part of a broader business solution.
Factors to Consider When Choosing a WMS
When selecting a WMS, scalability is crucial to accommodate future growth and changing business needs. The system should integrate seamlessly with existing software, like ERP and e-commerce platforms, to ensure smooth data exchange. Key features include real-time inventory tracking, order management, and analytics, which enhance operational efficiency and decision-making.
Cost considerations extend beyond the initial purchase, including implementation, training, and ongoing maintenance fees. User-friendliness is essential; a system with an intuitive interface reduces the learning curve and improves adoption rates. Additionally, the level of customer support and training should be evaluated, as these can significantly impact the effectiveness of the WMS and the speed of resolving potential issues during and after implementation.
- Functionality: Ensure the WMS offers the needed features, such as inventory management, order fulfillment, and labor management.
- Scalability: Consider your business's growth plans and choose a WMS for future expansion.
- Integration: Ensure the WMS can integrate with your existing systems, such as your ERP or transportation management system.
- Cost: Evaluate the initial cost and ongoing maintenance costs of the WMS.
- Support: Consider the level of support provided by the WMS vendor.
WMS Implementation and Integration
WMS implementation and integration require careful planning for a seamless transition. Begin with a thorough analysis of current warehouse processes to identify areas for improvement. Develop a clear implementation plan that includes data migration, system configuration, and staff training. Engaging stakeholders early ensures the WMS aligns with business goals and minimizes disruption during the transition.
Integrating existing systems like ERP and e-commerce platforms is crucial for efficient operations. A successful integration ensures real-time data flow, reducing errors and improving inventory visibility. Testing the system in stages allows for identifying and resolving issues early, providing a smooth go-live process. Continuous support and training further facilitate adaptation and long-term success.
1. Critical Steps in WMS Implementation
Critical steps in WMS implementation include conducting a thorough needs assessment, selecting the right system based on business requirements, and developing a detailed project plan. Key phases involve data migration, system configuration, and integration with existing platforms. Rigorous testing, staff training, and change management are essential for a smooth transition and successful adoption of the new system.
Needs Assessment
Needs assessment involves evaluating current warehouse operations and identifying specific requirements to ensure the WMS aligns with business goals. This process helps determine essential features, potential improvements, and integration needs, guiding the selection and implementation of the most suitable system.
- Identify specific business objectives and challenges.
- Determine the required functionality and features of the WMS.
Vendor Selection
Vendor selection involves evaluating and choosing a WMS provider based on system capabilities, integration options, cost, and support services. The goal is to select a vendor that best meets the organization’s operational needs and budget constraints.
- Evaluate WMS software options based on functionality, cost, scalability, and support.
- Conduct vendor demonstrations and reference checks.
Data Migration
Data migration involves transferring existing warehouse data into the new WMS, ensuring accuracy and integrity. This process includes mapping data fields, cleansing data, and validating the transfer to prevent disruptions and ensure a smooth transition to the new system.
- Extract and transform data from existing systems (e.g., ERP, inventory management).
- Load the data into the WMS.
Configuration
Configuration involves setting up the WMS to align with your specific operational processes and business rules. This includes defining workflows, customizing user interfaces, and adjusting system settings to ensure the software effectively supports your warehouse management needs.
- Customize the WMS to match your business processes and workflows.
- Configure settings for inventory, picking, packing, shipping, and other relevant areas.
User Training
User training equips staff with the skills to use the new WMS effectively. This involves hands-on instruction, tutorials, and support to ensure employees understand system functions, workflows, and best practices, which facilitates a smoother transition and minimizes operational disruptions.
- Provide comprehensive training to warehouse staff on how to use the WMS effectively.
- Develop user manuals and documentation.
Testing and Go-Live
Testing and going live involve validating the WMS through rigorous trials to ensure all functions work as expected. This phase includes resolving issues, confirming data accuracy, and ensuring system stability before officially launching the WMS for full operational use.
- Conduct thorough testing to identify and resolve any issues.
- Implement a phased go-live approach to minimize disruption.
Post-Implementation Support
Post-implementation support provides ongoing assistance to address any issues, ensure system performance, and assist with troubleshooting. It includes regular updates, user helpdesk services, and continuous training to optimize the WMS and adapt to evolving business needs.
- Provide ongoing support and maintenance to address any problems and ensure optimal performance.
2. Integration with Other Systems
Integration with other systems involves connecting the WMS with existing software, such as ERP and e-commerce platforms, to ensure seamless data flow and operational efficiency. This process requires configuring interfaces, mapping data fields, and testing connectivity to facilitate real-time updates and prevent discrepancies, ultimately enhancing overall warehouse and business operations.
- Enterprise Resource Planning (ERP): Integrate the WMS with your ERP system to synchronize inventory, orders, and customer information data.
- Transportation Management System (TMS): Integrate the WMS with your TMS to streamline shipping processes and optimize transportation costs.
- Radio Frequency Identification (RFID): Integrate RFID technology with the WMS to track real-time inventory and assets.
- Electronic Data Interchange (EDI): EDI exchanges electronic documents with suppliers and customers.
3. Challenges and Considerations
Challenges in WMS implementation include managing data migration, ensuring seamless integration with existing systems, and adapting to new workflows. Considerations involve selecting the right vendor, addressing potential resistance to change, and providing thorough training. Careful planning and ongoing support are crucial to overcoming these challenges and ensuring a successful WMS deployment.
- Data Quality: Ensure accurate and up-to-date data to avoid inconsistencies and errors.
- Change Management: Address resistance to change and effectively communicate the benefits of the WMS.
- Customization: Balance customization with standard functionality to avoid excessive costs and complexity.
- Integration Complexity: Carefully plan and execute integration with other systems to avoid disruption
Training and Support WMS Success
Training and support are crucial for WMS success, ensuring users are confident and proficient in using the system. Comprehensive training should include hands-on sessions, tutorials, and role-specific guidance covering all aspects of the WMS. This prepares staff to navigate the system effectively, reducing errors and improving efficiency in daily operations.
Ongoing support is equally important, providing users with assistance for troubleshooting and system updates. A responsive support team helps address technical issues quickly, minimizing downtime. Regular refresher training and system enhancements keep users updated on new features, ensuring the WMS meets evolving business needs and contributes to sustained operational success.
1. Training
Training is essential for ensuring users are proficient with the WMS, reducing errors, and boosting efficiency. It includes hands-on instruction, tutorials, and role-specific guidance tailored to the needs of different user groups. Practical training prepares staff to fully utilize the system's features, facilitating a smoother transition and enhancing overall warehouse operations.
- Needs Assessment: Identify the specific training needs of different organizational roles.
- Customized Training: Develop training programs tailored to employees' roles and skill levels.
- Hands-On Experience: Provide opportunities for employees to practice using the WMS in a simulated environment.
- Ongoing Training: Offer ongoing training and updates as the WMS evolves or new features are introduced.
- Documentation: Create comprehensive user manuals and documentation to support training and reference.
2. Support
Support is vital for maintaining WMS efficiency and offering assistance for troubleshooting, technical issues, and system updates. A responsive support team ensures quick problem resolution, minimizing operational disruptions. Continuous support includes providing user helpdesk services, implementing system enhancements, and offering refresher training, ensuring the WMS adapts to changing business needs and performs optimally.
- Help Desk or Support Center: Establish a dedicated support channel for users to seek assistance.
- Response Time: Ensure timely and effective responses to user inquiries and issues.
- Remote Support: Provide remote access and troubleshooting capabilities to resolve problems quickly.
- Regular Check-Ins: Conduct periodic check-ins with users to gather feedback and identify areas for improvement.
- Proactive Maintenance: Implement proactive maintenance and updates to prevent issues and ensure optimal performance.
Metrics and Performance Monitoring in WMS
Metrics and performance monitoring in WMS are crucial for evaluating warehouse efficiency and identifying areas for improvement. Key performance indicators (KPIs) such as order accuracy, pick-and-pack rates, and inventory turnover provide insights into operational effectiveness. Regularly tracking these metrics helps optimize workflows, reduce errors, and ensure timely order fulfillment.
Advanced WMS systems offer real-time data analytics and reporting features, enabling managers to make informed decisions quickly. By monitoring metrics like stock levels, lead times, and labor productivity, businesses can adjust strategies proactively to meet demand and improve customer satisfaction. Continuous performance monitoring ensures the WMS remains aligned with business goals, driving overall operational success.
1. Inventory Management Metrics
Inventory management metrics like turnover, stock accuracy, and order cycle time are essential for evaluating warehouse efficiency. These metrics help understand how quickly stock is sold and replaced, ensuring optimal inventory levels. Regular monitoring helps prevent overstocking or stockouts, improving order fulfillment and overall operational performance.
- Inventory Accuracy: Measure the accuracy of inventory records to minimize stock discrepancies.
- Inventory Turnover: Calculate the rate at which inventory is sold or used to assess efficiency.
- Stockout Rate: Track the frequency of stockouts to identify items that need more attention.
- Obsolete Inventory: Monitor the amount of outdated or slow-moving inventory.
2. Order Fulfillment Metrics
Order fulfillment metrics, such as order accuracy, pick and pack speed, and on-time delivery rates, are crucial for assessing efficiency and customer satisfaction. These metrics provide insights into how effectively orders are processed and shipped, helping identify areas for improvement to ensure timely and accurate deliveries enhancing customer experience.
- Order Accuracy: Measure the accuracy of order picking, packing, and shipping.
- Order Cycle Time: Track the time it takes to fulfill an order from receipt to shipment.
- On-Time Delivery Rate: Measure the percentage of orders delivered on time.
- Customer Satisfaction: Gather customer feedback to assess their satisfaction with the order fulfillment process.
3. Labor Efficiency Metrics
Labor efficiency metrics, like units picked per hour and order processing time, help evaluate workforce productivity in the warehouse. Monitoring these metrics identifies bottlenecks and areas where training or process improvements are needed. Improving labor efficiency leads to faster order fulfillment, reduced costs, and a more streamlined operation.
- Labor Productivity: Measure the amount of work completed per labor hour.
- Labor Utilization: Track the percentage of time employees are actively engaged in productive tasks.
- Overtime Hours: Monitor overtime usage to identify potential workload imbalances.
- Employee Turnover: Track employee turnover rates to assess job satisfaction and retention.
4. Space Utilization Metrics
Space utilization metrics, such as storage density and occupancy rates, assess how effectively warehouse space is used. By tracking these metrics, businesses can optimize layout and storage methods, ensuring maximum use of available space. Improved space utilization reduces storage costs and enhances overall warehouse efficiency and workflow.
- Storage Capacity: Measure the amount of available storage space.
- Space Utilization Rate: Calculate the percentage of available space that is occupied.
- Cube Utilization: Assess how efficiently space is used in terms of volume.
5. Cost Metrics
Cost metrics, including cost per order, storage, and handling costs, are essential for evaluating warehouse financial performance. Tracking these metrics helps identify areas where expenses can be reduced, such as optimizing labor and space. Effective cost management ensures more efficient operations and improves the warehouse's profitability.
- Inventory Carrying Costs: Calculate the costs associated with holding inventory (e.g., storage, insurance, obsolescence).
- Order Fulfillment Costs: Measure the costs of picking, packing, and shipping orders.
- Labor Costs: Track labor expenses and identify areas for cost reduction.
- Equipment Costs: Monitor the costs of maintaining and operating warehouse equipment.
6. Technology Performance Metrics
Technology performance metrics, such as system uptime, response time, and error rates, measure the effectiveness of WMS and other warehouse technologies. Monitoring these metrics ensures that systems are reliable and functioning optimally. High performance minimizes disruptions, enhances productivity, and supports smooth, efficient warehouse operations.
- System Uptime: Measure the percentage of time the WMS system is operational.
- Response Time: Track the time it takes for the system to respond to user requests.
- Data Integrity: Ensure the accuracy and consistency of data within the WMS.
Common Challenges in WMS Implementation and Solutions
Common challenges in WMS implementation include data migration issues, integration difficulties, and user resistance. Solutions involve thorough planning, testing data transfer, ensuring seamless system integration, and providing comprehensive training. Proactively addressing these challenges helps ensure a smooth transition and successful adoption of the WMS.
1. Data Quality Issues
Data quality issues, such as inaccuracies and inconsistencies, can hinder WMS effectiveness. To address these problems, implement robust data cleansing procedures, validate data accuracy before migration, and establish ongoing data quality controls. Ensuring high-quality data is essential for reliable system performance and accurate decision-making.
- Challenge: Inaccurate or incomplete data can lead to errors and inefficiencies.
- Solution: Implement data cleansing and validation processes, ensure data accuracy during entry, and regularly audit data quality.
2. Resistance to Change
Resistance to change occurs when individuals or teams hesitate to adopt new processes or technologies, such as implementing a WMS. This can stem from fear of the unknown, comfort with current methods, or lack of understanding. Addressing resistance requires clear communication, training, and involving stakeholders in the transition process to foster acceptance and ease adaptation.
- Challenge: Employees may only accept implementing a new system if it requires changes to their work processes.
- Solution: Communicate the WMS's benefits, provide adequate training, and involve employees in the implementation process.
3. Integration Challenges
Integration challenges arise when connecting a WMS with existing systems like ERP or e-commerce platforms. Issues can include data compatibility, complex workflows, and system inconsistencies. Overcoming these challenges requires careful planning, thorough testing, and using middleware or APIs to ensure seamless data exchange and functionality, resulting in a cohesive and efficient operational system.
- Challenge: Integrating the WMS with other systems (e.g., ERP, TMS) can be complex and time-consuming.
- Solution: Plan the integration process carefully, use standardized data formats, and consider hiring a consultant to assist with integration.
4. Scalability Issues
Scalability issues occur when a WMS cannot adapt to growing business demands, such as increased order volume or inventory size. This can lead to performance bottlenecks and inefficiencies. Addressing scalability requires choosing a flexible WMS capable of handling expansion and supporting additional features or integrations to ensure continued smooth operations as the business grows.
- Challenge: The WMS may need help handling future growth or changes in business requirements.
- Solution: Choose a WMS that is scalable and can accommodate future expansion
.
5. Cost Overruns
Cost overruns in WMS implementation can result from underestimating expenses like customization, integration, training, and ongoing maintenance. Unexpected issues during deployment may also increase costs. To mitigate this, develop a detailed budget, including contingency funds, and regularly review expenses against projections to keep the project within financial limits and ensure successful implementation.
- Challenge: The total cost of WMS implementation may exceed the initial budget.
- Solution: Develop a detailed project plan with clear timelines and budgets and regularly monitor costs.
6. Complexity
Complexity in WMS implementation can arise from extensive customization, intricate integration requirements, and adapting to unique operational workflows. This can lead to longer deployment times and user confusion. Simplifying the process by prioritizing essential features, using out-of-the-box solutions when possible, and providing comprehensive training can help manage and reduce complexity effectively.
- Challenge: The WMS may need to be simplified for employees to use effectively.
- Solution: Provide comprehensive training, simplify workflows, and consider customization options.
7. Vendor Selection
Vendor selection for a WMS involves evaluating potential providers based on their system capabilities, industry experience, and integration options. Key factors include cost, scalability, and the quality of customer support. Choosing the right vendor ensures the WMS aligns with business needs, offers reliable performance, and provides ongoing support for a successful implementation and operation.
- Challenge: Choosing the right WMS vendor can be difficult, especially with many available options.
- Solution: Research potential vendors, conduct demos, and consider factors such as functionality, cost, scalability, and support.
8. Data Security
Data security in WMS implementation is crucial to protecting sensitive information, such as inventory data and customer details. This involves implementing robust security measures like encryption, access controls, and regular security audits. Ensuring compliance with data protection regulations safeguards against breaches and maintains the integrity and confidentiality of the warehouse management system.
- Challenge: Ensuring data security and protecting sensitive information is crucial.
- Solution: Implement robust security measures, such as access controls, encryption, and regular backups.
Scalability and Growth
Scalability and growth are vital considerations when implementing a WMS, as the system must handle increasing order volumes, expanding inventory, and additional users. A scalable WMS can adapt to changing business needs without significant overhauls, supporting seamless growth while maintaining performance and efficiency. This flexibility is crucial for businesses anticipating expansion.
Choosing a WMS with scalable architecture ensures it can integrate new technologies and modules as the business evolves. It allows adding features like automation or multi-warehouse management without disrupting existing operations. Investing in a scalable WMS provides long-term value by supporting continuous improvement and accommodating future growth.
1. Capacity Planning
Capacity planning involves forecasting future operational needs to ensure that resources like staff, equipment, and space align with anticipated demand. It includes analyzing current performance, predicting growth trends, and adjusting to accommodate increased workload or expansion. Effective capacity planning helps optimize efficiency, avoid bottlenecks, and ensure seamless scalability of operations.
- Demand Forecasting: Accurately predict future demand to determine the necessary capacity.
- Space Utilization: Optimize existing space to maximize storage capacity.
- Expansion Options: Consider expanding the warehouse by leasing additional space or building a new facility.
2. Infrastructure
Infrastructure refers to the foundational systems and facilities required for efficient operation. It includes physical elements like buildings, equipment, technology, and supporting systems like IT networks and utilities. Robust infrastructure ensures operational reliability, supports scalability, and enhances overall efficiency, enabling organizations to manage resources and adapt to changing demands effectively.
- Equipment: Invest in appropriate equipment for increased volumes, such as additional forklifts, conveyors, or automated systems.
- Technology: Ensure that the Warehouse Management System (WMS) and other technologies can support expanded operations.
- Utilities: Verify that the warehouse has sufficient utilities (e.g., power, water) to handle increased demand.
3. Labor
Labor encompasses the workforce required to execute tasks and maintain operations, including skilled and unskilled roles. Effective labor management involves recruiting, training, and scheduling staff to optimize productivity and meet operational demands. Ensuring adequate staffing levels and ongoing support and development are crucial for achieving operational efficiency and maintaining a productive work environment.
- Staffing: Hire additional staff or retrain existing employees to meet the increased workload.
- Shift Scheduling: Optimize shift schedules to ensure adequate coverage during peak times.
- Automation: Consider automating tasks to improve efficiency and reduce labor costs.
4. Process Optimization
Process optimization involves refining workflows and procedures to enhance efficiency, reduce waste, and improve overall performance. Organizations can streamline operations, boost productivity, and lower costs by analyzing current processes, identifying bottlenecks, and implementing improvements. Continuous evaluation and adjustment ensure that processes remain effective and aligned with evolving business needs.
- Lean Principles: Implement lean principles to eliminate waste and improve efficiency.
- Workflow Optimization: Streamline workflows to minimize handling and reduce processing time.
- Technology Integration: Leverage technology to automate tasks and improve accuracy.
5. Supply Chain Integration
Supply chain integration involves coordinating and aligning various components, such as suppliers, manufacturers, and distributors, to ensure a seamless flow of goods and information. By integrating systems and processes, businesses can enhance visibility, improve efficiency, and reduce costs. Effective integration fosters collaboration, streamlines operations, and optimizes supply chain performance.
- Supplier Relationships: Strengthen relationships with suppliers to ensure reliable supply and avoid stockouts.
- Transportation: Optimize transportation routes and modes to reduce costs and improve delivery times.
- Inventory Management: Implement effective inventory management strategies to avoid excess stock or shortages.
6. Flexibility
Flexibility in business operations refers to the ability to adapt quickly to changes in market conditions, customer demands, or internal processes. It involves implementing agile systems and practices that can accommodate fluctuations in workload, adjust to new technologies, and respond to unforeseen challenges. Flexibility enhances resilience, allowing organizations to remain competitive and efficiently manage dynamic environments.
- Modular Design: Consider a modular warehouse design that can be easily expanded or modified.
- Adaptable Technology: Choose a WMS and other technologies that adapt to changing needs.
- Agile Processes: Develop agile processes that can quickly respond to changes in demand.
Best Practices, Trends, and Emerging Innovations in Ecommerce Warehouse Management Systems (eWMS)
Best practices in eWMS include leveraging automation to streamline order processing and reduce human error. Implementing real-time inventory tracking and integrating with e-commerce platforms ensures accurate stock levels and efficient order fulfillment. Additionally, advanced analytics helps optimize inventory levels and forecast demand, improving overall warehouse efficiency.
Current trends and emerging innovations in eWMS focus on incorporating artificial intelligence and machine learning for predictive analytics and enhanced decision-making. Robotics and automation, including autonomous mobile robots (AMRs), are increasingly used for picking and packing to speed up processes. Furthermore, cloud-based solutions provide flexibility and scalability, enabling warehouses to adapt quickly to changing business needs and integrate seamlessly with other systems.
1. Best Practices
Best practices in eWMS involve automating key processes to reduce manual errors and improve efficiency. This includes real-time inventory tracking, integrating with e-commerce platforms for accurate stock management, and using data analytics for demand forecasting. Streamlining workflows and ensuring seamless communication between systems enhance operational effectiveness and customer satisfaction.
- Order Fulfillment Speed: Prioritize fast and accurate order fulfillment to meet customer expectations.
- Inventory Accuracy: Maintain high accuracy to avoid stockouts and minimize shipping errors.
- Returns Management: Streamline returns processes to provide excellent customer service and reduce costs.
- Peak Season Planning: Optimize inventory levels and staffing to prepare for peak seasons (e.g., holiday shopping).
- Customer Satisfaction: Focus on customer satisfaction by providing timely updates, accurate tracking, and resolving issues promptly.
2. Industry Benchmarks
Industry benchmarks for eWMS typically include metrics such as order accuracy rates, inventory turnover, and picking efficiency. Achieving high benchmarks involves maintaining order fulfillment accuracy above 98%, optimizing inventory turnover ratios, and reducing picking times. These standards ensure operational excellence, improve customer satisfaction, and enhance warehouse performance.
- Order Accuracy Rate: Strive for high order accuracy rates to minimize returns and customer dissatisfaction.
- Average Order Fulfillment Time: Benchmark order fulfillment times against industry standards and competitors.
- Return Rate: Track the return rate and identify areas for improvement in product quality, packaging, or customer experience.
- Customer Satisfaction Ratings: Gather customer feedback to assess their satisfaction with the e-commerce experience.
- Net Promoter Score (NPS): Measure customer loyalty and willingness to recommend your brand.
3. Emerging Trends and Innovations
Emerging trends in eWMS include the integration of artificial intelligence and machine learning for predictive analytics and enhanced decision-making. Innovations such as autonomous mobile robots (AMRs) and advanced robotics streamline picking and packing processes, while cloud-based solutions offer scalability and flexibility. These advancements drive greater efficiency and adaptability in modern warehouse operations.
- Artificial Intelligence (AI) and Machine Learning: AI can be used for demand forecasting, inventory optimization, and automated decision-making.
- Robotics and Automation: Robotics can automate tasks such as picking, packing, and sorting, improving efficiency and reducing costs.
- Micro-Fulfillment Centers: Small-scale warehouses closer to customers can reduce delivery times and costs.
- Omnichannel Fulfillment: Integrate e-commerce fulfillment with brick-and-mortar stores to offer flexible delivery options.
- Sustainable Practices: Implement sustainable practices, such as reducing packaging waste and optimizing transportation routes.
4. Specific Trends in E-commerce WMS
Specific trends in e-commerce WMS include adopting real-time data analytics for improved inventory management and demand forecasting. The use of artificial intelligence and machine learning enhances order processing and personalization. Additionally, integrating automation technologies, like robots and automated sortation systems, speeds up fulfillment and accuracy.
- Last-Mile Delivery: Optimize last-mile delivery strategies to provide fast and convenient delivery options.
- Subscription-Based Models: Manage inventory and fulfillment for subscription-based businesses effectively.
- Personalization: Use data analytics to personalize product recommendations and improve customer experience.
- Returns Management: Implement efficient returns management processes to minimize costs and improve customer satisfaction.
- Peak Season Planning: Develop strategies, such as temporary staffing or additional warehouse space, to handle peak season demand.
E-commerce warehouse Execution System software
E-commerce Warehouse Execution System (WES) software optimizes warehouse operations to meet the rapid pace of online retail. It acts as an intermediary between Warehouse Management Systems (WMS) and warehouse automation, coordinating tasks like order picking, packing, and shipping. WES software streamlines the flow of goods and manages resources in real time, ensuring efficient order fulfillment.
This system enhances productivity by integrating various automation technologies, such as conveyors, sorters, and robotics. It dynamically prioritizes tasks, allocates resources, and monitors performance to minimize delays. By optimizing inventory movement and reducing bottlenecks, e-commerce WES software improves accuracy and speed, leading to faster delivery times and higher customer satisfaction.
1. Fynd WMS
Fynd WMS is an e-commerce-focused Warehouse Execution System that delivers real-time inventory management and seamless order processing. It integrates effortlessly with multiple sales channels, optimizing warehouse operations for higher accuracy and faster fulfillment.
- Real-time inventory tracking
- Seamless order processing
- Integration with multiple sales platforms
- Enhanced accuracy in order fulfillment
2. Manhattan Active Warehouse Management
Manhattan Active WES is an adaptive warehouse management solution designed specifically for e-commerce. It offers real-time order orchestration, inventory management, and automation to ensure quick and efficient order fulfillment.
- Real-time order orchestration
- Adaptive inventory management
- Automated task execution
- Tailored for e-commerce operations
3. Softeon WES
Softeon WES enhances e-commerce fulfillment centers with dynamic order processing and task interleaving. It integrates with various automation systems, ensuring faster and more accurate order fulfillment in high-volume environments.
- Dynamic order processing
- Task interleaving
- Integration with automation systems
- Ideal for fast-paced e-commerce fulfillment
4. HighJump (Körber)
HighJump, now part of Körber, is a flexible WES that supports e-commerce businesses with features like inventory tracking, order picking, and integration with automation. It enhances efficiency by streamlining complex warehouse processes.
- Flexible inventory tracking
- Order picking optimization
- Seamless automation integration
- Suitable for growing e-commerce warehouses
5. Honeywell Momentum WES
Honeywell Momentum WES optimizes e-commerce warehouse operations through features like automated material handling and dynamic slotting. It aims to improve the speed and accuracy of order consolidation and fulfillment.
- Automated material handling
- Dynamic slotting for efficient storage
- Real-time order consolidation
- Optimized for e-commerce operations
6. Swisslog SynQ
Swisslog SynQ is a modular WES that integrates with automated systems to improve order picking, packing, and shipping. Its scalable solutions cater to the growing demands of e-commerce, ensuring accuracy and speed in fulfillment.
- Modular WES design
- Integration with automated systems
- Optimized order picking and packing
- Scalable for growing e-commerce needs
7. Zebra FulfillmentEdge
Zebra FulfillmentEdge improves e-commerce warehouse operations by optimizing task management and workflow execution. It is designed to meet the needs of fast-paced e-commerce businesses and enhance overall productivity.
- Optimized task management
- Improved workflow execution
- Designed for fast-paced e-commerce operations
- Enhanced warehouse productivity
8. Cimcorp 3D Shuttle
Cimcorp 3D Shuttle offers an automated storage and retrieval system integrated with WES capabilities. It is ideal for e-commerce warehouses that require enhanced order-picking efficiency and accuracy through automation.
- Automated storage and retrieval
- Efficient order-picking
- Integration with WES capabilities
- Suitable for high-demand e-commerce fulfillment
Conclusion
Implementing an e-commerce warehouse management system is crucial for online businesses to streamline operations, enhance efficiency, and improve customer satisfaction. E-commerce warehouse management systems enable businesses to scale quickly and accurately meet growing demands by automating tasks, tracking inventory, and optimizing order fulfillment. With real-time visibility and data-driven insights, companies can make informed decisions, reduce errors, and increase productivity, increasing revenue and competitiveness in the e-commerce market.
Frequently asked questions
An E-Commerce WMS is software that manages and controls the day-to-day operations of an e-commerce warehouse or distribution center, optimizing the storage, handling, and shipping of goods and products.
Key features of an e-commerce WMS include inventory management, order management, picking and packing, shipping, returns management, and real-time visibility into warehouse operations.
An e-commerce WMS improves inventory management by providing real-time visibility into inventory levels, tracking inventory movements, and automating inventory-related tasks such as stock counting and reporting.
Yes, most e-commerce WMS solutions can integrate with popular e-commerce platforms such as Shopify, Magento, and WooCommerce, as well as with other third-party systems such as ERP and CRM systems.
An e-commerce WMS improves order fulfillment by automating the picking and packing process, reducing errors, and increasing the speed and accuracy of order fulfillment.
Many e-commerce WMS solutions can manage multiple warehouses or distribution centers, providing a centralized view of inventory and operations across all locations.